Internal cooling loop, Liners, Spare parts kit – Parr Instrument Series 4580 User Manual
Page 18: Air motor, Accessories (continued)
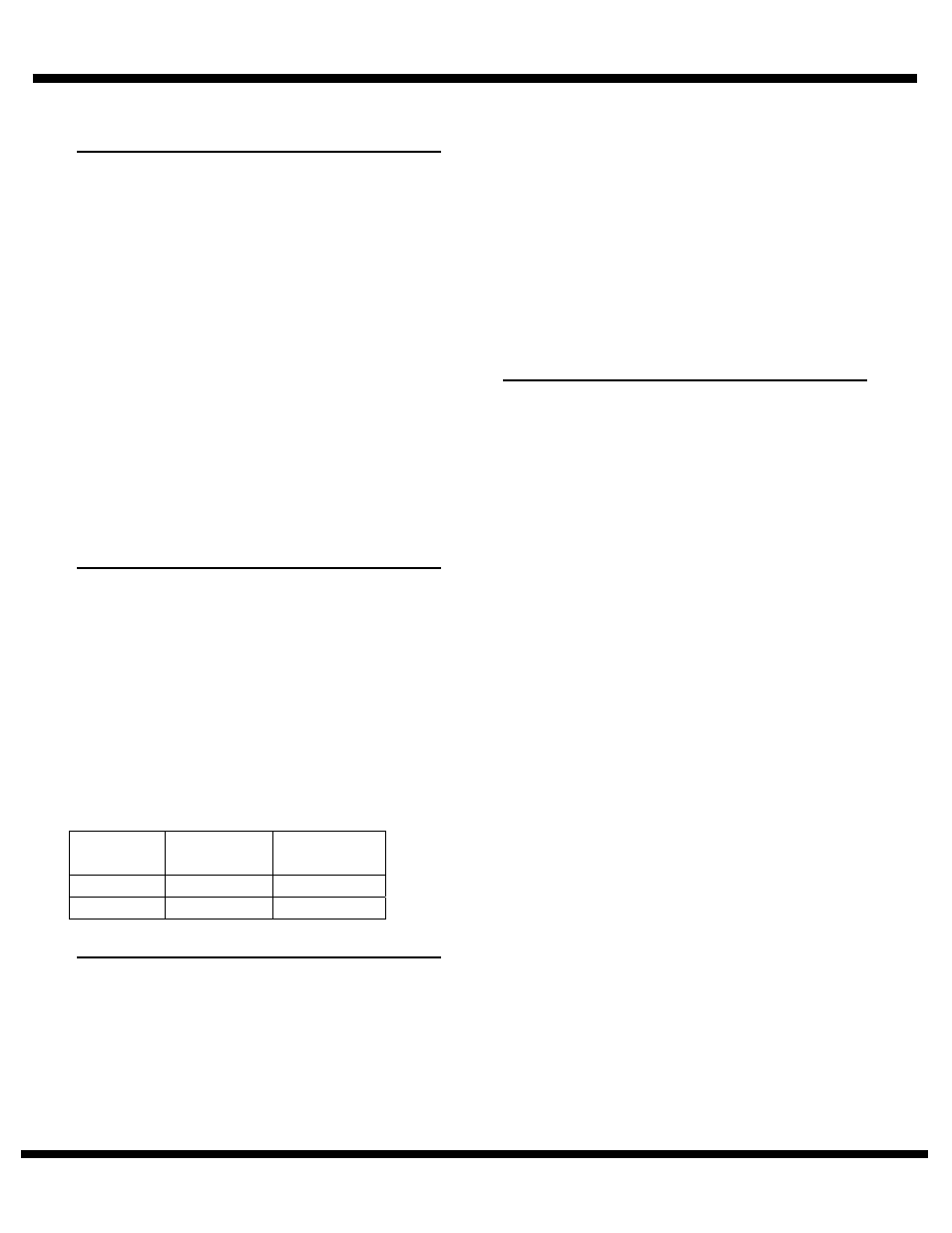
- 17 -
ACCESSORIES (continued)
Internal Cooling Loop
A serpentine cooling coil is mounted to the
underside of the head and sealed with a ferrule
and compression nut arrangement.
A slow continuous flow of cold water
through the coil is an effective means for
controlling temperature overshoot, particularly
when operating at temperatures below 150
C.
Alternately the cooling coil is used to effectively
cool the system at the completion of a reaction.
An optional solenoid valve package is
available to automate the cooling process.
This package coordinates with the internal coil,
with the water supply and connects to the
temperature controller.
If the internal cooling is not required, the
coil may be removed and the alternate plugs
installed.
Liners
Glass liners are available for both 1
gallon and 1.5 gallon vessels. These liners
slide into the cylinder. Although they will not
keep corrosive vapors from reaching the
surfaces of the cylinder and head, they
make it much easier to add and remove
liquid reactants, and they give some
protection to the cylinder when working with
corrosive solutions.
Liner Part Numbers
Fits
ID
Cylinder
Size
Glass
Liner
5.50” 1
Gallon
1996HC
5.50” 1.5
Gallon
1996HC2
Spare Parts Kit
Spare parts kits are available for these
reactors. The kits will provide a reserve
supply of parts and tools sufficient to handle
most normal replacements and emergency
repairs during a year of heavy usage.
The kits contain small perishable items
required for continuous operation including
gaskets, bushings, rupture discs and seals.
They can be ordered from any Parr Dealer
or direct from the Parr Instrument Company.
The order must specify the reactor size and
indicate type of rupture disc, stirrer drive and
type of gasket. It is most advantageous to
provide the complete vessel serial number
from the head or cylinder.
Air Motor
Variable stirring speeds from 100 to 2000
rpm with no electrical spark hazard can be
obtained by replacing the standard motor
with an air motor. This motor operates on
compressed air which must be supplied at
40 psig minimum pressure with at least
10CFM available at that pressure. It is
furnished with a speed control valve and
oiler, all assembled on a mounting bracket.
To operate reactors equipped with an air
motor, mount the drive system firmly on the
support stand and connect the air hose to a
compressed air line. Fill the oiler with SAE
10 oil and adjust the oiler to feed one drop
per minute into the air stream. For long
continuous runs at high speeds, the oiling
rate should be increased to three drops per
minute. If the motor becomes sluggish,
flush it with a non-flammable solvent in a
well ventilated area. Disconnect the air line
and muffler and pour a small amount of
solvent into the inlet port. Rotate the shaft
by hand in both directions for a few minutes;
then connect the air line and run the motor
until there is not further trace of solvent in
the exhaust. If the muffler felts are dirty,
wash them in solvent or replace them.
Relubricate the motor with a squirt of oil into
the chamber and reassemble. If it becomes
necessary to disassemble the motor to
replace the vanes, follow directions given in
the instruction sheet published by the Gast
Manufacturing Corp., Benton Harbor,
Michigan.