Sioux Tools SNH10S18 NIBBLER User Manual
Page 3
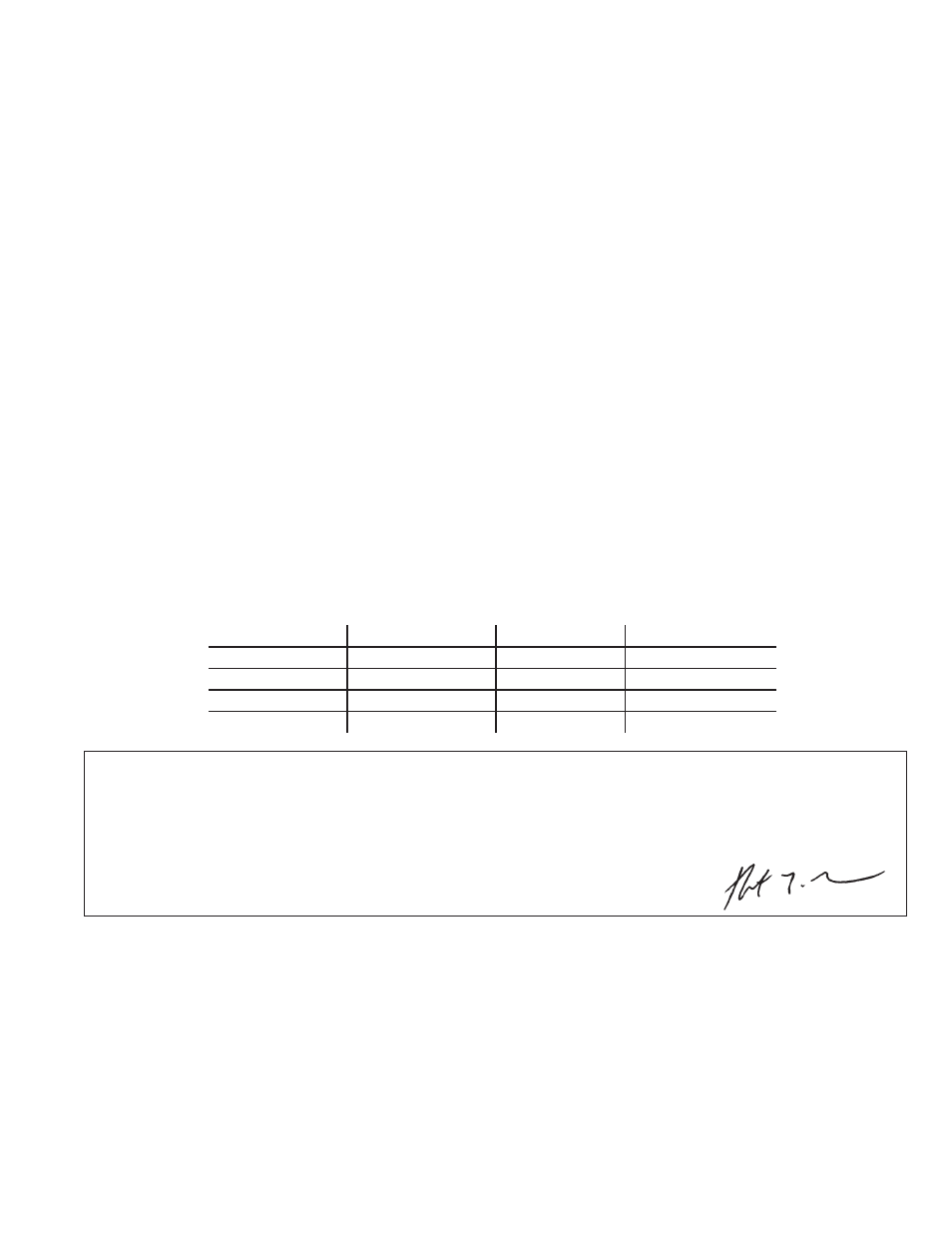
Form ZCE797
3
Date 2012May9/B
ASSEMBLY
To assemble 53609 shear head and adapt to power unit:
1. Place the left side knife 54500 into position in the shear housing.
2. Insert center cap screw 07102 through housing and blade just far enough to slip spacer bushing 54502 over cap screw.
3. Place right side knife 54501 into position and push center cap screw through right side knife. Start cap screw into insert just enough to hold
blades in place. DO NOT TIGHTEN.
