Kipp&Zonen SMP3 Pyranometers User Manual
Page 57
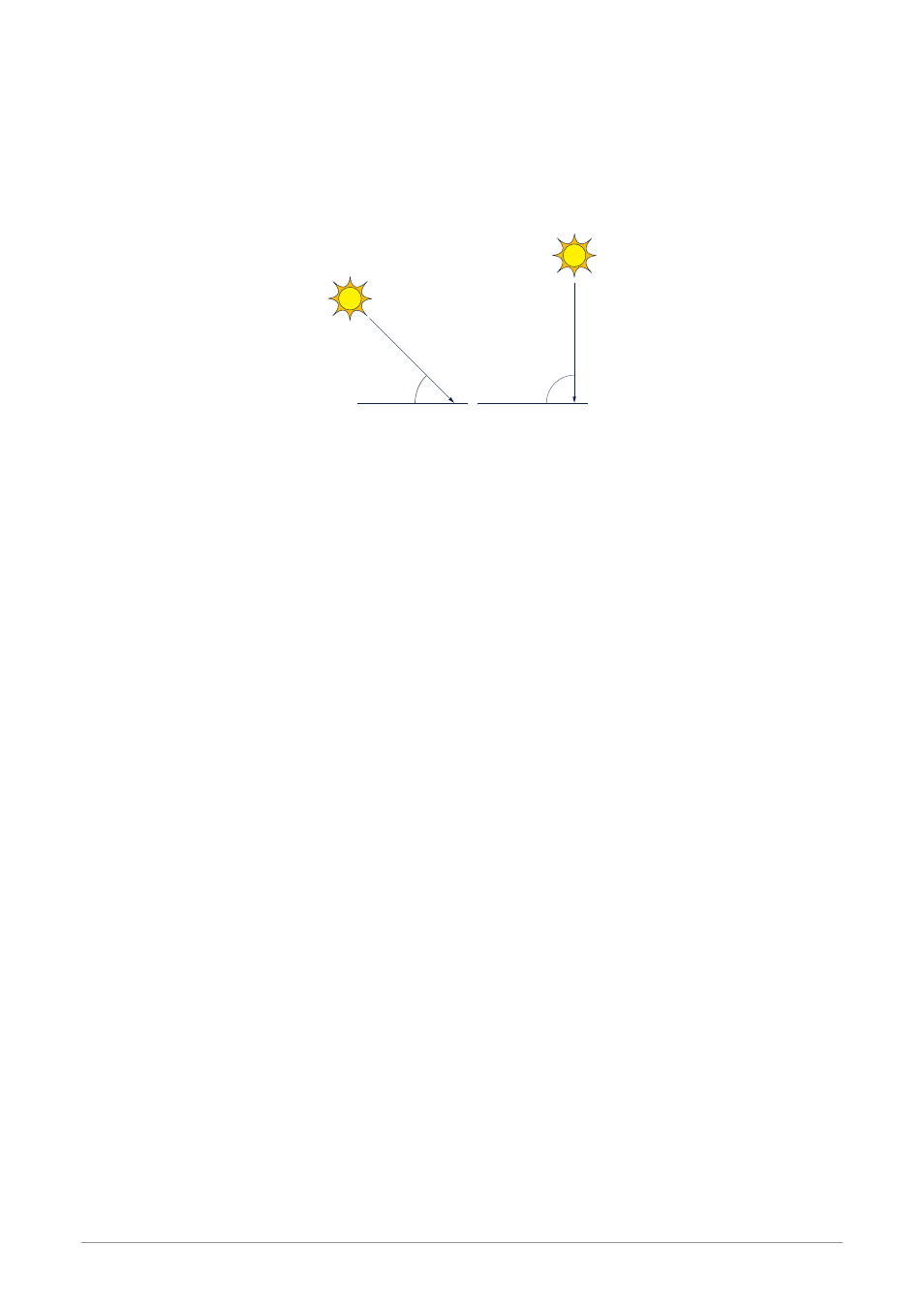
.
Register 4
IO_SCALE_FACTOR
The scale factor defines the number of fractional digits, the range and the position of the decimal point for the following
registers:
IO_SENSOR1_DATA, IO_SENSOR2_DATA, IO_RAW_SENSOR1_DATA and IO_RAW_SENSOR2_DATA. The scale factor is read
only. The default value of the scale factor is set during calibration mode or it can be changed during operation (see register
IO_DEF_SCALE_FACTOR and coil IO_AUTO_RANGE).
