Pictorial pilot ground checkout, Ground checkout, Must be performed before first flight – TruTrak Pictorial Pilot User Manual
Page 13
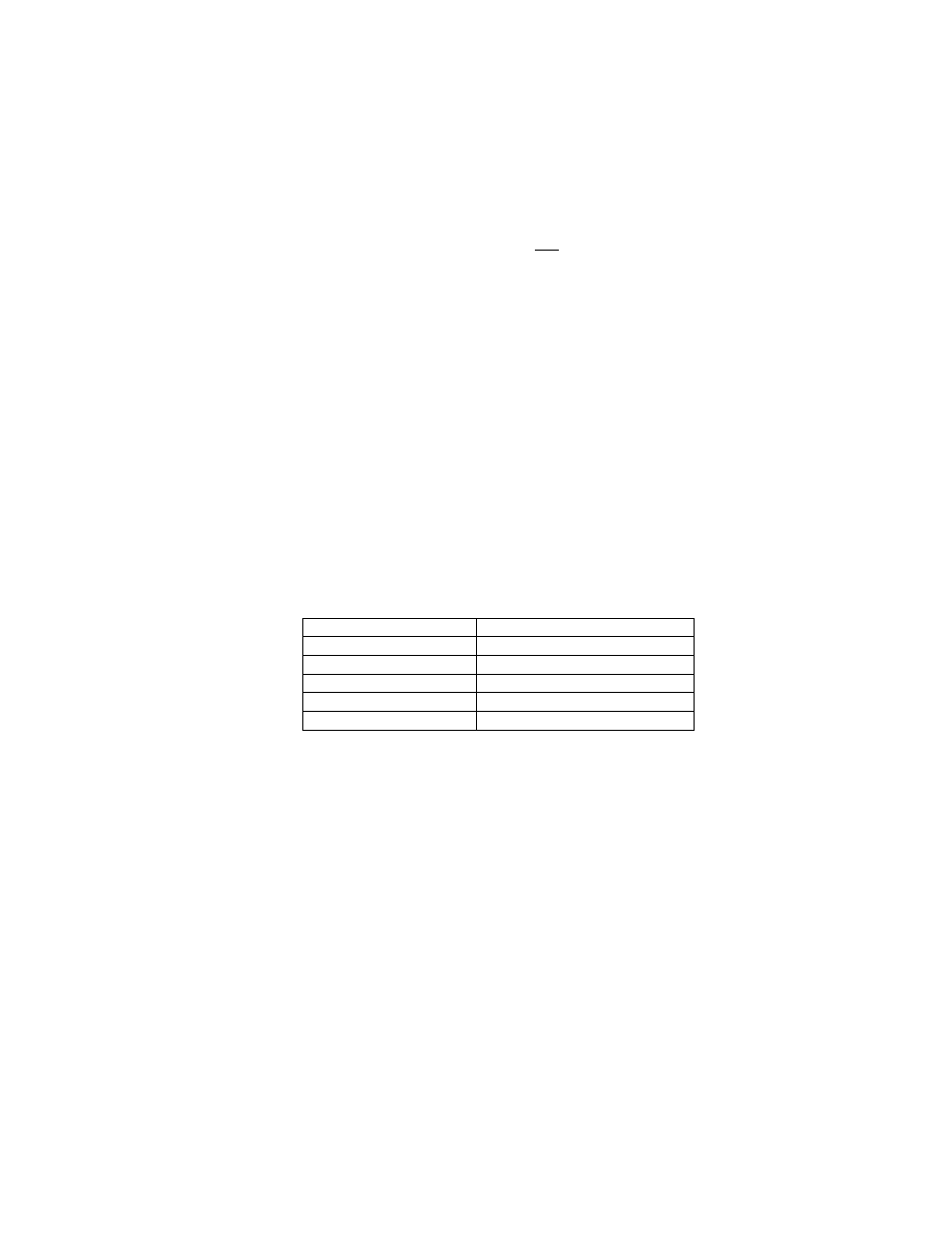
Pictorial Pilot Ground Checkout
Must be performed before first flight
Once wiring is completed the autopilot should be tested in the aircraft while on the ground. The first step is to enter the setup
mode on the autopilot and set all parameters to their correct values. Apply power to the autopilot programmer.
When power is first applied to the unit, the display will show three flashing dash (“–”) characters. After approximately ten
seconds, the autopilot is ready to be set up for operation, indicating three non-flashing dashes on the display. (If a GPS unit
happens to be connected to the autopilot, has a valid position fix, and is running at the correct baud rate, the autopilot will
indicate the word “OFF” instead of the three dashes.)
Engage the autopilot by clicking the knob. Then press and hold the knob for approximately 4 seconds, until the first setup
screen is displayed.
This display will show a flashing “1” and a two-digit number from 0 to 24, representing the autopilot activity level (default 6).
With the activity setup screen on the display, rotate the knob as necessary to adjust the lateral activity value to a value of 1 or 2.
Click the knob to enter the activity value and advance to the next screen.
The second setup screen, with a flashing “2” is used to set the torque of the autopilot servo (default 12). Rotate the knob as
necessary to adjust the torque value close to the maximum value of 12. Once that is done, click the knob to enter that value
and advance to the next screen.
The third setup screen, with a flashing “5” is used to set the micro activity of the autopilot servo (default 0). Rotate the knob as
necessary to adjust the activity value to the value of 0 to 32. This setting is used in aircraft, in which lost motion has been
observed in the control system, or when a slow wing rock persists and adjusting activity (setting 1) does not solve the problem.
Once that is done, click the knob to enter that value and advance to the next screen
The fourth setup screen, with a flashing “3” is used to set the baud rate (speed) of the serial interface to the GPS receiver
(default 96). Rotate the knob to select among five choices as shown in the table below.
Displayed value
RS-232 serial rate
06 600
Baud
12 1200
Baud
24 2400
Baud
48 4800
Baud
96 9600
Baud
9600 and 4800 are the most common settings. Having chosen the desired baud rate, click the knob to enter that value and
advance to the next screen.
The fifth setup screen, with a flashing “4” provides the option for calibrating the internal backup magnetometer. To this
question, leave the answer set to 0 (which means “no”) at this time. This operation will be done at a later time during flight
testing.
Click the knob to leave the setup mode. The Pictorial Pilot display will now show “–| – |–” indicating the magnetic “heading-
hold” mode. (If the GPS were indicating sufficient ground-speed for flight, the display would be showing the current ground
track instead.)
Push and hold the knob for approximately 1-1/2 seconds. The Pictorial Pilot display will now return to its disengaged (off)
state, which is three “–” characters if no GPS fix has been obtained, or “OFF” if a GPS position fix has been obtained, and the
“AP” light will turn off as well.
While the autopilot is in its disengaged (off) mode, press and hold the knob. The display will now show “–| – |–” with the
center dash character blinking, indicating the Manual Gyro Set operation. Continue to hold the knob in for about 10 seconds
while the autopilot is not being moved about, to re-center the gyro manually.
The next step in the check-out procedure is to verify that the servo runs, and in the correct direction. Click the knob to again
engage the autopilot. The servo should be responding at this time, moving the controls only very slowly in attempt to hold
magnetic heading constant. Rotate the knob to right and select a heading approximately 20 degrees to the right. The autopilot
will now move the controls in an attempt to cause a turn towards the right. If servo direction is not correct, the wires going to
pins 4 and 5 of the roll servo (pins 11 and 12 on the main connector) must be reversed to achieve the correct response. If the
TruTrak Flight Systems Pictorial Pilot Installation & User Guide
December 2009 11 8300-011 Rev B