Maintenance and safety instructions, Bomb maintenance, 1108r oxygen combustion vessel – Parr Instrument 1108R User Manual
Page 12
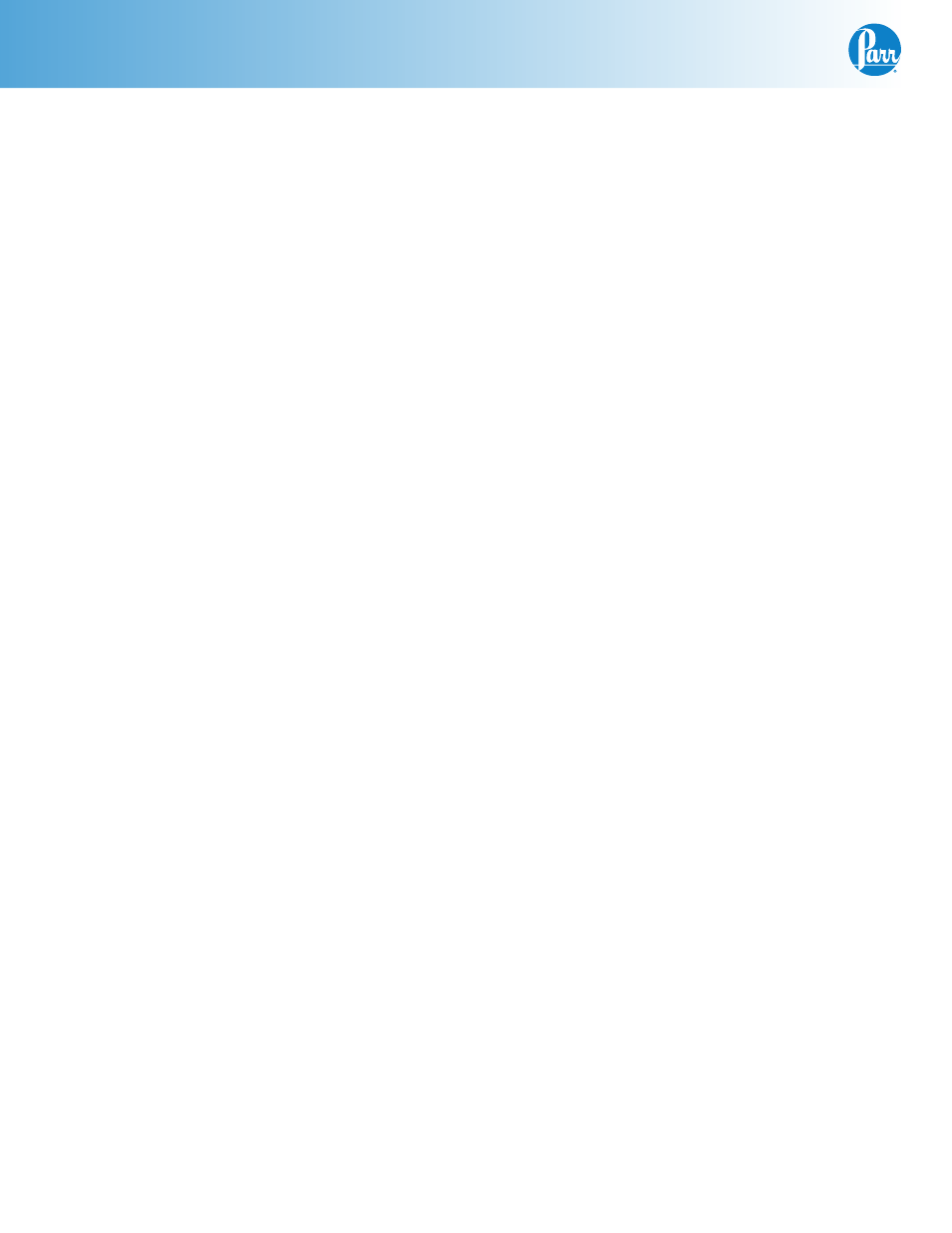
P a r r I n s t r u m e n t C o m p a n y
12
1108R Oxygen Combustion Vessel
Maintenance and Safety Instructions
Bomb Maintenance
Under normal usage Parr oxygen bombs will give
long service if handled with reasonable care. How-
ever, the user must remember that these bombs
are continually subjected to high temperatures and
pressures which apply heavy stresses to the sealing
mechanism. The mechanical condition of the bomb
must therefore be watched carefully and any parts
that show signs of weakness or deterioration should
be replaced before they fail. Otherwise, a serious
accident may occur.
Do not fire the bomb if gas bubbles are observed
anywhere indicating a possible gas leak. Disas-
semble the parts and install new seals immediately.
The bomb head parts which require closest attention
and most frequent replacement are: the 410A quad
ring head gasket, all the 238A sealing rings, the
415A O-ring and the 20VB PCTFE valve seat in the
needle valve.
When replacing the 410A head gasket, remove the
104A2 contact ring and position the new 410A flat
upon the head.
The 20VB valve seat in the needle valve deteriorates
with use, not only in the needle area but on the
underside of the seat as well. Leakage and a possible
serious burn-out can result from a worn or damaged
seat if it is not replaced promptly. As a basic rule,
the 20VB valve seat and the two 238A O-rings on
the valve needle should be replaced after every 500
firings or every six months, whichever occurs first.
If the bomb is used for samples containing chlorine,
these parts should be replaced after every 250 firings.
To replace the valve seat, unscrew the 397A com-
pression nut; remove the valve stem and the old
seat, and disassemble all of the parts. Drop a new
20VB valve seat into the body and push it down
into place. Slide a 7VBCM Monel washer, two 238A
O-rings and the 378A packing cup onto the A420A
valve needle assembly with the needle pointed
upward; then adjust the parts on the needle so
that the tip of the needle is flush with-or slightly
recessed into-the bottom of the packing cup. Insert
this assembly into the 396A outlet valve body and
press it firmly against the valve seat by tightening
the 397A compression nut to 100 inch-pounds of
torque.
A Parr 475A Service Clamp offers a convenient
means for clamping the bomb head firmly in a vise
without damaging the head when replacing any of
the bomb head parts.
Keep the 397A compression nut on the valve needle
tightened firmly at all times. Frequent tightening
is important. This nut, if slightly loose, may allow a
leak to develop during the rapid pressure rise upon
ignition. This type of leak may not be detectable
before firing; but if it develops, the hot gases can
ignite the 20VB valve seat and burn through the
head.
Do not use extreme force when closing the needle
valve. A moderate but firm turn on the valve knob
should be sufficient to stop all gas flow. Excessive
needle pressure will deform and possibly close the
gas passage. If this happens, unscrew the valve
body and replace the 20VB valve seat. Accumulated
salt deposits may also clog the gas passage, making
it difficult to release pressure at the end of a run.
To avoid this, clean the passage through the valve
needle and deflector nut with a small drill.
The 238A sealing ring in the insulated electrode
should be replaced with the same frequency as the
20VB valve seat. Also, keep the 411A terminal nut
tight at all times. As the 238A sealing ring ages and
hardens it becomes a partial electrical conductor,
permitting misfires and producing unwanted heat-
ing effects. Periodic replacement will eliminate this
potential problem.
The threads on the screw cap should be checked
routinely for any burns or other deformity. After
long use, the threads on the screw cap may become
worn to the point where they will no longer provide
a safe closure for the bomb, and the screw cap will
have to be replaced. The following procedure can be
used to check the extent to which the threads have
become worn: