1 din valve quick-check, 9 din valve maintenance – Flowserve Valtek Mark 200 User Manual
Page 12
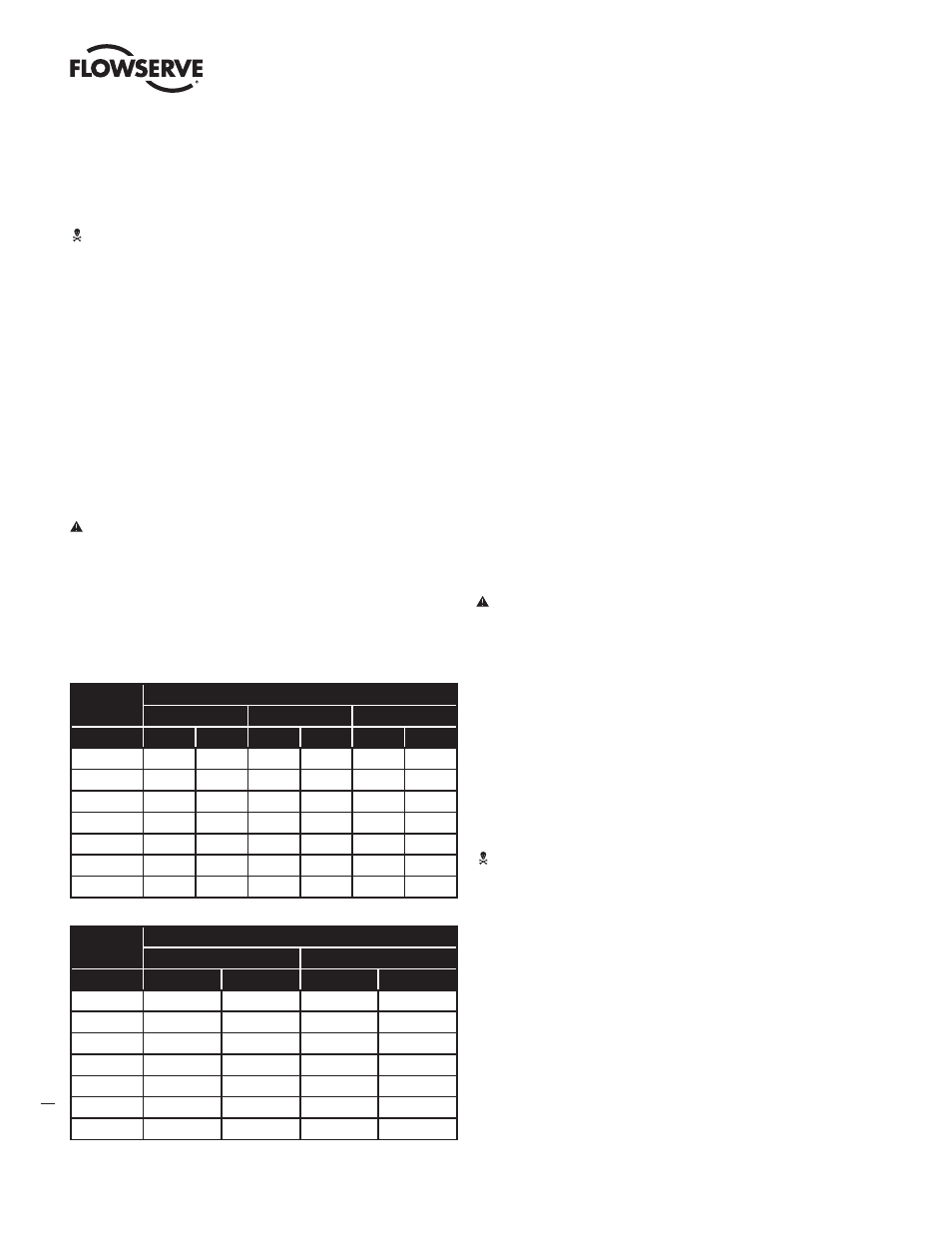
Mark 200 Control Valve FCD VLENIM0200– 12/12
12
8.1 DIN Valve Quick-check
Prior to start-up, check the control valve by following these steps:
WARNING: Due to the risk of injury, it is prohibited to work
between the yoke/columns while the valve is in operation.
