Step 5, Step 6 step 7 – ParkZone PKZ4675 User Manual
Page 4
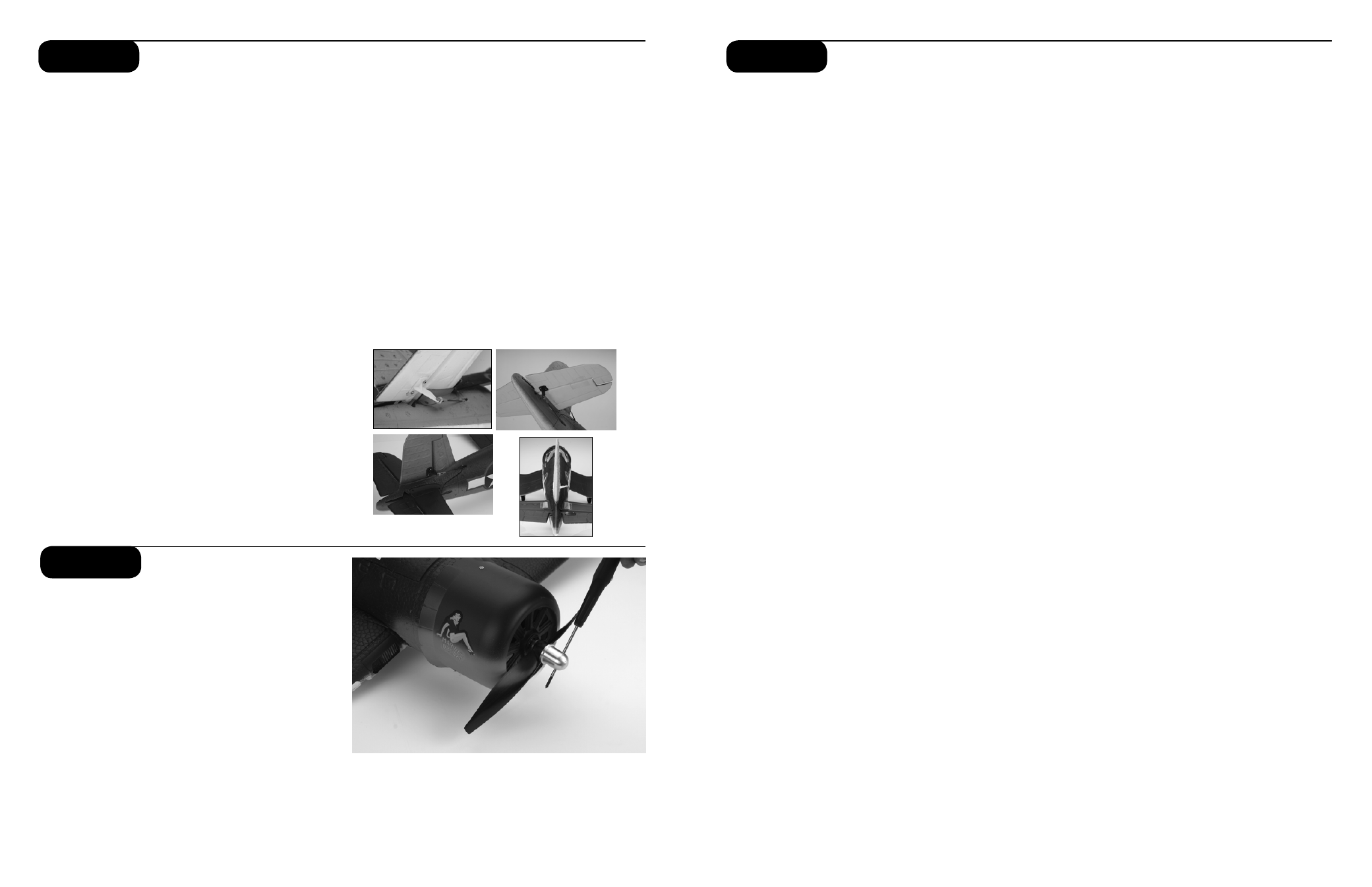
7
8
Attaching the Horizontal Stabilizer
1. Locate the horizontal stabilizer of the tail.
2. Slide the horizontal stabilizer in the allotted space
of the fuselage, making sure the control horn
installed in the elevator will properly align with the
pushrod and clevis exiting the back of the fuselage.
3. When you are certain the horizontal stabilizer is
centered correctly and in the right place, use the
tape provided to properly secure the stabilizer to
the fuselage. Use the tape on the top and bottom
of each side of the horizontal stabilizer (total of 4
applications).
4. Make sure the throttle stick is in the full down (idle)
position. Turn on the transmitter and plug in the
flight battery.
5. Locate the lower clevis and pushrod exiting the
right side of the fuselage, and attach the clevis to
the outermost hole on the elevator control horn.
Slide the included retainer over the clevis to ensure
the clevis will not open.
6. Make any trim adjustments as necessary prior to
flight (see step 7).
