Installation – Flowserve BA46 User Manual
Page 24
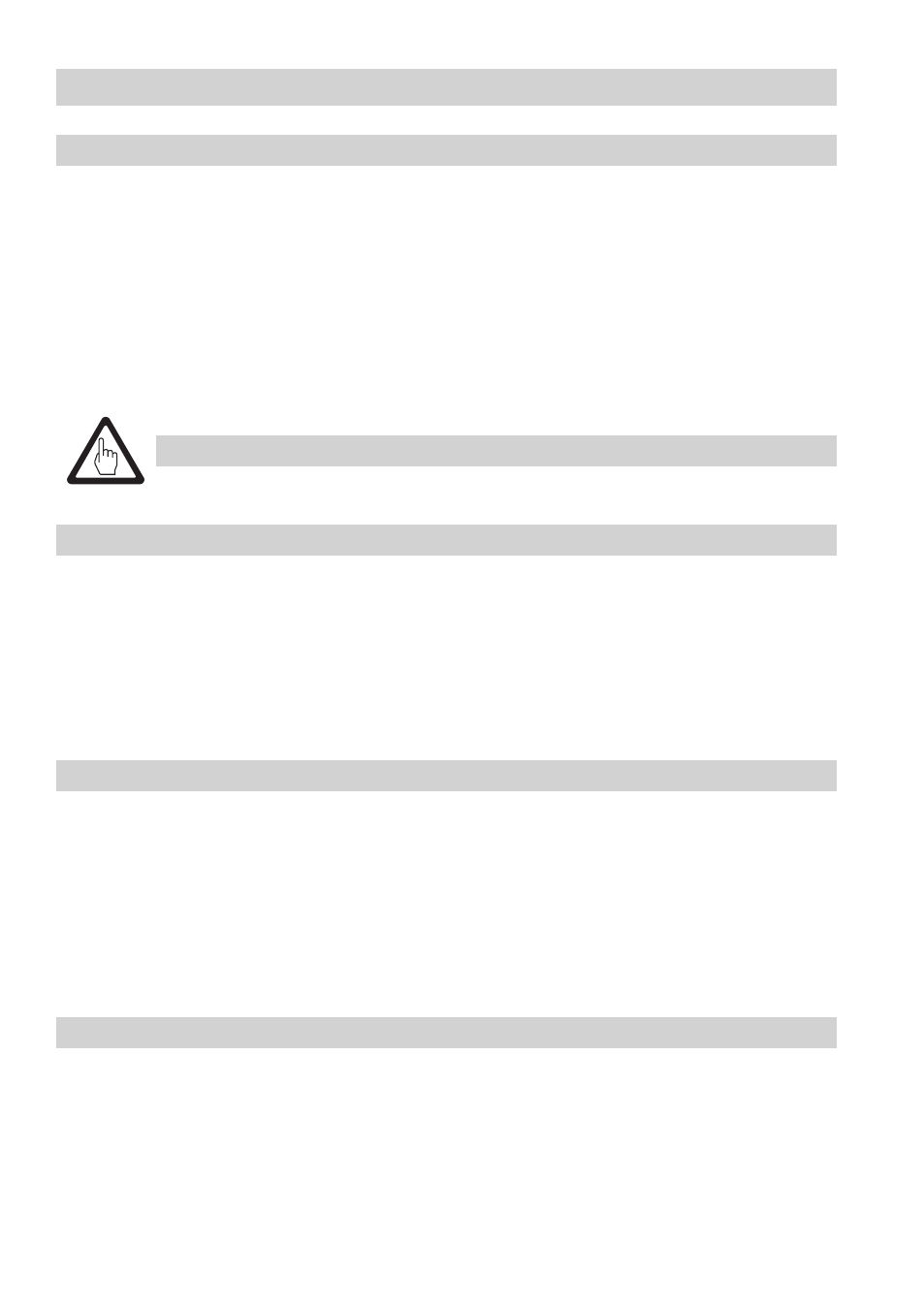
4
Valve with butt-weld ends
. Ensure correct position of installation. The control lever
U
must be freely movable.
. Observe direction of flow. The flow arrow is on the valve body.
3. Consider space required for servicing the valve. When the continuous blowdown valve is installed
a minimum space of at least 80 mm is required for removing the equipment or for the subsequent
installation of the actuator.
4. Remove plastic plugs. They are only used as transit protection.
5. Clean butt-weld ends.
6. Arc-weld trap only manually (welding process and 4 to ISO 4063) or apply gas-welding
process (welding process 3 in accordance with ISO 4063)
Installation
BA 46, BA 47, BAE 46, BAE 47
Mount the continuous blowdown valve, taking the direction of the flow arrow into account. The
blowdown take-off point must be located in the steam boiler underneath the low level mark and close
to the steam outlet. The continuous blowdown valve can be installed in horizontal and vertical
pipes. The continuous blowdown valve is delivered ready for installation, with the actuator mounted
or supplied separately. Before commissioning read the technical documentation provided by the
manufacturer of the actuator and store the document together with the installation manual “BA 46, BA
47, BAE 46, BAE 47” in a sheltered place. The continuous blowdown valve is delivered with a sample
valve (not installed). This sample valve must only be attached to the continuous blowdown valve at the
intended point. Before commissioning read the technical documentation provided by the manufacturer
of the sample valve and store the document together with the installation manual “BA 46, BA 47, BAE
46, BAE 47” in a sheltered place.
Valve with flanged ends
. Ensure correct position of installation. The control lever
U
must be freely movable.
. Observe direction of flow. The flow arrow is on the valve body.
3.
Consider space required for servicing the valve. When the continuous blowdown valve is installed a
minimum space of at least 80 mm is required for removing the equipment or for the subsequent
installation of the actuator.
4.
Remove plastic plugs. They are only used as transit protection
.
5.
Clean seating surfaces of both flanges.
6.
Install the continuous blowdown valve.
Valve with socket-weld ends
. Ensure correct position of installation. The control lever
U
must be freely movable.
. Observe direction of flow. The flow arrow is on the valve body
.
3.
Consider space required for servicing the valve. When the continuous blowdown valve is installed a
minimum space of at least 80 mm is required for removing the equipment or for the subsequent
installation of the actuator
.
4.
Remove plastic plugs. They are only used as transit protection.
5.
Clean socket-weld ends
6.
Arc-weld trap only manually (welding process and 4 to ISO 4063) or apply gas-welding
process (welding process 3 in accordance with ISO 4063)
.
Attention
n
Note that the inclination of the actuator when installed must not exceed 90 °!