Flowserve 5000 Positioner Automax Valve Automation Systems User Manual
Page 5
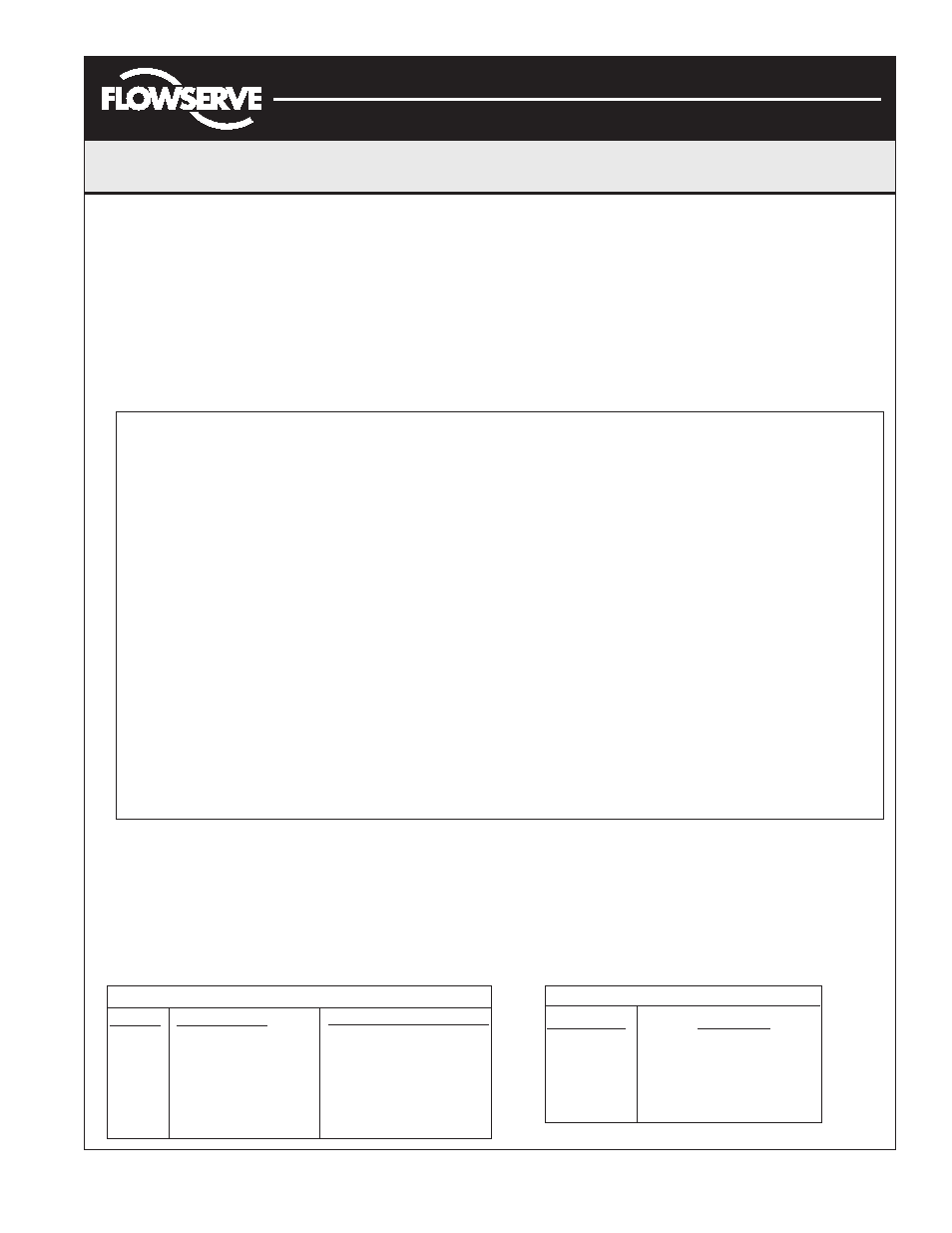
©
2011, Flowserve Corporation, Printed in USA
3-Position Control/Dribble Control
SR Limit Switch Method
Automax Valve Automation Systems
Installation, Operation and Maintenance Instructions
FCD AXAIM0030- 01 (LMR0004-0) (AUTO-30) 03/ 11
Flowserve Corporation
1350 N. Mountain Springs Parkway
1978 Foreman Dr.
Flow Control Division
Springville, Utah 84663-3004
Cookeville, TN 38501
www.flowserve.com
Phone: 801 489 2233
Phone: 931 432 4021
Page 5 of 8
I/P Module Calibration: Caution:
If I/P Module is installed in
explosive atmosphere, disconnect power prior to removing
cover to avoid personal injury.
Figures 3 and 4 (5100, and
5200-5600 respectively) show the locations of zero and
span adjustments.
1. Start with cover removed, supply pressure
connected, and a 4 mA input signal.
2. Turn zero potentiometer (pot) until I/P Module gauge
reads 3 psi.
3. Change input to 20 mA and turn span pot until I/P
Module gauge reads 15 psi.
4. Zero and span adjustments are interactive, so repeat
steps 1 thru 3 as necessary.
5. Replace cover.
I/P Module Troubleshooting (Model 5100 only - consult factory for 5200 & 5400):
Problem
Probable Cause/Solution
I/P Module does not build up full output pressure
1. Improper zero/span setting.
regardless of input:
2. Low bias (see “Bias Adjustment”).
3. Air leakage (check O-Rings & pneumatic diaphragm).
4. Low air supply.
5. Low regulator output (see “Regulator Adjustment”).
I/P Module does not build up any pressure (or does not
build up over bias pressure):
Circuit Board LED not lit:
1. Loose, shorted, or reversed signal connection.
2. Coil connection reversed.
3. Controller board not responding (replace board).