If the register
IO_SCALE_FACTOR is not set to 0 then you must multiply or divide the data of register (X), whereas X is one of the
above mentioned registers.
Scale factor = 2
(floating point) result = (integer) register (X) / 100.0
Scale factor = 1
(floating point) result = (integer) register(X) / 10.0
Scale factor = 0
(floating point) result = (integer) register(X)
Scale factor = -1
(floating point) result = (integer) register(X) * 10.0
The default value of register
IO_SCALE_FACTOR is 0. However, this value can be set to a different value if the coil IO_AU-
TO_RANGE is set or a different value is written to the register IO_DEF_SCALE_FACTOR (set default scale factor).
Register 5
IO_SENSOR1_DATA
This register holds the actual data (solar radiation) measured by the sensor. The solar radiation is measured in W/m².
If the register
IO_SCALE_FACTOR is not set to 0 then you must multiply or divide the data as described under register 4.
The raw data from the sensor is calibrated, linearized; temperature compensated and filtered using 2 different kinds of filters
(See
IO_FAST_RESPONSE and IO_TRACKING_FILTER).
Register 6
IO_RAW_SENSOR1_DATA
The raw sensor data is calibrated but not linearized and temperature compensated. If the register
IO_SCALE_FACTOR is not set
to 0 then you must multiply or divide the data as described under register 4,
IO_SCALE_FACTOR.
Register 7
IO_STDEV_SENSOR1
This register is used to calculate the standard deviation over the signal. When the register is read the data is sent to the comput-
er and at the same time a new calculation is started. The next time register 7 is read the standard deviation over the last period
is sent to the computer and a new calculation is started. If the poll frequency is quite high (for example 1 poll per second) then
the standard deviation will be zero or almost zero, but if the poll frequency is very low then the standard deviation can be quite
high, indicating that the data in register 5 or 6 changed dramatically since the last poll. The standard deviation is measured in
0.1 W/m². To convert the data to a floating point, make the following calculation:
(floating point) result = (integer) register (IO_STDEV_SENSOR1) / 10.0
Register 8
IO_BODY_TEMPERATURE
The body temperature sensor measures the temperature of the body in 0.1°C.
The convert the data to a floating point number, make the following calculation:
(floating point) result = (integer) register (IO_BODY_TEMPERATURE) / 10.0
B. Pyranometer physical properties
B.1 Spectral range
The spectrum of the solar radiation reaching the Earth’s surface is in the wavelength range between 280 nm and 4000 nm,
extending from ultraviolet (UV) to the far infrared (FIR). Due to the excellent physical properties of the glass dome and black
absorber paint, Kipp & Zonen SMP series radiometers are equally sensitive in a wide spectral range. 97 - 98 % of the total
energy will be absorbed by the thermal detector.
B.2 Sensitivity
For the SMP series pyranometers the physical sensitivities are converted to a digital output that is identical for all sensors. The
SMP-V versions all have an analogue output of 0 to 1 Volt for -200 to 2000 W/m². The SMP-A outputs are 4 to 20 mA for 0 to
1600 W/m².
B.3 Response time
Any measuring device requires a certain time to react to a change in the parameter being measured. The radiometer requires time
to respond to changes in the incident radiation. The response time is normally quoted as the time for the output to reach 95%
(sometimes 1/e, 63 %) of the final value following a step-change in irradiance. It is determined by the physical properties of the
thermopile and the radiometer construction. SMP series radiometers are set to digitally accelerate the physical response.
B.4 Non-linearity
The non-linearity of a pyranometer is the percentage deviation in the sensitivity over an irradiance range from 0 to 1000 W/m²
compared to the sensitivity calibration irradiance of 500 W/m². The non-linear effect is due to convective and radiative heat
losses at the black absorber surface which make the conditional thermal equilibrium of the radiometer non-linear.
B.5 Tempearture dependence
The sensitivity change of the radiometer with ambient temperature change is related to the thermo-dynamics of the radiometer
construction. The temperature dependence is given as percentage deviation with respect to the calibrated sensitivity at +20 °C.
The SMP series pyranometers have an integrated temperature sensor and use a fourth-order polynomial function to actively
correct for temperature errors over a -40 °C to +70 °C range.
