5 asme valve maintenance – Flowserve Valtek Mark 200 User Manual
Page 5
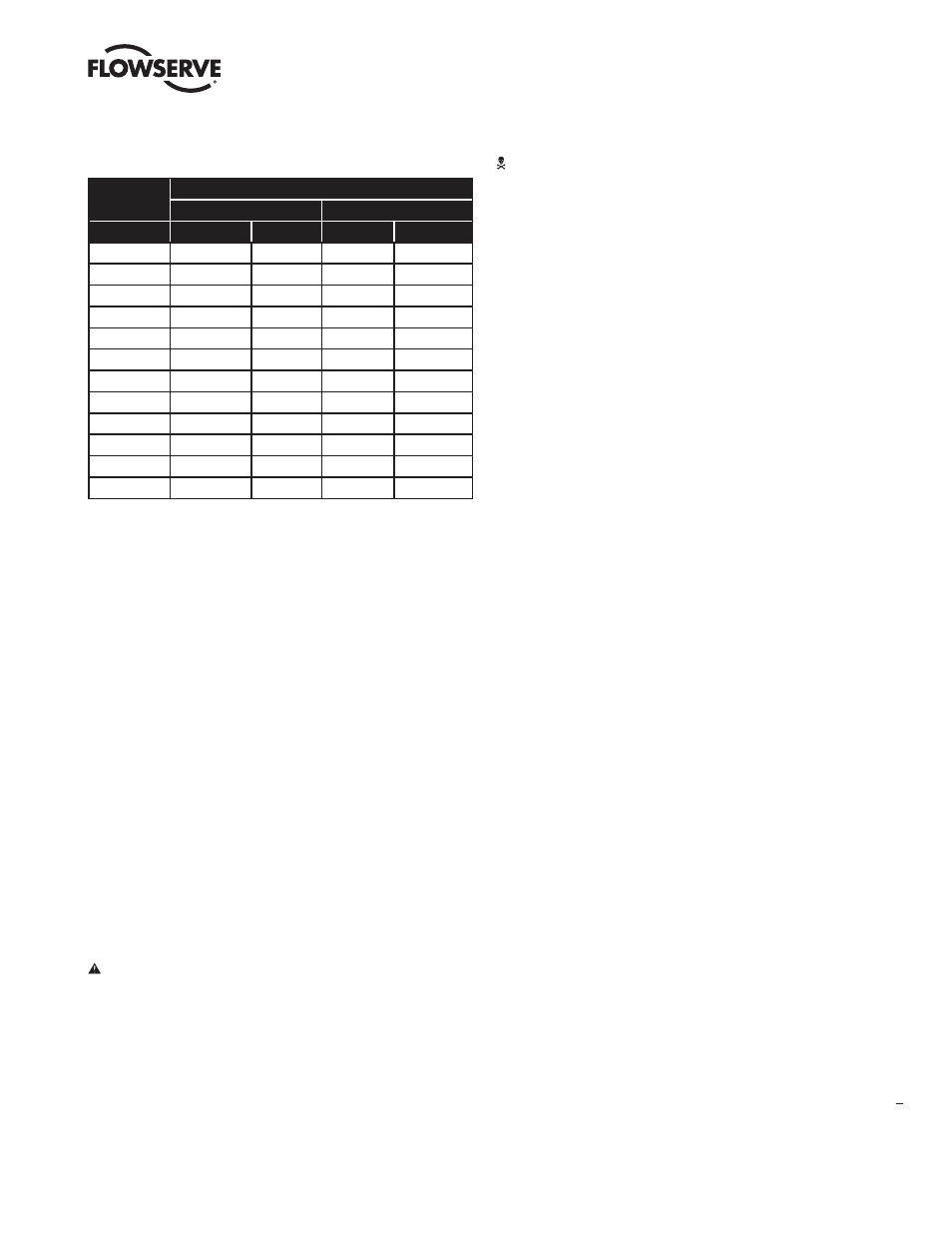
5
Mark 200 Control Valve FCD VLENIM0200– 12/12
flowserve.com
Table 2: Recommended ASME Body Bolt Torque Values
Bolt/Stud Material
Bolt Size
Carbon Steel
Stainless Steel
(inches)
ft lb
N m
ft lb
N m
1-1⁄8
520
691
380
447
1-1/4
730
990
460
624
1-3⁄8
1000
1356
630
854
1-1/2
1320
1790
840
1139
1-5⁄8
1710
2318
1080
1464
1-3⁄4
2170
2942
1400
1898
1-7⁄8
2700
3660
1700
2305
2
3350
4542
2100
2847
2-1/4
4050
5491
2530
3430
2-1/2
4850
6575
3010
4081
2-3⁄4
5900
8000
4400
5960
3
7273
9860
5913
8015
5 ASME Valve Maintenance
At least once every six months, check for proper operation by following
the preventative maintenance steps outlined below. These steps can be
performed while the valve is in-line and, in some cases, without interrupting
service. If an internal problem is suspected, refer to the “Valve Disassembly
and Reassembly” section.
1. Look for signs of gasket leakage through the end flanges and bonnet.
Retorque flange and bonnet bolting (if required). See Table 2.
2. Check for fluid leakage to the atmosphere through the body drain plug, if
applicable.
3. Examine the valve for damage caused by corrosive fumes or process
drippings.
4. Clean valve and repaint areas of severe oxidation.
5. Check packing box bolting for proper tightness. Refer to the packing
installation manual for specific details on maintaining the style of
packing supplied.
CAUTION: Do not overtighten packing. This can cause exces-
sive packing wear and high stem friction that may impede
stem movement.
6. If the valve is supplied with a lubricator fitting, check lubricant supply
and add lubricant if necessary. See product documentation or contact
the Flowserve representative.
7. If possible, stroke the valve and check for smooth, full-stroke operation.
Unsteady stem movement could indicate an internal valve problem.
NOTE: Due to excessive friction, graphite packing can cause the plug
stem to move in a jerky fashion.
WARNING: Keep hands, hair and clothing away from all moving
parts when operating the valve. Failure to do so can cause
serious injury.
8. Make sure positioner linkage and stem clamp or coupling pieces are
securely fastened. If the stem clamp or coupling pieces are loose, check
plug thread engagement (refer to the “Reassembling the Body” section
for the correct procedure on aligning the plug with the seat.) Tighten
stem clamp nut or counter nut.
9. Ensure all accessories, brackets and bolting are securely fastened.
10. If possible, remove air supply and observe actuator for correct fail-safe
action.*
11. Check rubber actuator bellows for splits, cuts or wear.*
12. Check tightness of the actuator. Spray a soap solution around the
cylinder actuator retaining ring, adjusting screw and actuator stem
guide to check for air leaks through the O-rings. *
13. Clean any dirt and other foreign material from the plug stem.
14. If an air filter is supplied, check and replace cartridge if necessary.*
* Pneumatic operated control valves
** Pneumatic operated control valves with safety function