Flowserve 5000 Positioner Automax Valve Automation Systems User Manual
Page 3
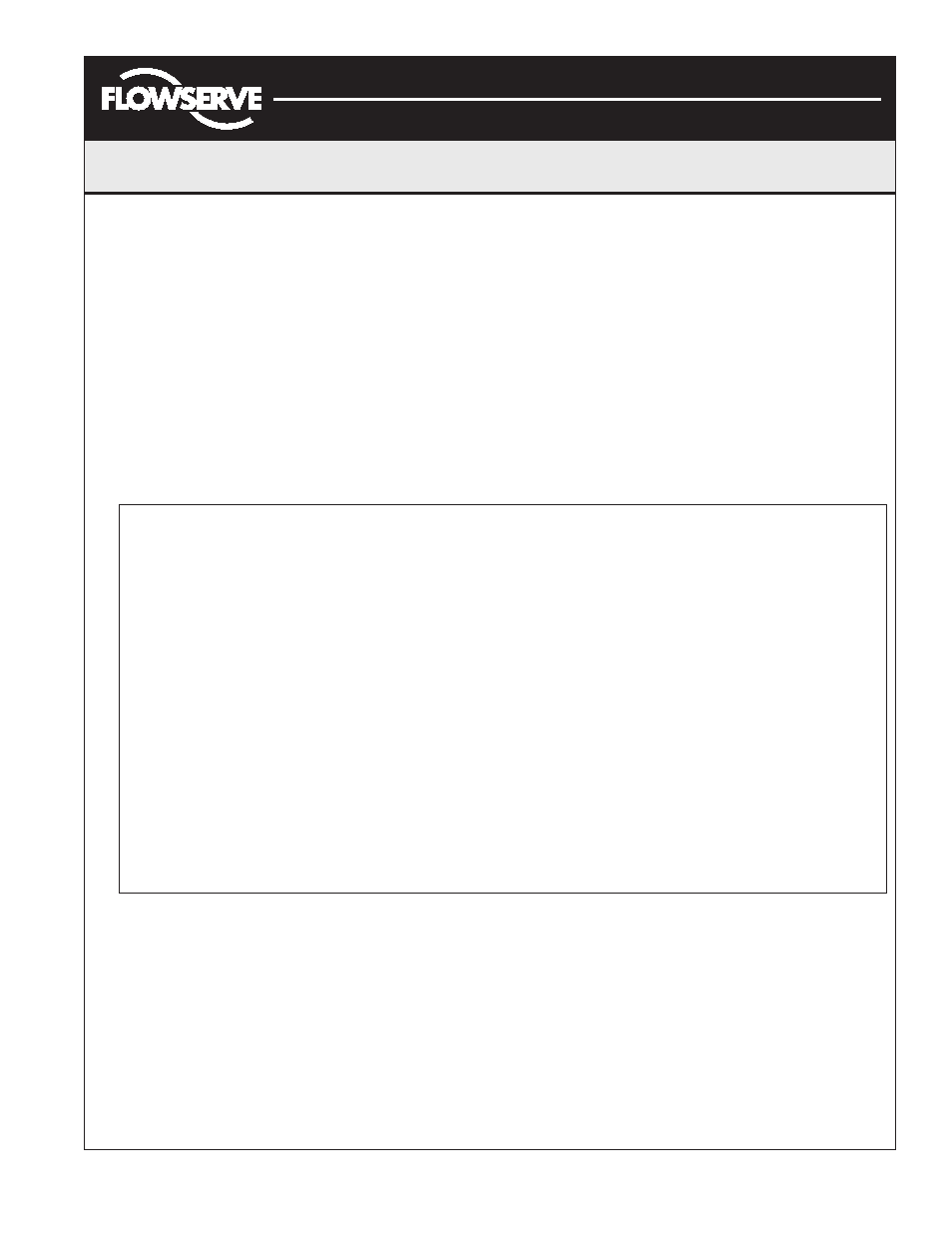
©
2011, Flowserve Corporation, Printed in USA
3-Position Control/Dribble Control
SR Limit Switch Method
Automax Valve Automation Systems
Installation, Operation and Maintenance Instructions
FCD AXAIM0030- 01 (LMR0004-0) (AUTO-30) 03/ 11
Flowserve Corporation
1350 N. Mountain Springs Parkway
1978 Foreman Dr.
Flow Control Division
Springville, Utah 84663-3004
Cookeville, TN 38501
www.flowserve.com
Phone: 801 489 2233
Phone: 931 432 4021
Maintenance:
The Apex 5000 positioner is designed for long life and
trouble-free operation. The following steps should be followed
every six months to assure proper operation.
1. Check air supply and associated filtration
equipment. See “Supply Air Requirements.”
2. Make sure arms, bearings, and adjustment screws
move freely. Caution:
Moving parts to check
freedom with supply pressure connected will cause
rotation of cam. Be sure to keep fingers away from
cam pinch points. If parts do not move freely,
disassemble and lubricate with a light, instrument
grade grease (Lubriplate MAG 1 or equivalent).
3. Check for smooth operation of the spool valve. If
it sticks or feels “gummy”, remove it and clean
both spool and valve bore with solvent. Make
sure both parts are clean and dry before
reinstalling. Do NOT apply grease to these parts.
4. Check for air leaks in air supply.
5. Refer to “Troubleshooting” sections if
maintenance does not cure a problem.
Troubleshooting:
Problem
Probable Cause/Solution
Actuator/Valve won’t stroke or
1. Positioner ports are connected to wrong sides of actuator.
goes full stroke with no control:
2. Cam on wrong side (see “Cam Installation”).
3. Stuck arm or spool valve (see “Maintenance”).
4. Input section problem (see “I/P Module Troubleshooting”).
Calibration Shifts:
1. Loose mounting hardware.
2. Loose cam nut.
3. Loose lockscrews/nut.
Excessive air consumption (other
1. Spool valve gasket leaking or loose screws.
than normal exhaust of 10-30 scfh):
2. Air leak between positioner/actuator or within actuator.
3. If condition occurs at end of stroke only, calibration is incorrect.
Oscillation or hunting:
1. Air leak between positioner/actuator or within actuator.
2. Oversized spool valve (decrease size).
3. Gain setting too high (see “Gain Adjustment”).
Sluggish or slow response:
1. Undersized spool valve (increase size or add volume boosters).
2. Gain setting too low (see “Gain Adjustment”).
3. Tubing restriction (check supply between positioner/actuator).
4. Tubing too small (increase tubing size).
I/P Module:
General:
All I/P Modules are factory calibrated and should not
require adjustment. However, long-term storage or storage in
temperature extremes may affect calibration. The factory-
installed pressure gauge may be used for calibration, but
accuracy is limited (+/- 3 percent).
Ordering Information:
The Apex 5000 Modular Positioning
System (AMPS) allows easy field installation of four input
options. Specify the following for changeover kits (Kits
include modules, mounting hardware [if necessary],
fasteners, and o-ring seals):
KM50
- Change I/P Module input to 3-15 psi pneumatic input.
KM51
- Change to Model 5100 I/P Module.
KM52
- Change to Model 5200 I/P Module.
KM53
- Change to Model 5300 I/P Module.
KM54
- Change to Model 5400 I/P Module.
KM56
- Change to Model 5600 I/P Module.
Page 3 of 8