Flowserve SLD User Manual
Page 4
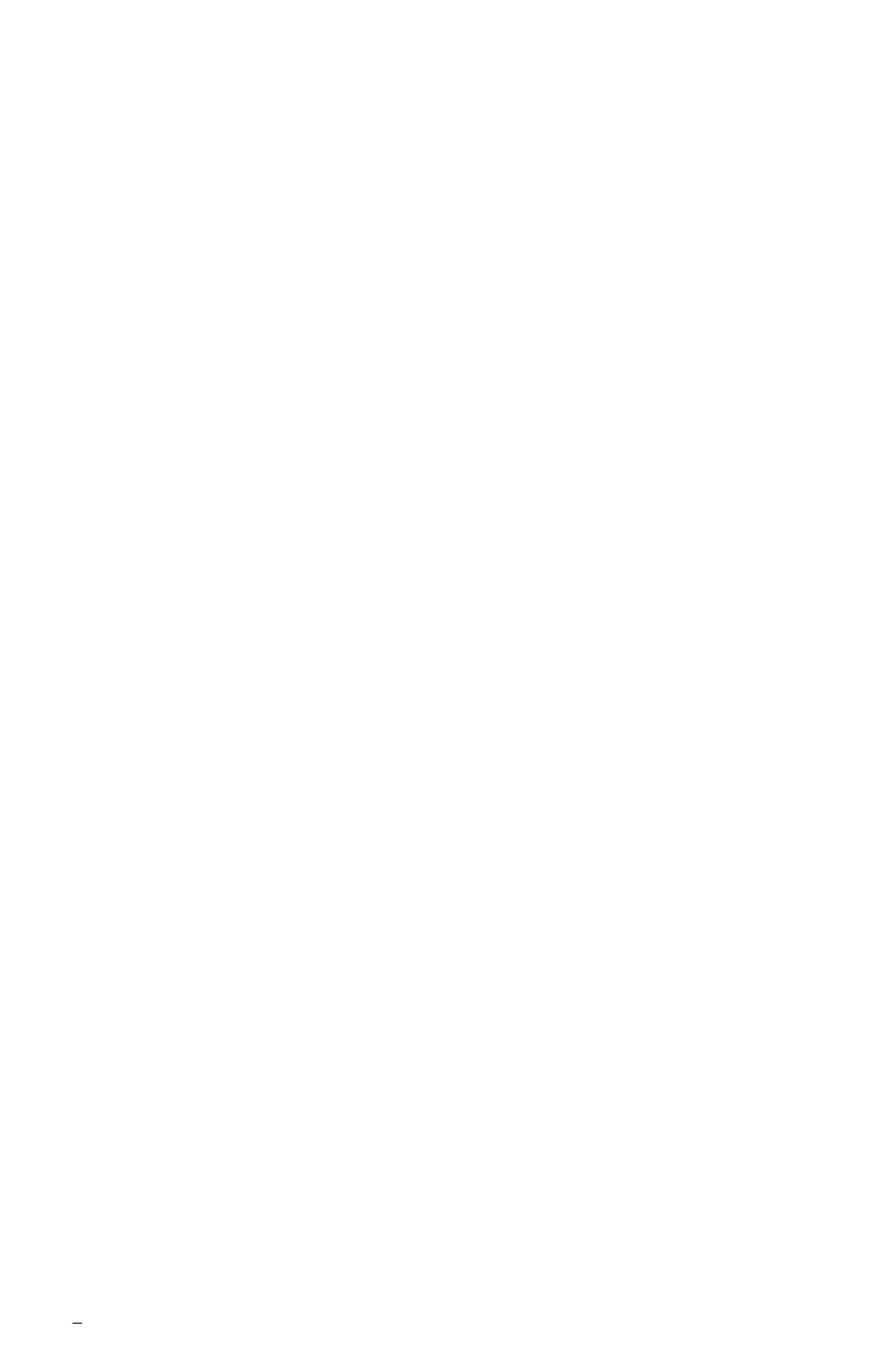
4
It is recommended that the shortest possible pipe length be used. The
piping should be installed with good design and minimal bends from the
SLD to the seal. It should be filled with clean grease prior to start up and
vented to make sure no air has been trapped prior to start up.
Additional support to the SLD auto-luber may be required for pipe lengths
over 100mm (4 inch). High vibration levels or improper support of the SLD
auto-luber unit can cause threaded fitting fracture or failure. The unit should
be monitored carefully to ensure that it does not experience excessive
vibration caused by pump operation. If vibration is observed due to inad-
equate support from the piping alone, additional bracing should be used to
support the unit. The bracing should connect directly to the fitting near the
SLD auto-luber, not directly to the unit.
The SLD auto-luber should be located so that it will not be impacted during
normal pump operation and maintenance. Excessive or sudden force on
the threaded fittings may lead to a fracture or failure.
Take care using tube fittings or special connectors as they may have an ID
smaller than the 6.4 mm (.25 inch) recommended. Restrictions in the INLET
or OUTLET lines may create back pressure in the system affecting perfor-
mance of the SLD auto-luber.
1.3 Temporarily plug the pipe tee with a pipe plug prior to initially filling the seal
quench cavity by use of the SLD grease gun.
1.4 Fill the seal quench cavity with SLD synthetic lubricant supplied using
the specified grease gun until lubricant expels from the OUTLET quench
connection located towards the top of the seal. This step does not need to
be repeated later when only replacing an empty SLD auto-luber unit.
1.5 Install OUTLET piping using 1/4 inch NPT [6.4 mm (0.25 inch) minimum
pipe ID]
to the OUTLET quench connection of the seal. Piping should have
no restrictions and be a maximum length of 125 mm (5 inch). The piping
should expel the lubricant to a safe location. For dusting or blowing sand
environments, a 90 degree elbow can be connected with the opened end
facing down.
1.6 Remove the pipe plug from the pipe tee and thread the SLD auto-luber unit
in place to finish installation.
1.7 Set the dispensing rate of the SLD auto-luber unit by clicking the
appropriate DIP (direction input postioner) switch or switches located
through the top access port. See Figure 2. It is recommended that the
initial dispensing rate should be between 1-2cc per day (2-3 month setting
for Mini Luber or 8-12 month setting for Jumbo Luber) to start with. Be
sure to also click on the “Blip” light switch. See paragraph 4 Maintenance
for blip light indicators. The visual presence of the blip light every 15 to
20 seconds indicates that the SLD system is functioning and operational.
Be sure to replace the DIP switch access cap and weather proof cover to
protect the SLD auto-luber unit against dust and moisture contamination.
Lubricant dispensing rate may vary depending on atmospheric pressures,
temperatures, and seal size. Please see Section 3 for appropriate
considerations.