B.6 Tilt error
This is the deviation from the sensitivity at 0 ° tilt (exactly horizontal) over the range from 0 ° to 90 ° tilt under 1000 W/m²
normal incidence irradiance. The tilt response is proportional to the incident radiation. The error could be corrected for, in
applications where it is necessary to install the pyranometer on an inclined surface, but is usually insignificant.
.
Register 9
IO_EXT_POWER_SENSOR
The Ext power sensor measured the external voltage applied to the sensor in 0.1 Volt.
The convert the data to a floating point number, make the following calculation:
(floating point) result = (integer) register (IO_EXT_POWER_SENSOR) / 10.0
Example
Read registers: ‘operational mode to external power’ from Modbus® device with address 1.
Tx
transmitted data to the smart sensor
Rx
received data from the smart sensor
SendModbusRequest (0x04, 1, IO_OPERATIONAL_MODE, 8);
Tx 01 04 00 02 00 08 50 0C
Rx 01 04 10 00 01 00 00 00 00 03 E5 03 E5 00 00 00 F8 00 EA 66 12
Explanation of the received bytes:
01
= MODBUS address
04
= read input registers
10
= number of received data bytes
00 01
= operational mode (mode 1)
00 00
= status flags (none)
00 00 = scale factor = 0 = 1x
03 E5
= 997 decimal = sensor 1 data in W/m²
03 E5
= 997 decimal = raw sensor 1 data in W/m²
00 00
= 0 = standard deviation sensor 1
00 F8
= 248 = 24.8°C.
00 EA
= 234 = 23.4 Volt
66 12
= MODBUS checksum (CRC16)
.
A.5 Discrete inputs
A discrete input can be true or false. A discrete input is read only; a coil can be read or written.
Status indicators
Input Parameter
R/W Def. Mode Description
0
IO_FALSE
R
0
All
Always false (for testing only)
1
IO_TRUE
R
1
All
Always true (for testing only)
2
IO_VOID_DATA_FLAG
R
*
All
Void signal, 1=unstable signal, temperature too low or too high
3
IO_OVERFLOW_ERROR
R
*
All
Overflow, signal out of range
4
IO_UNDEFLOW_ERROR
R
*
All
Underflow signal out of range
5
IO_ERROR_FLAG
R
*
All
General hardware error (set if one of the H/W error flags is set)
6
IO_ADC_ERROR
R
*
All
Hardware error A/D converter
7
IO_DAC_ERROR
R
*
All
Hardware error D/A converter
8
IO_CALIBRATION_ERROR
R
*
All
Calibration checksum error
9
IO_UPDATE_FAILED
R
*
All
Update calibration parameters failed
Legend
Input
Discrete input
Modbus® discrete input 0 is the first discrete input
Coil
Modbus Coil
A coil can be read or written.
Parameter Name
Name of the register
R/W
Read write
R
Read only
R/W Read/write
Def
Default value
default value at power on (0, 1or *) * = undefined
Mode
operation mode
N
available in normal mode
S
available in service mode
C
available in calibration mode (not for users)
F
available in factory mode (not for users)
All
available in all modes
Inputs can be read in all modes but some coils can’t be written in normal mode or service mode.
A.6 Coils
Device control
Coil
Parameter
R/W Def. Mode Description
10
IO_CLEAR_ERROR
R/W 0
All
Select normal operation and clear error (1=clear error)
11 to 17 FACTORY USE ONLY
18
IO_RESTART_MODBUS
R/W 0
All
Restart the device with modbus® protocol
19
FACTORY USE ONLY
20
IO_ROUNDOFF
R/W 1
S,N
Enable rounding of sensor data
21
IO_AUTO_RANGE
R/W 0
S,N
Enable auto range mode (0=no auto range)
22
IO_FASTRESPONSE
R/W 0
S,N
Enable fast response filter (0=no filter)
23
IO_TRACKING_FILTER
R/W 1
S,N
Enable tracking filter (0=no filter)
Note
The default values of the device options are stored in non-volatile memory. The default values can be overruled during
operation. However, at power-on the default values are restored and the smart sensor will start up with the default
values stored in the non-volatile memory.
.
ADC CONTROL
Coil
Parameter
R/W Def. Mode Description
24 to 34 Factory use only
A.7 Read write holding registers
Register 34
IO_DEF_SCALE_FACTOR
The default scale factor is set in the factory mode or service mode and is stored in non-volatile memory. The default scale factor
stored in non-volatile memory is always set after a power-on. However it is possible to change the default setting during opera-
tion by writing a value to the register 34.