Circuit Board LED lit:
1. Low bias pressure (see “Bias Adjustment”).
2. Air leakage (check o-rings & pneumatic diaphragm).
3. Bad coil connection or bad coil.
4. Dirty or plugged I/P Module filter (clean or replace).
I/P Module puts out excessive pressure at 4 mA:
1. Improper zero/span setting.
2. High bias (see “Bias Adjustment”).
I/P Module output fluctuates:
1. Air leakage (check o-rings & pneumatic diaphragm).
2. Zero or low bias pressure (see “Bias Adjustment”).
Bias Adjustment:
With supply pressure connected and no
input signal, the I/P Module should put out between 2 and
2 1/2 psi. If necessary, turn the bias adjust setscrew
(CW to increase, item 20 figure 3).
Regulator Adjustment:
With supply pressure connected and
input adjusted to 24 mA or 125 percent, the I/P Module
pressure should be between 18 and 20 psi. If necessary, turn
the regulator setscrew (CW to increase, see figure 3). This
adjustment may affect bias pressure, recheck bias pressure
after making adjustment.
Apex Modular Positioning System (AMPS) Options:
The Apex 5000 positioner is also designed to accept modular
output accessories. These “bolt on” easily and require no
housing modification. The following is a list of part numbers
to specify when ordering.
Electrical Output (Feedback) Options
Base No.
Add Cam Option
Suffix Options - Description
KMA
A-Std. Linear Cam
F - 4-20 mA Transmitter
KMA
B-30,45,60,90
G - 1K OHM Feedback Pot.
KMA
C-Characterized
H - 10K OHM Feedback Pot.
KMS
D-60° for butterfly valve
K - 2-SPDT Mechanical Sw.
KMS
M - 2-SPST Proximity Sw.
KMS
N - 2-SPDT Proximity Sw.
Pneumatic Output Options
Part Number
Description
KMFC
Flow Control Module
KMBB
Block/Bleed Module
(Manual Override + lock-out)
KMBBFC
Flow Control + Block/Bleed
Modules