Interlocks – Crompton Controls 3DPM1CHS/10 User Manual
Page 15
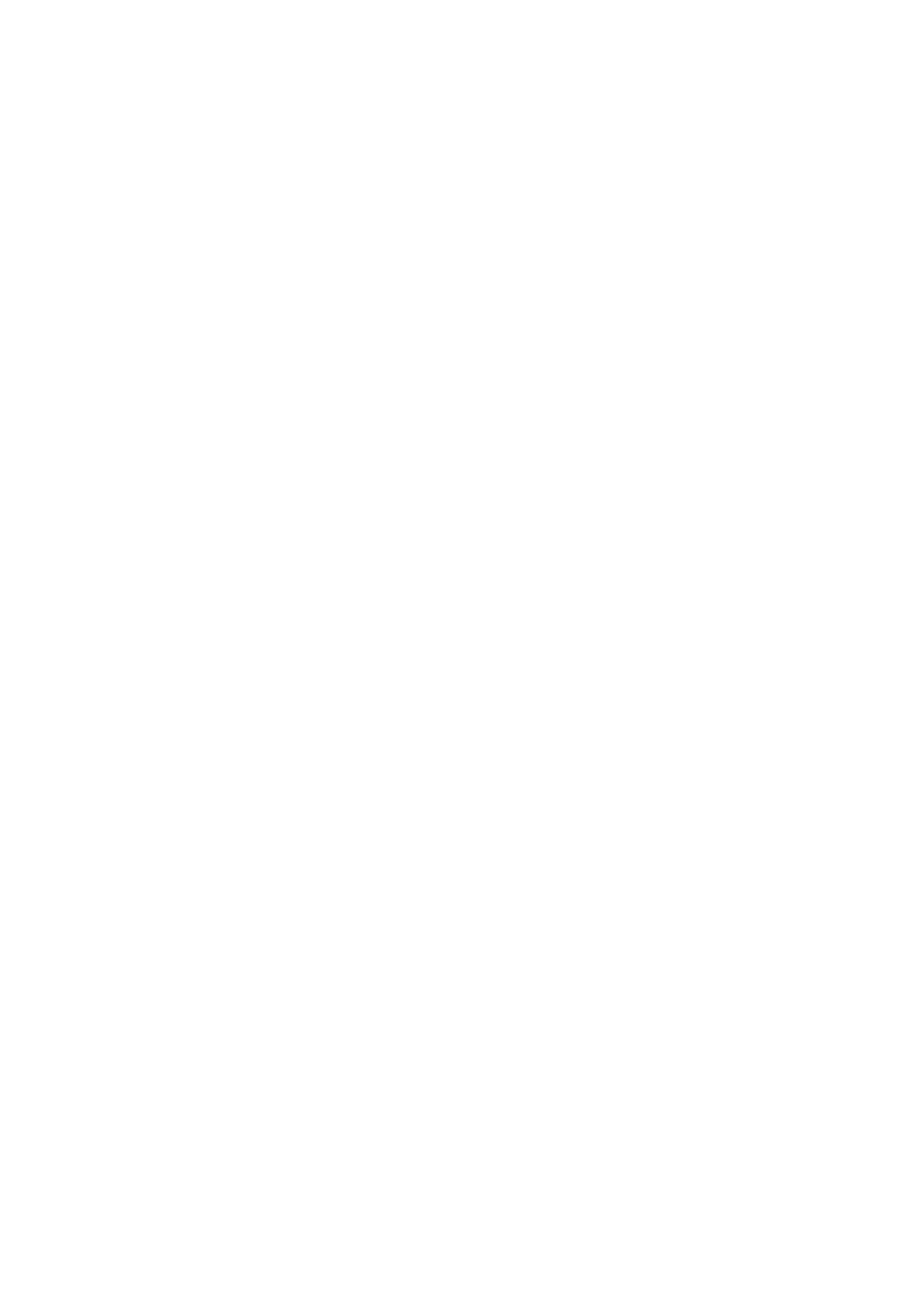
15
Interlocks
The two internal relays controlling the starting (RL1) and braking (RL2) provide in initial
degree of interlocking. The normally closed on the first relay feeds the common on the
second so the outputs 18 and 28 cannot be on at the same time. Electrical interlocks are
also used on the main and DC contactors. However if the interlocking is bypassed for
some reason then the AC and DC contactors energised together put a direct short circuit
across two phases and supply fuse size will determine the amount of damage.
If several brake modules are used with a common control circuit it is important to
maintain interlocks across all the units. Use volt free relay contacts in the common circuit
from relays connected to terminal 18 on each module.
General Notes
•
Star Delta run up times of approx 15 sec or more could result in the overload tripping.
•
Star Delta connections are important easy to have the motor start and run but not dc
inject if the 6 leads are not correctly marked or wired.
•
Inertia can result in the need to increase the amount of dc current. E.g. Disc sanders,
band saws, and high-speed routers.
•
Mechanical damage can occur with very high levels of dc injection.
•
The motor resistance will change with temp up to 30% from cold to hot, reducing
braking as the motor warms.
•
Bad connections can cause severe damage to contactors –old machines have old
motors, wiring and starters. Sawdust and woodchips inside contacts is a prime cause of
bad connections.
•
More than one motor can be dc injected using the same thyristor/diode power assembly
if all can be stopped together.
•
Multi motor machines (tennoners) can have individual start buttons but one common
stop which will dc inject all motors running or stationary.
•
Aux block on the main contactor has to be moved to allow the starter to be wired. If
not put back in place this may result in no braking i.e. the brake contactor doesn’t
operate.
•
Check connections to the motor if the brake contactor is operating but the motor is not
braking.
This can be quickly done by measuring the winding resistance across the diode M1 to
M2 while operating the brake contactor by hand to make the circuit.