Vogt valves – Flowserve Vogt Forged Steel Gate User Manual
Page 20
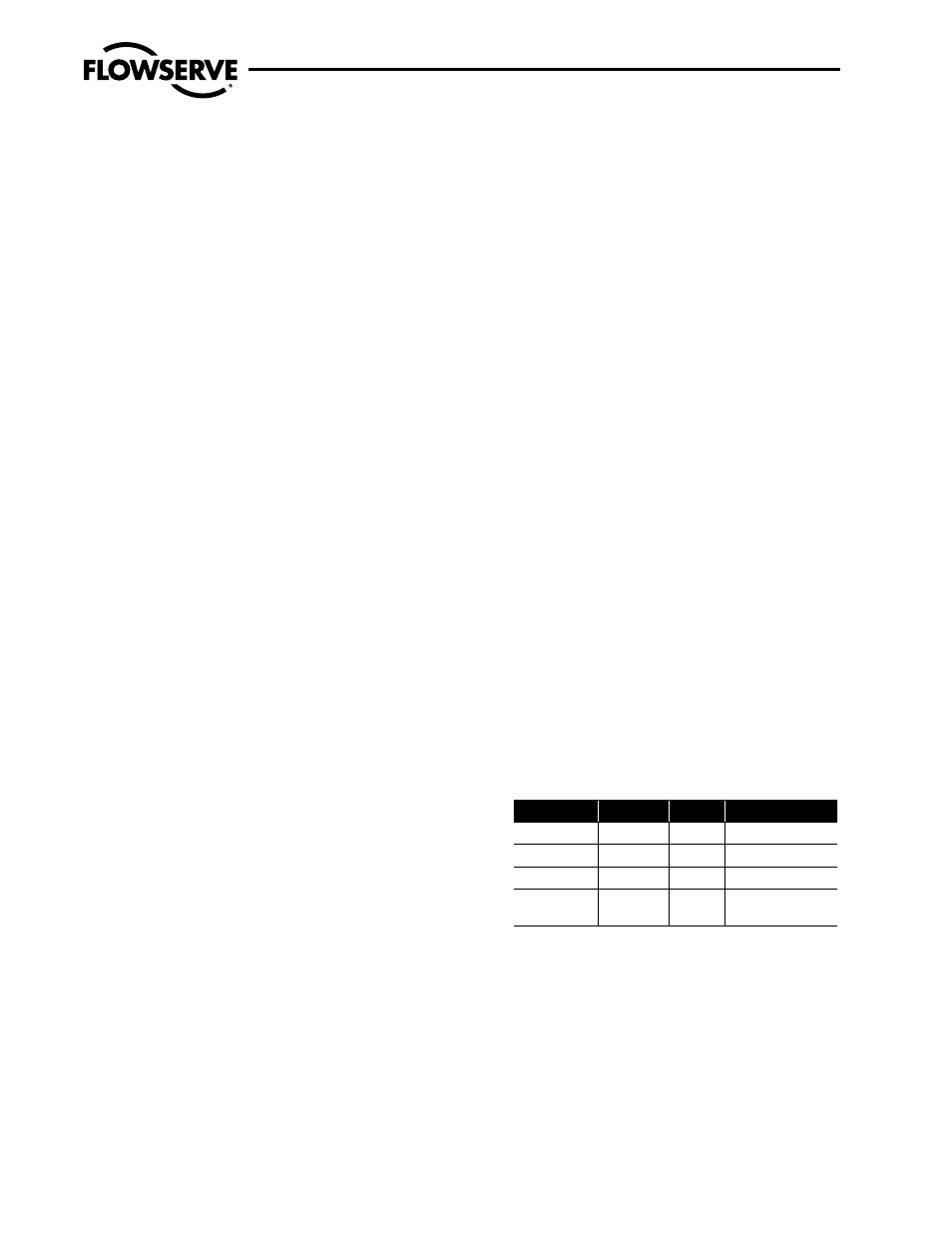
Flow Control
Vogt Valves
20
Forged Steel Gate, Globe and Check Valves
FCD VVENIM2000-02
h) Securely tack weld the mating parts when required if part of the
approved procedure.
