7 faults; causes and remedies, Drawings (8), General assembly drawings (8) – Flowserve PolyChem GRP User Manual
Page 45: Parts lists (see 8), Sectional drawings (8)
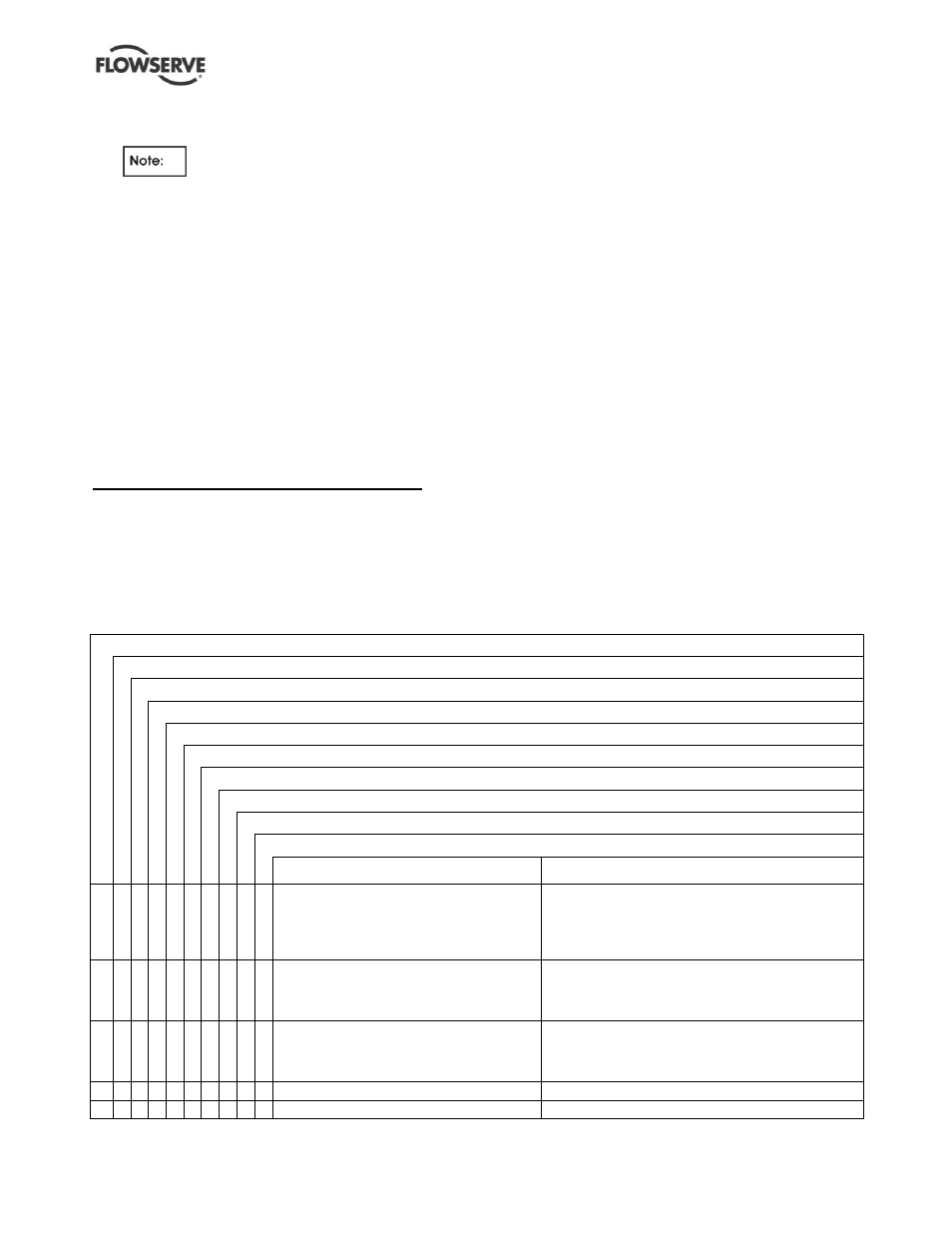
USER INSTRUCTIONS POLYCHEM GRP ENGLISH 71569132 12-04A
Page 45 of 52
flowserve.com
d) For packing, install 4 packing rings [4130], then the
seal cage [4134] and then 2 more rings of packing.
Pump size 4J12x10G-15B only has 5
rings of packing followed by the seal cage and
then 2 more rings of packing.)
6.10.5 Final back pullout assembly steps
a) Refit the constant level oiler, if supplied.
b) Fit the main casing O-ring [4610.1] onto the cover
[1200].
c) The complete back pullout assembly can now be
installed into the casing. Fit the casing bolts
[6570.1] or use the studs [6572] (on some
pumps) together with washers [6541.4],
lockwashers [6541.2] and nuts [6580.3] and
torque up evenly to 14 Nm (10 lbf
•ft).
d) Finally, adjust the impeller running clearance as
described in section 6.6.
7 FAULTS; CAUSES AND REMEDIES
Troubleshooting
The following is a guide to troubleshooting problems with Flowserve Mark 3 pumps. Common problems are
analyzed and solutions offered. Obviously, it is impossible to cover every possible scenario. If a problem
exists that is not covered by one of the examples then refer to one of the books listed in section 10.3, Sources
of additional information, or contact a Flowserve Sales Engineer or Distributor/Representative for assistance.
Fault symptom
Pump not reaching design flow rate
Pump not reaching design head (TDH)
No discharge or flow with pump running
Pump operates for short period, then loses prime
Excessive noise from wet end
Excessive noise from power end
PROBABLE CAUSES
POSSIBLE REMEDIES
Insufficient NPSH. (Noise may not be
present.)
Recalculate NPSH available. It must be greater than the
NPSH required by pump at desired flow. If not, redesign
suction piping, holding number of elbows and number of
planes to a minimum to avoid adverse flow rotation as it
approaches the impeller.
System head greater than anticipated.
Reduce system head by increasing pipe size and/or
reducing number of fittings. Increase impeller diameter.
(NOTE: Increasing impeller diameter may require use of
a larger motor.)
Entrained air. Air leak from atmosphere on
suction side.
1. Check suction line gaskets and threads for tightness.
2. If vortex formation is observed in suction tank, install
vortex breaker.
3. Check for minimum submergence.
Entrained gas from process.
Process generated gases may require larger pumps.
Speed too low.
Check motor speed against design speed.