Note
This value is not stored in non-volatile memory and is overwritten with the default value at power on.
The following values are valid:
Scale factor = 2
Scale factor = 1
Scale factor = 0
Scale factor = -1
Scale factor 0 is the default value. See also input register 4
IO_SCALE_FACTOR.
A.8 Read discrete inputs
Discrete input 0 IO_FALSE
This discrete input is always false
Discrete input 1 IO_TRUE
This discrete input is always true
Discrete input 2 IO_VOID_DATA_FLAG
The void data flag is raised when the data in register
IO_SENSOR1_DATA or IO_RAW_SENSOR1_DATA is not valid, because the
body temperature of the sensor is too low or too high, when there is an internal overflow condition, because a calculation is out
of range or a division by zero occurred, the reference voltage of the ADC is not stable or the digital filter is not stable. When the
IO_VOID_DATA_FLAG is set, bit 0 in the IO_STATUS_FLAGS is also set.
The
IO_VOID_DATA_FLAG and bit 0 of the IO_STATUS_FLAGS are cleared when the IO_VOID_DATA_FLAG is read by the computer.
Discrete input 3 IO_OVERFLOW_ERROR
This discrete input is raised when an out of range condition occurs and the sensor data (see
IO_SENSOR1_DATA) is above the
maximum value specified by the calibration program or above 29,999. The typical maximum value is 4000 W/m².
When the
IO_OVERFLOW_ERROR is set, bit 1 in the IO_STATUS_FLAGS is also set.
The
IO_OVERFLOW_ERROR and bit 1 of the IO_STATUS_FLAGS are cleared when the IO_OVERFLOW_ERROR is read by the computer.
Discrete input 4 IO_UNDERFLOW_ERROR
This discrete input is raised when an underflow condition occurs and the sensor data (see
IO_SENSOR1_DATA) is below the
minimum value specified by the calibration program or below -29,999. The typical minimum value is -400 W/m².
When the
IO_UNDERFLOW_ERROR is set, bit 2 in the IO_STATUS_FLAGS is also set.
The
IO_UNDERFLOW_ERROR and bit 2 of the IO_STATUS_FLAGS are cleared when the IO_UNDERFLOW_ERROR is read by the
computer.
.
Discrete input 5 IO_ERROR_FLAG
The error flag is raised when there is a (fatal or correctable) hardware error or software error such as: ADC error, DAC error,
calibration error or when the update of the calibration data failed. When the
IO_ERROR_FLAG is raised the error code is copied
to the register
IO_ERROR_CODE (see register 26).
The error flag is cleared when a true condition is written to the coil:
‘IO_CLEAR_ERROR’. This has no effect when the error is fatal
or not resolvable such as a calibration error.
The error flag is always set after a power up, this is to indicate the power went off, or a restart occurred. The computer should
raise the
IO_CLEAR_ERROR in order to reset the error flag.
Discrete input 6 IO_ADC_ERROR
This flag is raised when the A/D converter responsible for the conversion of the analogue signals to digital signals detected a
failure (hard or software).
The ADC error flag is cleared when a true condition is written to the coil:
‘IO_CLEAR_ERROR’ and the error produced by the ADC,
is not fatal.
Discrete input 7 IO_DAC_ERROR
This flag is raised when the D/A converter responsible for the conversion of the digital signal to the analogue output signal
detected a failure (hard or software).
The DAC error flag is cleared when a true condition is written to the coil:
‘IO_CLEAR_ERROR’ and the error produced by the DAC,
is not fatal.
Discrete input 8 IO_CALIBRATION_ERROR
The calibration error flag is raised when the sensor was not calibrated or a checksum error was detected in the calibration data.
This flag can’t be cleared unless the sensor is sent back to the manufacturer or dealer for a re-calibration.
Discrete input 9 IO_UPDATE_FAILED
The update failed is raised when data is written to the non-volatile memory and the update failed. This can happen in calibration
mode when calibration data in written to non-volatile memory or in the service mode when device options are written to the
non-volatile memory.
If this error is set you should retry the last update action. If the error does not disappear then there could be a hardware
problem with the non-volatile memory (EEPROM).