i) Complete the weld using the approved welding procedure.
j) Clean and inspect the finished weld.
k) Repair any defects using an approved weld repair procedure
when necessary.
a
CAUTION: For welding end zero leak check valves,
the valve’s piston, or check disk along with the o-ring
should be removed, by removing the valve cover, prior
to welding the check valve into the pipe line. A spare
cover gasket should be ordered to accommodate this
process. Care should be taken to prevent foreign debris
from entering the valve during the installation process.
Cover bolting should be tightened to the torques listed
on page 49 of this document.
4.7 Recommendations for Field
Welding of Small Carbon
Steel Socket Weld Valves
1. Evaluation of Code Requirements Prior to welding,
construction code requirements should be reviewed (ASME
Section I, VIII, IX, B31.1, B31.3, etc.). Applicable code
requirements may supersede these recommendations. In the
absence of specific code requirements, the guidelines of ASME
Section IX are recommended for qualification.
2. Selection of Process Based on the size of the valve and
the skill of the welder, either the SMAW (stick) or GTAW (Tig)
process is recommended. SMAW is generally preferred,
although, GTAW offers more control (at the expense of speed)
and may be preferred for 3/4" and smaller valves.
3. Selection of Weld Filler Metal For SMAW, use
3
/
32
" electrode
on the first pass with
1
/
8
" for subsequent passes.
1
/
8
" and
5
/
32
"
electrodes may be used effectively on larger valves. E7018
electrodes are recommended, although E6010 may be preferred,
particularly on the first pass, if joint cleanliness is less than
desirable.
Type ER7OS-2 is preferred for GTAW. ER7OS-3 and ER7OS-6
may also be used.
3
/
32
" size is recommended, although
1
/
16
" and
1
/
8
" may also be used successfully.
4. Selecting the Welder Most construction codes require a
welder to qualify prior to making a production weld. Welder
performance qualification provides some assurance that the
production weld will be of good quality since the welder has
proven, through testing, that he can make a good weld. Care
should be taken in comparing the welder’s qualification with the
code requirements to assure that the welder has qualified with
an appropriate test for the intended production weld.
5. Joint Cleanliness The area in-way-of welding should be
cleaned to remove rust, scale, dirt, oil, and protective coatings.
This should be done prior to fit-up or residue in the joint overlap
will not be removed. Sanding, grinding, or wire brushing is usu-
ally adequate. Solvents may be necessary, if oil is to be removed.
6. Fit-up (Socket Weld Valves) In order to gauge fillet weld size
after welding place a circumferential mark 1" from the engaging
pipe end prior to welding. Bottom out the pipe engagement into
the socket and pull it back approximately
1
/
16
" to allow for weld
shrinkage. Note the dimension from the mark to the valve pipe
end.
Tack welds should be contoured to allow for easy inclusion into
the final weld.
7. Welding Technique
a. Prior to welding, the valve should be lightly closed. Where
possible, attach the electrical ground to the adjoining pipe
on the same side of the valve as the weld being made. Do
not attach the ground to the handwheel or upper structure of
the valve or arcing across the valve seating surfaces could
occur.
b. Where possible, welding should be done in the flat or
horizontal position. Where vertical welding is necessary,
progression should be upward (vertical down welding is
prone to lack-of-fusion).
c. Welding parameters: The following welding parameters may
be used as a guide.
Electrode
Current
Voltage Shielding Gas
3
/
32
"
E6010
55-75 A
—
N/A
3
/
32
"
E7018
70-90 A
*
N/A
1
/
8
"
E7018
90-110 A
*
N/A
3
/
32
"
ER7OS-2
75-100 A
13-14 V 100% Argon at
15-20 CFH
*Use as close and tight an arc as possible.
d. A minimum of two layers should be used for all socket
welds. This will decrease the chance of leaking even if one
pass contains a weld defect.