Installation, Program switches, Wiring schematics – Greenheck Advanced Control - MSAC (476373) User Manual
Page 2: Warning, Mounting, Wiring, Low voltage wiring, Torque table, Switch 1, Switch 2
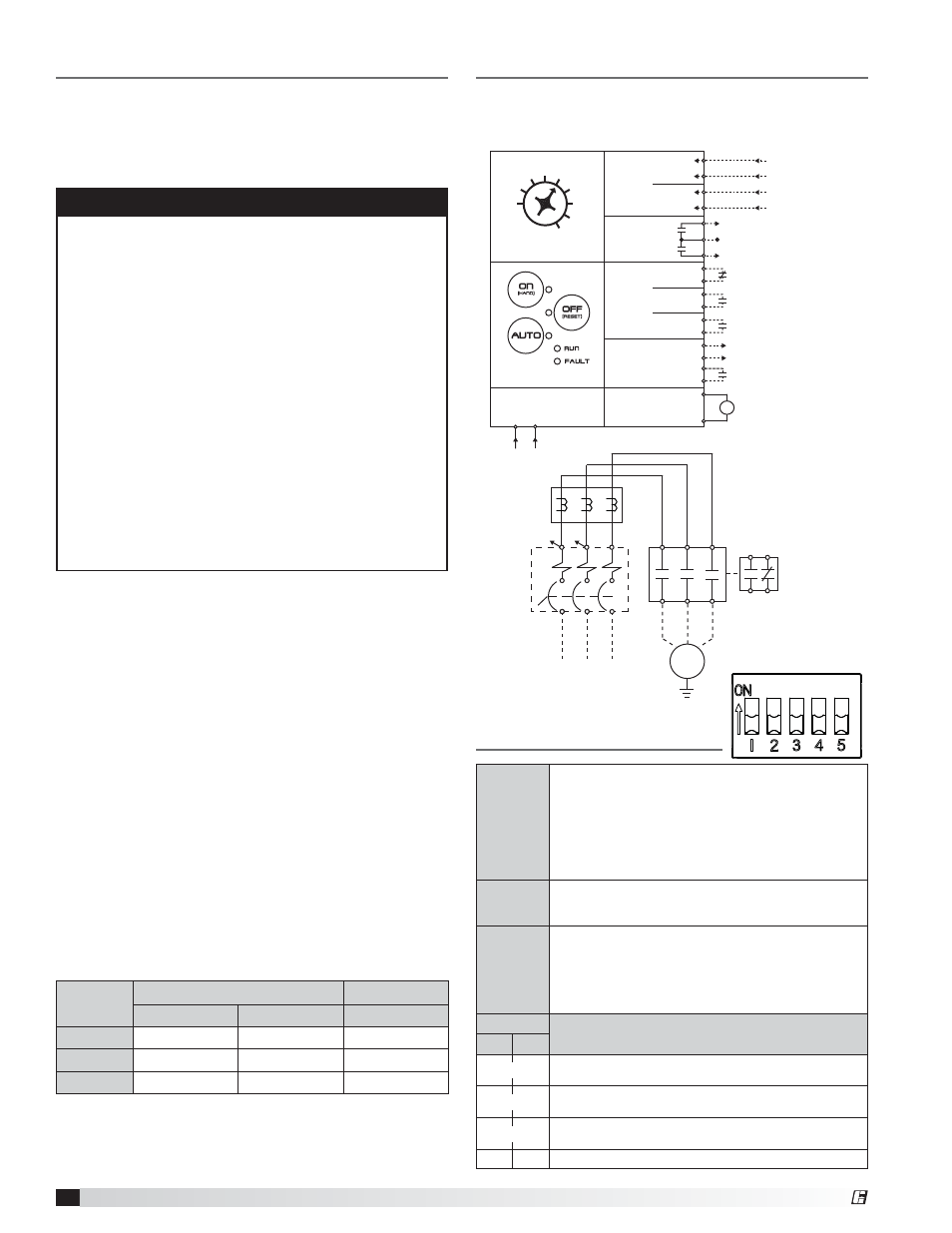
2
Motor Starter Advanced Control
WARNING
• To maintain overcurrent and short circuit protection,
the manufacturer’s instructions for selecting current
elements and setting the instantaneous-trip circuit
breaker must be followed.