1. Stroke the valve and observe the plug position indicator on the stem
clamp compared to the stroke indicator plate. The plug should change
position in a smooth, linear fashion.
NOTE: Due to excessive friction, graphite packing can cause the plug
stem to move in a jerky fashion.
2. Check for full stroke by making appropriate instrument signal change.
3. Check packing box bolting for the correct adjustment. Refer to the
packing installation manual for specific details on maintaining the style
of packing supplied.
CAUTION: Do not overtighten packing. This can cause
excessive packing wear and high stem friction that may
impede plug movement.
4. After a temperature excursion has occurred, bonnet flange bolting
should be retorqued to ensure bonnet gaskets do not leak. See Table 4.
Table 4: Recommended DIN Body Bolt Torque Values
Bolt Size
PN 160 / Body Material
1.0619, 1.5419
1.7357
1.7379
(mm)
ft lb
N m
ft lb
N m
ft lb
N m
M24
265
360
265
360
300
405
M27
385
525
385
525
410
555
M30
410
555
415
565
480
650
M33
630
860
650
885
740
1000
M39
1220
1650
1220
1650
1250
1700
M42
1400
1900
1400
1900
1550
2100
M52
3250
4400
3250
4400
3250
4400
Bolt Size
PN 250 / Body Material
1.0619, 1.5419, 1.7357
1.7379
(mm)
ft lb
N m
ft lb
N m
M24
265
360
280 (300)*
380 (410)*
M30
427
580
500
680
M39
1150
1570
1220
1660
M45
2060
2800
2060
2800
M48
2500
3400
2500
3400
M56
4050
5500
4050
5500
M72
8550
11600
8550
11600
* Nominal Size DN 80 only
9 DIN Valve Maintenance
At least once every six months, check for proper operation by following
the preventative maintenance steps outlined below. These steps can be
performed while the valve is in-line and, in some cases, without interrupting
service. If an internal problem is suspected, refer to the “Valve Disassembly
and Reassembly” section. If multiple checks in line without claim (record) it
is allowed to extend the maintenance interval by risk of plant operator.
1. Look for signs of gasket leakage through the end flanges and bonnet.
Retorque flange and bonnet bolting (if required). See Table 4.
2. Check for fluid leakage to the atmosphere through the body drain plug, if
applicable.
3. Examine the valve for damage caused by corrosive fumes or process
drippings.
4. Clean valve and repaint areas of severe oxidation.
5. Check packing box bolting for proper tightness. Refer to the packing
installation manual for specific details on maintaining the style of
packing supplied.
CAUTION: Do not overtighten packing. This can cause exces-
sive packing wear and high stem friction that may impede
stem movement.
6. If the valve is supplied with a lubricator fitting, check lubricant supply
and add lubricant if necessary. See product documentation or contact
the Flowserve representative.
7. If possible, stroke the valve and check for smooth, full-stroke operation.
Unsteady stem movement could indicate an internal valve problem.
NOTE: Due to excessive friction, graphite packing can cause the plug
stem to move in a jerky fashion.
WARNING: Keep hands, hair and clothing away from all moving
parts when operating the valve. Failure to do so can cause
serious injury.
8. Make sure positioner linkage and stem clamp or coupling pieces are
securely fastened. If the stem clamp or coupling pieces are loose, check
plug thread engagement (refer to the “Reassembling the Body” section
for the correct procedure on aligning the plug with the seat.) Tighten
stem clamp nut or counter nut.
9. Ensure all accessories, brackets and bolting are securely fastened.
10. Clean any dirt and other foreign material from the plug stem.