A.9 Read write discrete coils
Coil 10
IO_CLEAR_ERROR
Setting this coil will clear the error only when the error is a non-fatal error. Reading this coil will always return a 0. The coil
IO_CLEAR_ERROR can be used to select the normal mode (see IO_OPERATIONAL_MODE).
The smart sensors will always start-up in the normal mode.
Note
Use
IO_CLEAR_ERROR to return to the normal mode.
.
Coil 20
IO_ROUNDOFF
Setting this coil enables rounding of the data presented in
IO_SENSOR1_DATA and IO_RAW_SENSOR1_DATA.
If not set then the customer should round off the received data before processing the data.
The default value after power on is ON.
If
IO_ROUNDOFF is cleared, then the sensor is not calibrated and could produce more digits, than there are significant digits.
Coil 21
IO_AUTO_RANGE
Setting this coil enables the auto-range feature. The auto-range feature increases the number of digits for small signals
The default value after power on is OFF.
If
IO_AUTO_RANGE is set then the sensor is not calibrated and could produce more digits, than there are significant digits.
Coil 22
IO_FASTRESPONSE
Setting this coil enables the fast response filter. This filter increases the step response of the sensor. Disabling the fast response
give the SMP pyranometers the same response time as the CMP equivalents.
The default value after power on is ON.
Coil 23
IO_TRACKING_FILTER
Setting to this coil enables the tracking filter. The tracking filter reduces the noise of the signal. However, when the filter is on,
the step response on a sudden signal change is decreased. The smart sensor uses variable filter constants to minimize the effect
on the step response.
The default value after power on is OFF.
A.10 Requesting serial number
Register 41
IO_BATCH_NUMBER
The batch number defines the production year of the smart sensor, 11 = 2011, 12=2012 etc.
Register 42
IO_SERIAL_NUMBER
Register 42 defines the 4 digits serial number of the smart sensor. Only the combination of the batch number and serial number
is unique.
A.11 Simple demonstration program
The simple ‘C’ program below will show how to read the sensor data and how to deal with errors. The program will read the
registers: ‘operational mode, status flags, scale factor, and sensor data’ from Modbus® device with address 2 into registers
uOperationMode, uStatusFlags, iScaleFactor and iSensorData. Then the program will check the operation mode (must be
‘normal’) and if there are no errors flags set in iStatusFlags. If there is an error then set the
IO_ERROR_FLAG.
.
UInt16
uOperationalMode = 0;
UInt16
uStatusFlags = 0;
Int16
iScaleFactor = 0;
Int16
iSensorData = 0;
float
fSensorData = 0;
int main (void)
{
while (true)
{
// Send MODBUS request 0x04 Read input registers to slave 2
// Get modus data will wait for the answer and copies the data to registers
// uOperationalMode, uStatusFlags, iScaleFactor and iSensorData
SendModbusRequest (0x04, 2, IO_OPERATIONAL_MODE, 4);
WaitModbusReply ();
GetModbusData ();
If (uOperationalMode != 1)
{
// Send MODBUS request 0x05 write single coil to slave 2
SendModbusRequest (0x05, 2, IO_CLEAR_ERRROR, true);
WaitModbusReply
();
}
else if (uStatusFlags != 0)
{
SendModbusRequest (0x05, 2, IO_CLEAR_ERRROR, true);
WaitModbusReply
();
}
switch (iScaleFactor)
{
case 2: fSensorData = (float)(iSensorData) / 100.0;
case 1: fSensorData = (float)(iSensorData) / 10.0;
case 0: fSensorData = (float)(iSensorData);
case -1: fSensorData = (float)(iSensorData) * 10.0;
default: fSensorData = 0.0;
}
// wait 1 second
Delay (1000);
}
}
.
B.7 Zero offset type A
By physical laws any object having a certain temperature will exchange radiation with its surroundings. The domes of upward
facing radiometers will exchange radiation primarily with the relatively cold atmosphere. In general, the atmosphere will be
cooler than the ambient temperature at the Earth’s surface. For example, a clear sky can have an effective temperature up to
50 °C cooler, whereas an overcast sky will have roughly the same temperature as the Earth’s surface.
Due to this the pyranometer dome will ‘lose’ energy to the colder atmosphere by means of radiative transfer. This causes the
dome to become cooler than the rest of the instrument. This temperature difference between the detector and the instrument
housing will generate a small negative output signal which is commonly called Zero Offset Type A. This effect is reduced by using
an inner dome. This inner dome acts as a ‘radiation buffer’.