• Tripping of the instantaneous-trip circuit breaker
is an indication that a fault current has been
interrupted. Current-carrying components of the
magnetic motor controller should be examined and
replaced if damaged to reduce the risk of fire or
electric shock.
• Do not locate starter in an environment subject to
flammable gases, dusts or materials. Contact arcing
can induce explosion or fire.
• Locate starter in a location appropriate to enclosure
ratings and operational ratings. (e.g. NEMA-1 should
only be located in a dry, protected environment).
• Do not allow any metal shavings or debris from
installation to enter enclosure.
Installation
Mounting
Mount the starter on a vertical surface, with the line
terminals facing up. Install using 1/4-inch diameter
hardware suitable for the mounting surface.
Wiring
Wire main power input and motor leads to the
appropriate terminals tightened to specified torques
indicated in the torque table. Use only copper
conductors rated at least 60°C for applications less
than 100A and at least 75°C ≥ 100A. Maintain proper
clearances and verify that no possibility of an electrical
short exists between the power conductors or
enclosure. Ensure that wires are not under stress and
all insulation is intact. Verify voltage input matches label
and the control power is tapped per schematic.
Low Voltage Wiring
Automation system control wiring should be run in
a separate conduit. The control terminals accept
26~14AWG wire torqued to 3.5 in-lb.
Program Switches
SWITCH
1
Smartstart Bypass: Bypasses the Smartstart features
when on. Smartstart protects the motor by detecting
several common potentially damaging fault conditions.
When Smartstart is active, the starter will shut off
under the following conditions: if locked rotor condition
is present for 0.5 seconds, if the motor takes more
than 10 seconds to start, or if the FLA setting is
determined to be incorrect.
SWITCH
2
Selects overload trip Class 10 when on and overload
trip Class 20 when off. If trip Class 20 is selected
Smartstart is bypassed. Default: ON
SWITCH
3
(ON) - Fault reset: Depress the “OFF” button for 5
seconds to reset a fault trip. Starter will return to “OFF”
mode.
(OFF) - Automatic Fault Reset: The starter will make 3
attempts at an auto fault reset separated by 5 minutes
intervals. Also allows manual reset as above.
SWITCH
Power Fail Modes
4
5
ON
ON
Default Mode - Always return to last mode with no
delay in the event of a power failure.
OFF OFF
Default Mode - Always return to last mode with no
delay in the event of a power failure.
ON
OFF
Always return to last mode with a 10 second delay in
the event of a power failure.
OFF
ON
Upon a power failure, return to off mode.
NEMA
Size
Input (lb-in)
Output (lb-in)
Standard
Combination Motor Leads
00
15.6
18
20
0
15.6
18
20
1
15.6
18
20
Torque Table
Wiring Schematics
Standard product wiring diagram shown. As-built
product wiring may vary. Product wiring diagram located
on starter enclosure.
H1
H4
L3
L1
L2
MTR
T1
T3
AUX
CONT
M
T2
OL
3PH
43
44
31
32
A1
A2
M
Control
Limit Switch
Normally
Open Input
Actuator
Control
24VDC,
1A Output
Dry
Inputs
Relay
Outputs
Common
Fault
Status
Fireman’s
Override
12-250VAC/DC Input
Auto Run
Permissive
Shut Down
Auto Run
12-250VAC/DC Input
Voltage
Inputs
Contactor
Coil
1
FLA (A)
5
10
15
20
25
30
35
40
PCB Power
H1 H4
Keypad
Overload Setting
Normally
Open Input
Normally
Open Input
Normally
Closed Input
MCP
(Optional)
24V
Output to
contactor coil
208-600VAC
60VA Max.
208-600VAC
Input
24VDC output
to 24VAC
contactor coil
®