Safety instructions, Service instructions, Warning – Modern AG Grapple User Manual
Page 14: Continued), Daily or every 8 hours of operation, Safety sign identification and replacement
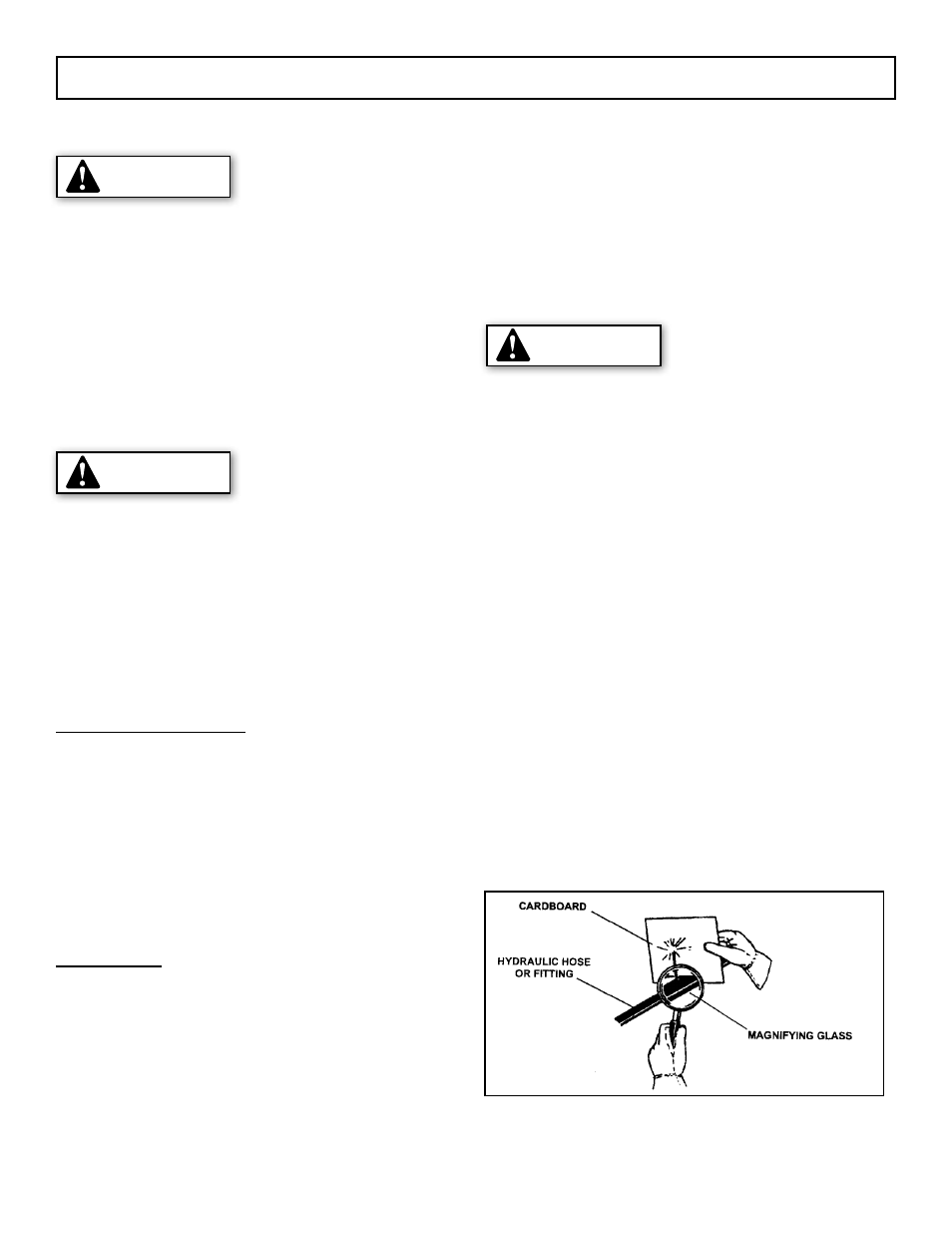
14 - Grapple
mAiNTeNANCe SeCTiON
Never GO uNDerNeATH eQuiPmeNT. Never
place any part of the body underneath equipment or
between moveable parts even when the engine has
been turned off. Hydraulic system leak down, hydraulic
system failures, mechanical failures, or movement of
control levers can cause equipment to drop or rotate
unexpectedly and cause severe injury or death.
Read Manual for service instructions or have service
performed by a qualified dealer.
Keep all persons away from operator control area while
performing adjustments, service, or maintenance.
Before dismounting power unit or performing any
service or maintenance, follow these steps: disengage
power to equipment, lower all raised components to
the ground, operate valve levers to release any hydraulic
pressure, set parking brake, stop engine, remove
key, and unfasten seat belt. Never leave equipment
unattended with engine running.
General information
Your attachment was designed to be almost
maintenance free. Little effort is needed to keep it in
top condition. It is, however, important to follow these
procedures to get full performance and longevity out of
the equipment. IMpORTANT: When replacing parts, use
only factory approved replacement parts. Manufacturer
will not claim responsibility for use of unapproved parts
or accessories and/or other damages as a result of their
use.
lubrication
The lubrication your Grapple Bucket will need is the
greasing of the grapple clamp pivot tube. Two grease
fittings have been installed in each clamp pivot tube to
facilitate this task.
We recommend greasing these fittings both before and
after the initial eight (8) hours of use and then every
(40) hours of use thereafter.
Thoroughly clean the grease zerks before servicing.
Dirt mixed with lubricant will rapidly wear parts. Keep
it clean.