4. Insert spacer bushing 54502 into hole in center blade 54499 and lubricate with a good grade of bearing grease.
5. Install center blade 54499 into shear housing 12598 by tapping blade gently forward using a drift to line up hole in center blade with forward holes
in housing.
6. Insert and tighten forward cap screw 07102 making sure spacer bushing 54502 in center blade stays in position. Apply good grade of bearing
grease to clevis in center blade. WHEN SHEAR HEAD IS PROPERLY ASSEMBLED THE CENTER BLADE WILL PIVOT FREELY IN HEAD.
7. Insert rear cap screw 07102 into shear housing 12598 but do not completely tighten.
To install shear head assembly 53609 onto power unit:
1. Make sure rear cap screw and center cap screw 07102 are loosened three complete turns.
2. Place shear head onto unit and tighten cap screws 07102 snugly to lock head assembly in place. It may be necessary to gently tap the shear
head assembly into place if it does not readily slip onto the power unit.
NIBBLER HEAD
The Nibbler Head is recommended for CR sheet steel up to 18 gauge. Secure work piece. To start cut, place die opening of nibbler slightly onto the
edge of the work piece to steady the tool and ready it for the cut. Depress the trigger switch on the drive motor and guide the nibbler into the work.
Don’t force it. Avoid double thickness of material, which exceed the 18 gauge recommended capacity. For cutting within perimeter of work piece, drill
a 1/2" diameter-starting hole and follow instructions above. If resistance to tool develops or cutting becomes difficult, discontinue cutting and check the
following: lubrication; chip clogging; thickness of material, sharpness of punch and die.
ADJUSTMENTS
The die rotates a full 360 degrees. To change position, loosen clamp nut and set die in desired position, tighten clamp nut. When cutting corrugated
metal, set die at 90 degrees to the motor unit. This will allow the motor and head to roll with the corrugations.
TO CHANGE PUNCH AND/OR DIE
1. Disconnect motor unit from power source.
2. Remove clamp nut 64089 and the die 64091 will slide off.
3. Remove retainer nut 64092 and the punch 64090 will slide out of the head.
4. Insert new punch into head and secure with retainer nut.
5. Insert new die and secure with clamp nut.
MAINTENANCE
Once every three months, depending upon usage, remove the nibbler head from the power unit by loosening clamping screw and pull the head with a
twisting action. Lubricate bearing surface of the eccentric nut with a good grade of bearing grease. Place nibbler head back onto motor unit. Eccentric
nut must engage with the link assembly as head is placed onto motor. Tighten clamping screw snugly to lock head assembly in place.
DECLARATION OF CONFORMITY
We, Sioux Tools Inc., 250 Snap-on Drive, P.O. Box 1596, Murphy, NC, 28906, USA, declare under our sole responsibility that the products
SSH10P18, SSH10S18, & SNH10S18
to which this declaration relates are in conformity with the following standard or standards or other normative document or documents:
EN 792, ISO 12100-1, ISO 12100-2, ISO 8662, ISO 3744
following the provisions of
89/392/EEC as amended by 91/368/EEC & 93/44/EC Directives.
Signature of issuer
June 1, 2009
Murphy, North Carolina, USA
Date and place of issues
Robert Hartman
Vice President and General Manager-Power Tools
Sioux Tools Inc
Name and position of issuer
NOISE AND VIBRATION READINGS
Catalog Number
*Sound Pressure (dBA)
*Sound Power (dBA)
*Vibration m/s^2
SSH10S18
79.4
91.0
3.12
SSH10P18
85.1
96.7
Less than 2.5
SNH10S18
82.4
94.0
6.75
*per ISO 3744
*per ISO 3744
*per ISO 8662