This offset can be minimized by applying appropriate ventilation of the instrument. The CVF4 ventilation unit can be used with
the SMP10 and SMP11, no ventilation unit is available for the SMP3.
B.8 Zero offset type B
Proportionally to the ambient temperature the instrument temperature varies and causes heat currents inside the instrument.
This will cause an offset commonly called Zero Offset Type B. It is quantified as the response in W/m² to a 5 K/hr change in
ambient temperature.
B.9 Operating temperature
The operating temperature range of the radiometer is determined by the physical properties of the individual parts. Within the specified
temperature range Kipp & Zonen radiometers can be operated safely. Outside this temperature range special precautions should be
taken to prevent any physical damage or performance loss of the radiometer. Please contact your Kipp & Zonen representative for
further information regarding operation in unusually harsh temperature conditions.
B.10 Field of view
The field of view is defined as the unobstructed open viewing angle of a radiometer. ISO and WMO require that a pyranometer
for the measurement of global solar radiation has a field of view of 180 ° in all directions (i.e. a hemisphere). The inherent field
of view of the instrument should not be confused with the clear field of view of the installation location.
.
B.11 Directional response
Radiation incident on a flat horizontal surface originating from a point source with a defined zenith position (such as the sun)
will have an intensity value proportional to the cosine of the zenith angle of incidence. This is sometimes called the ‘cosine-law’
or ‘cosine-response’ and is illustrated below.
Ideally a pyranometer has a directional response which is exactly the same as the cosine-law. However, in a pyranometer the
directional response is influenced by the detector and by the quality, dimensions and construction of the dome(s). The maximum
deviation from the ideal cosine-response of the pyranometer is given up to 80 ° angle of incidence with respect to 1000 W/m²
irradiance at normal incidence (0 ° zenith angle).
B.12 Maximum irradiance
The maximum irradiance is defined as the total irradiance level beyond which the output is no longer linear and out of specifica-
tions. The analogue output for the SMP’s is set to 2000 W/m², which is sufficient under normal atmospheric conditions. For
special applications (environmental test rooms) the SMP10 and SMP11 can be set higher, up to 4000 W/².
B.13 Non-stability
This is the percentage change in sensitivity over a period of one year. This effect is mostly due to degradation by UV radiation
of the black absorber coating on the thermopile surface.
Kipp & Zonen recommends recalibration every two years. However, for quality assurance purposes some institutes, companies or
networks may require more or less frequent recalibration. Please read the chapter on the calibration procedure for pyranometers
for more information.
B.14 Spectral selectivity
Spectral selectivity is the variation of the dome transmittance and absorption coefficient of the black detector coating with
wavelength and is commonly specified as % of the mean value.
B.15 Environmental
The SMP series are intended for outdoor use under all expected weather conditions. The radiometers comply with IP 67 and
their solid mechanical construction is suitable to be used under all environmental conditions within the specified ranges.
.
B.16 Uncertainty
The measurement uncertainty of a pyranometer can be described as the maximum expected hourly or daily uncertainty with
respect to the ‘absolute truth’. The confidence level is 95 %, which means that 95% of the data-points lie within the given
uncertainty interval representing the absolute value. Kipp & Zonen empirically determine uncertainty figures based on many
years of field measurements for typical operating conditions.
When a pyranometer is in operation, the performance of it is correlated to a number of parameters, such as temperature, level of
irradiance, angle of incidence, etc. If the conditions differ significantly from calibration conditions, uncertainty in the calculated
irradiances must be expected.
For a ‘High Quality’ pyranometer the WMO expects maximum uncertainty in the hourly radiation totals of 3 %. In the daily total
an uncertainty of 2 % is expected, because some response variations cancel each other out if the integration period is long. See
the WMO ‘Guide to Meteorological Instruments and Methods of Observation’ Seventh Edition, 2008. ISO 9060:1990 does not
refer to hourly or daily uncertainties.
Many years of experience has shown that pyranometer performance can be improved concerning zero offset type A by using
a well-designed ventilation system. The Kipp & Zonen CVF4 ventilation unit is recommended for the SMP10 and SMP11 to
minimise this small error.
C. Pyranometer classification to ISO 9060:1990 (E)
α = 45 °
α = 0 °