Description of operation – Crompton Controls 3DPM1CHS/10 User Manual
Page 6
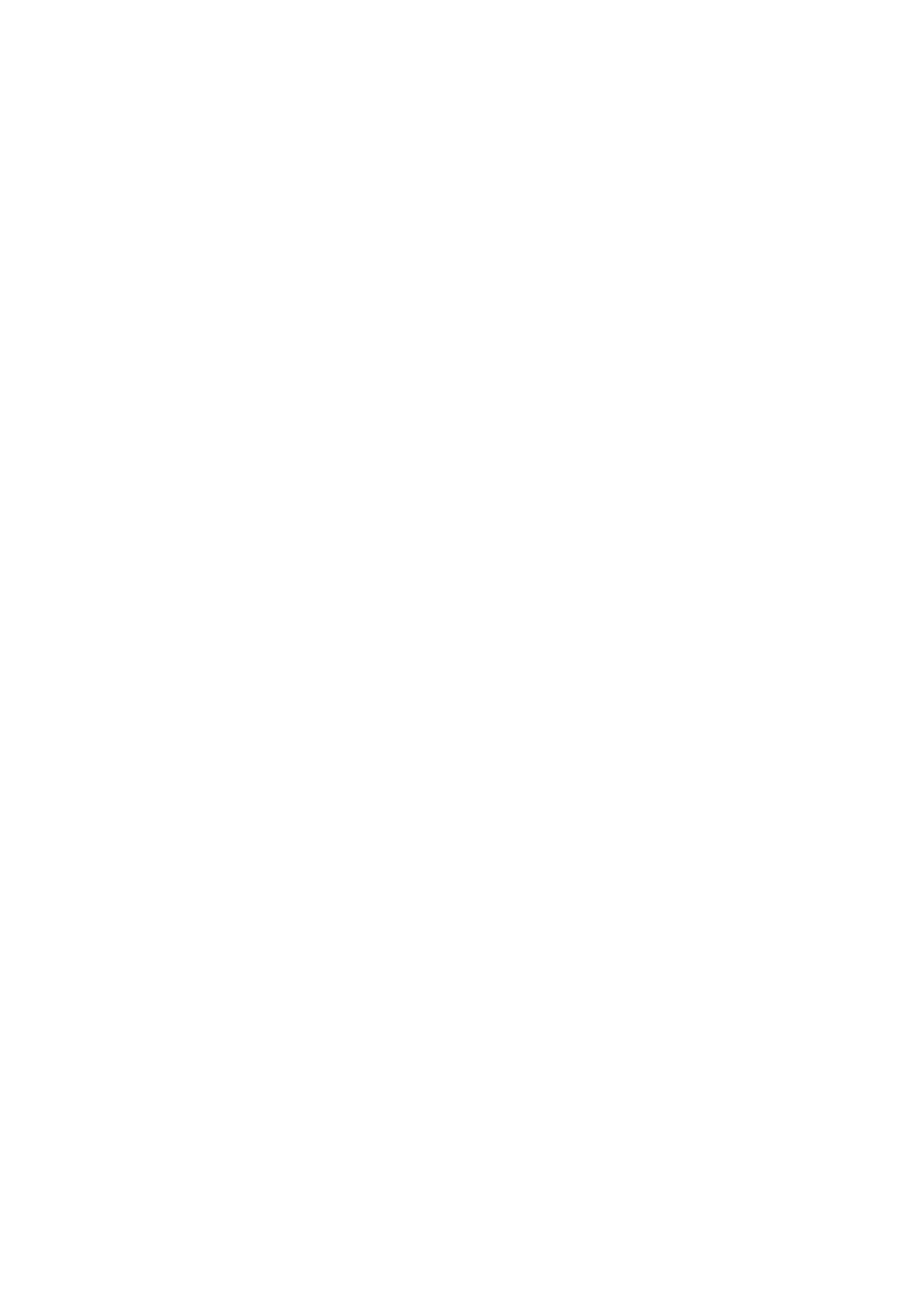
6
Description of operation
Both S10 and Smooth-BRAKE units are powered at operational voltage on
L1
and
L2. L1
is connected internally to the PCB OV common. A secure connection to the incoming supply
must be made at all termination and switching points. The voltage sensing input to B2 is
measured relative to L1. At power on there is a short initial delay and RL1, one of the two
internal relays, is energized giving an output on terminal 18, provided terminal 17 has a
supply. This output is wired to the main start contactor which can be energized to start
the motor; an auxiliary terminal on this contactor is used to connect a voltage to the
B2
sensing input. When voltage is applied to B2 nothing happens, until on removal of this
voltage when the timing sequence starts:-
1
25mS dwell, then re-check no voltage on B2 – to prevent the startup voltage drop
causing dc injection
2
RL1 opens removing the feed to 18 preventing the main contactor from operating
3
500mS dwell period to allow the contactor arcs and motor EMF to decay – the setting
potentiometers are also read at this time.
4
RL2 is then energized to bring in the external brake contactor, connecting terminals
M1 and M2 directly to the motor.
5
This enables DC to be injected for the time and voltage as set on the potentiometers.
(Smooth brake without M3 connected).
The DC is increased progressively to the set value to avoid mechanical shock.
6
RL2 is then de-energized after turning off the DC
7
Dwell period to allow the DC to decay
8
RL1 is then re-energized to allow the motor to be started again.
NOTE:
DC injection braking is a PUWER 98 approved method of stopping AC electric
motors and requires the mains supply to be present to operate correctly.
S10 and Smooth-BRAKE (without M3 connection)
Basic setting procedure
A Braking Time Setting (0-100% S10 0.1- 12.7 sec Smooth Brake 0.2 to 50 sec)
1. From minimum, turn the Braking Time Pot slightly clockwise.
2. Start the motor.
3. Stop the motor and check the time the brake contactor energises for.
4. Repeat steps 1 – 3 until the required time is reached (10 seconds or less).
B Braking Torque Setting (0-100% - approx 160v dc)
1. From minimum, turn the Braking Torque Pot slightly clockwise.
2. Start the motor.
3. Stop the motor and measure the time taken to stop.
4. If the motor continues to rotate after the Braking Time (contactor) has lapsed repeat
steps 1 – 3 until there is sufficient braking to stop the motor within the required time.