DAily Or every 8 HOurS OF OPerATiON
Replace any missing bolts or nuts with approved
replacement parts. Check hydraulic system for
leaks.
See procedure below.
Visually inspect the
machine for worn parts or cracked welds. Repair
as necessary.
Escaping fluid under pressure can have sufficient
force to penetrate the skin, causing serious personal
injury. Fluid escaping from a very small hole can be
almost invisible. Use a piece of cardboard or wood,
rather than hands to search for suspected leaks.
Keep unprotected body parts, such as face, eyes,
and arms as far away as possible from a suspected
leak. Flesh injected with hydraulic fluid may develop
gangrene or other permanent disabilities.
If injured by injected fluid, see a doctor at once.
If your doctor is not familiar with this type of
injury, ask him or her to research it immediately to
determine proper treatment.
WArNiNG
WArNiNG
WArNiNG
6
15
SAFETY INSTRUCTIONS
(continued)
SAFELY OPERATE EQUIPMENT
Do not operate equipment until you are completely trained by a qualified operator in how to use
the controls, know its capabilities, dimensions, and all safety requirements. See your machine's
manual for these instructions.
• Operate only from the operator's station. Always use the seat belt if the prime mover has a
ROPS. Do not use a seat belt if there is not ROPS. Check the seat belt daily and replace if
frayed or damaged.
• Specified lift capacities must not be exceeded. See loader specifications.
• An operator must not use drugs or alcohol, which can change their alertness or coordination.
An operator taking prescription or over-the-counter drugs should seek medical advice on
whether or not they can safely operate equipment.
• Never use any of these attachments for a work platform or personnel carrier.
• Always check locking pins before tilting or operating any attachment.
• Keep all step plates, grab bars, pedals, and controls free of dirt, grease, debris, and oil.
• Never allow anyone to be around the equipment when it is operating.
• Do not allow riders on the attachment or the prime mover.
• Do not operate the equipment from anywhere other than the correct operator's position.
• Never leave equipment unattended with the prime mover’s engine running, or with this attach-
ment in a raised position.
• Do not handle round bales unless loader is equipped with approved bale handling attachments.
• Do not detach loader from tractor with any of these attachments installed. Equip loader with
material bucket when detaching.
• Stop loader gradually when lowering or lifting loads
• Before exiting the prime mover, lower the attachment to the ground, apply the brakes, turn off
the prime mover's engine, and remove the key.
• Do not alter or remove any safety feature from the prime mover or this attachment.
• Know your work site safety rules as well as traffic rules and flow. When in doubt on any safety
issue, contact your supervisor or safety coordinator for an explanation.
• A heavy load can cause instability of the prime mover. Use extreme care during travel. Slow
down on turns and watch out for bumps. The prime mover may need additional counter-weights
to counter-balance the weight of the attachment.
• Do not heap load heavy material where the combined weight of the bucket and the material
could exceed the rated lifting capacity of the loader.
• Be sure the load does not stick out too far in front of the bucket. A light load sticking out too far
can have the same tipping effect as a heavy load carried in close.
• Do not exceed the lift capacity of your loader. See loader specifications.
• Make sure all loads are secure before lifting. If lifting with the grapple and the load appears to
be unstable, lower the load, open the grapple and reposition the load to attain full stability.
WARNING!
SERVICE INSTRUCTIONS
(continued)
DO NOT MODIFY MACHINE OR ATTACHMENTS
Modifications may weaken the integrity of the and may impair the function, safety, life, and perform-
ance of the attachment. When making repairs, use only the manufacturer's genuine parts,
following authorized instructions. Other parts may be substandard in fit and quality. Never modify
any ROPS (Roll Over Protection Structure) or FOPS (Falling Object Protective Structure) equip-
ment or device. Any modifications must be authorized in writing by the manufacturer.
WARNING!
Escaping fluid under pressure can have sufficient force to penetrate the skin, causing seri-
ous personal injury. Fluid escaping from a very small hole can be almost invisible. Use a
piece of cardboard or wood, rather than hands to search for suspected leaks.
Keep unprotected body parts, such as face, eyes, and arms as far away as possible from a
suspected leak. Flesh injected with hydraulic fluid may develop gangrene or other perma-
nent disabilities.
If injured by injected fluid, see a doctor at once. If your doctor is not familiar with this type
of injury, ask him or her to research it immediately to determine proper treatment.
WARNING!
DAILY OR EVERY 8 HOURS OF OPERATION
Replace any missing bolts or nuts with approved replacement parts.
Check hydraulic system for leaks. See procedure below.
Visually inspect the machine for worn parts or cracked welds. Repair as necessary.
SAFETY SIGN IDENTIFICATION AND REPLACEMENT
Safety Sign placement and identification for all of the attachments can be found on the parts diagrams and lists locat-
ed at the back of this manual. The safety signs are identified by their part numbers with reductions of the actual safety
signs located on the page. Use this information to order replacements for missing, illegible or damaged safety signs.
When replacing parts with safety signs attached, the safety sign must also be replaced. All Safety Signs are free of
charge. Contact your local dealer or manufacturer for replacements.
Replacing Safety Signs
1. Clean the area of application with nonflammable solvent.
2. Wash the same area with soap and water.
3. Allow the surface to fully dry.
4. Remove the backing from the safety sign exposing the adhesive surface.
5. Apply the safety sign to the location shown in the parts diagram.
6. Smooth out any bubbles.
Helpful Hints: (1) Decals adhere to a warm surface better than a cold surface. (2) Applying heat (from a hair
dryer) will greatly improve your ability to remove a damaged decal before preparing the surface for installation
of a new one.