Crompton Controls 3DPM1CHS/10 User Manual
Page 2
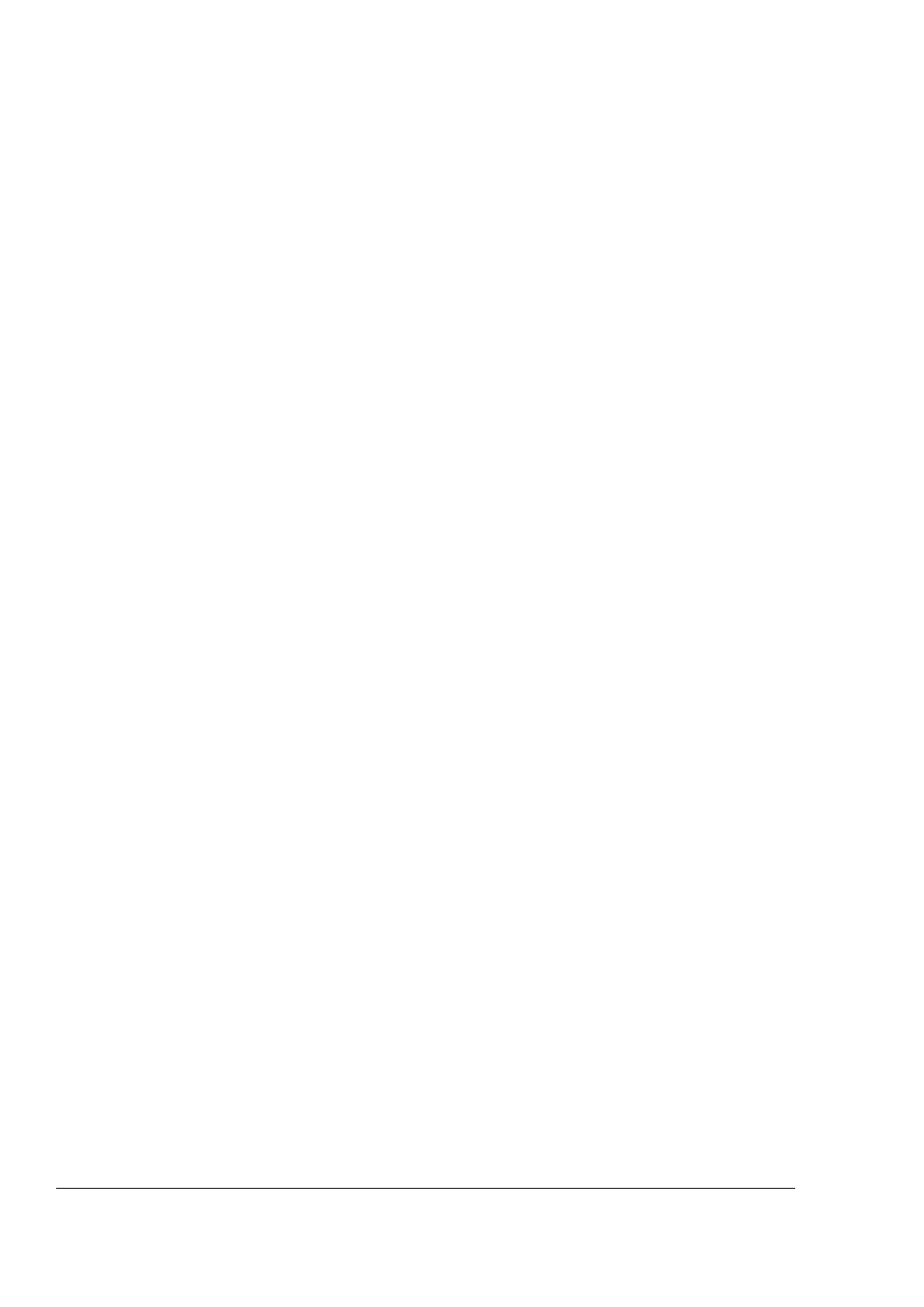
DC Injection Brake Module
Installation and Maintenance Document
S10 and Smooth-BRAKE
Warranty
All goods are guaranteed for one year from the date of purchase. This does not affect the
statutory rights of the user.
Safety warning
Important Safety Information
All electrical equipment for operating on low voltages contain devices which are capable of
causing serious or fatal injuries.
Any person involved in installation or maintenance of this equipment should be fully
competent to conduct the work.
Such persons should be familiar with the Health and Safety at Work Act, Electricity at
Work Regulations and have a working knowledge of the IEE Wiring Regulations.
If in doubt please contact,
Crompton Controls Ltd Tel: +44 (0)1924 368 251
General Description of the equipment
Crompton Controls DC injection Braking starters are suitable for controlled
stopping of induction motors.
When the machine starter is de energised the brake timer senses the break in supply and
applies a DC voltage to the motor windings to provide a controlled braking force for a
timed duration.
NOTE:
DC injection braking is a PUWER 98 approved method of stopping AC electric
motors and requires the mains supply to be present to operate correctly.
Induction motors
Induction motors can be braked to standstill, by injecting a DC current into the winding,
this creates a stationary field and any shaft rotation will produce a braking torque.
Braking from full speed an induction motor behaves as a twice speed generator, the
generated currents help to stop the motor and full load braking torque requires a DC
current of approx 2 to 2.5 times motor full load current. The DC is produced using a
thyristor with controlled half rectification and a diode is connected across the motor to
rectify the generated current, without the diode the motor would not brake. The externally
applied dc current will rise as the machine brakes to a halt. Motor noise is normal when
using phase angle control due to the nature of the unsmoothed dc waveform.
The DC current produces magnetic flux in the motor air gap, current can increase but
there is a saturation effect that means flux and braking torque will increase with current
up to saturation after which high currents will not produce much extra braking.
Most braking systems provide a voltage to apply to the windings, at standstill the current
will be determined by ohms law, current=voltage/winding resistance.
Part Numbers
Rated operational voltages
BR011 S10/400
400 volt 50Hz 25 Amp brake module
BR016 S10/240
240 volt 50Hz 25 Amp brake module
BR021 S10/110
110 volt 50Hz 25 Amp brake module
BR025 Smooth-Brake
400 volt 50Hz 60 Amp brake assembly
BR026 Smooth-Brake
400 volt 50Hz 90 Amp brake assembly
BR024 Smooth-Brake Control Module
2