Note: To make trim adjustments to the horizontal
stabilizer:
a. Confirm the throttle stick is in the full down (idle)
position and turn on the DX5e transmitter.
b. Connect the blue EC3 battery connector into the
EC3 device connector on the speed control.
c. Use the elevator trim of the radio by moving up or
down to achieve neutral position when the gimbal is
also at neutral. If these changes are not sufficient,
center the transmitter elevator trim (distinguished by
a long tone), then remove the clevis from the elevator
control horn and turn clevis in or out as needed to
move the elevator alignment back to neutral.
Warning: Always keep hands and all objects away
from the propeller in case the motor is engaged.
A moving propeller can cause severe injury and
damage.
Step 5
Installing or Replacing the Propeller and
Spinner
Your F4U Corsair has come with 2 different propellers.
• The 2-blade (installed) propeller is slightly more
efficient and offers a little more thrust.
• The 3-blade propeller allows for more scale-type
flights, yet performs very well.
1. Remove the prop hub by inserting a hex driver
through the holes drilled in the hub. Carefully
grasp the propeller and turn the prop hub counter-
clockwise to loosen the hub.
2. Slide propeller on. Make sure pitch numbers on
prop are visible from the front of the airplane.
3. Re-install the prop hub by turning it clockwise. The
hex driver should be used as in Step 1 to ensure
the hub is tight.
NOTE: Always confirm the flight battery is unplugged
from the speed control prior to working around the
propeller and cowl.
Step 6
Step 7
30A ESC instructions
The E-flite 30A Pro Brushless ESC is a lightweight, high-
quality, efficient sensorless brushless electronic speed
control with an integrated switch-mode BEC. It can oper-
ate without the need for a separate receiver battery to
power your servos and receivers, saving you weight and
complication. It is capable of up to 30 amps continuous
current when using 3- to 4-series LiPo battery packs.
You can drive up to 5 analog or 4 digital sub-micro-sized
servos with the BEC on any recommended input voltage.
This ESC also features safe power arming along with
advanced programmable features such as low voltage
cutoff, braking, timing, throttle input range, and more,
making this truly a ‘pro series’ speed control. The ESC
installed in the F4U Corsair has been pre-programmed
for 3S low voltage cut-off.
Note: ALWAYS assume the motor and the propeller
are live. ALWAYS keep clear of the propeller at all
times. The high rpm of the brushless motor can
cause severe injury.
E-flite 30-Amp ESC Features:
• Up to 30 amps continuous current with proper air
flow and 35 amps burst current (15 seconds)
• 5V switch-mode BEC capable of 700mAh
continuous current on any recommended
input voltage
• Drive up to 5 analog or 4 digital sub-micro-sized
servos with the BEC on any recommended
input voltage
• 3- to 4-cell LiPo, 9- to 12-cell NiMH/NiCd
input voltage
• Programmable motor braking
• Safe power-arm mode prevents accidental starts
• Programmable low voltage cutoff with settings
for 3-cell LiPo (9.2V), 4-cell LiPo (12V), or 74% of
battery starting voltage
• Programmable throttle input range (1.1ms–1.9ms
or 1.2ms–-1.8ms)
• Programmable soft start for helis and airplanes
• Auto motor shut down if signal is lost or there is
interference
• Programmable timing—5 user-selectable ranges–
use with a large variety of brushless motors
• Optional RS232 Serial Link and software available
for PC programming (EFLARS232)
• Pre-wired connectors—E-flite EC3 on battery input
and 3.5mm female gold bullets on motor
output leads
Specifications
Continuous Current: 30A*
Max Burst Current:
35A (15 sec)*
Length:
51mm (2 in)
Width:
28mm (1.1 in)
Height:
8.7mm (.35 in)
Weight:
31 g (1.1 oz)
Cells:
3-4S LiPo or 9-12 NiMH/NiCd
Battery Input Leads: 16 AWG with E-flite
EC3 Connector
Motor Output Leads: 16 AWG with 3.5mm Female
Gold Bullet Connectors
* Proper cooling required
Optional RS232 Serial Link & Programming Software
Programming your ESC will be much faster and easier
when you purchase the optional RS232 Serial Link and
programming software. This will allow you to update
your ESC using a laptop or PC. You must have a Serial
Port on your computer or you can purchase a separate
USB to DB9 adapter (available at computer retailers).
EFLARS232—RS232 Serial Link/Programming Software
Servo Ratings with BEC Enabled:
Drives up to 5 analog or 4 digital sub-micro-sized servos
with the BEC on any recommended input voltage.
Some servo combinations we have tested in various
models include:
• 1 analog standard servo, 1 digital sub-micro servo,
2 analog sub-micro servos—E-flite Apprentice
15e RTF
• 2 ParkZone (PKZ1081) analog sub-micro servos
and 2 ParkZone (PKZ1090) digital metal gear
sub-micro servos—ParkZone T-28 Trojan RTF &
F4U Corsair RTF
Some other brands and models of servos may have
significantly higher current draw. Digital servos and
binding servos of any kind typically have higher current
draw. As a general rule, micro and sub-micro servos
draw less current which may affect your servo usage
as shown in the examples above. We recommend the
use of a Hangar 9 Servo and Receiver Current Meter
(HAN172), installed between the throttle lead of the
ESC and receiver, to confirm current draw of the actual
servos used. Also, always be sure to position the ESC
for maximum airflow since cooling can significantly aid
in the performance of the BEC.