Rega RP8 User Manual
Page 4
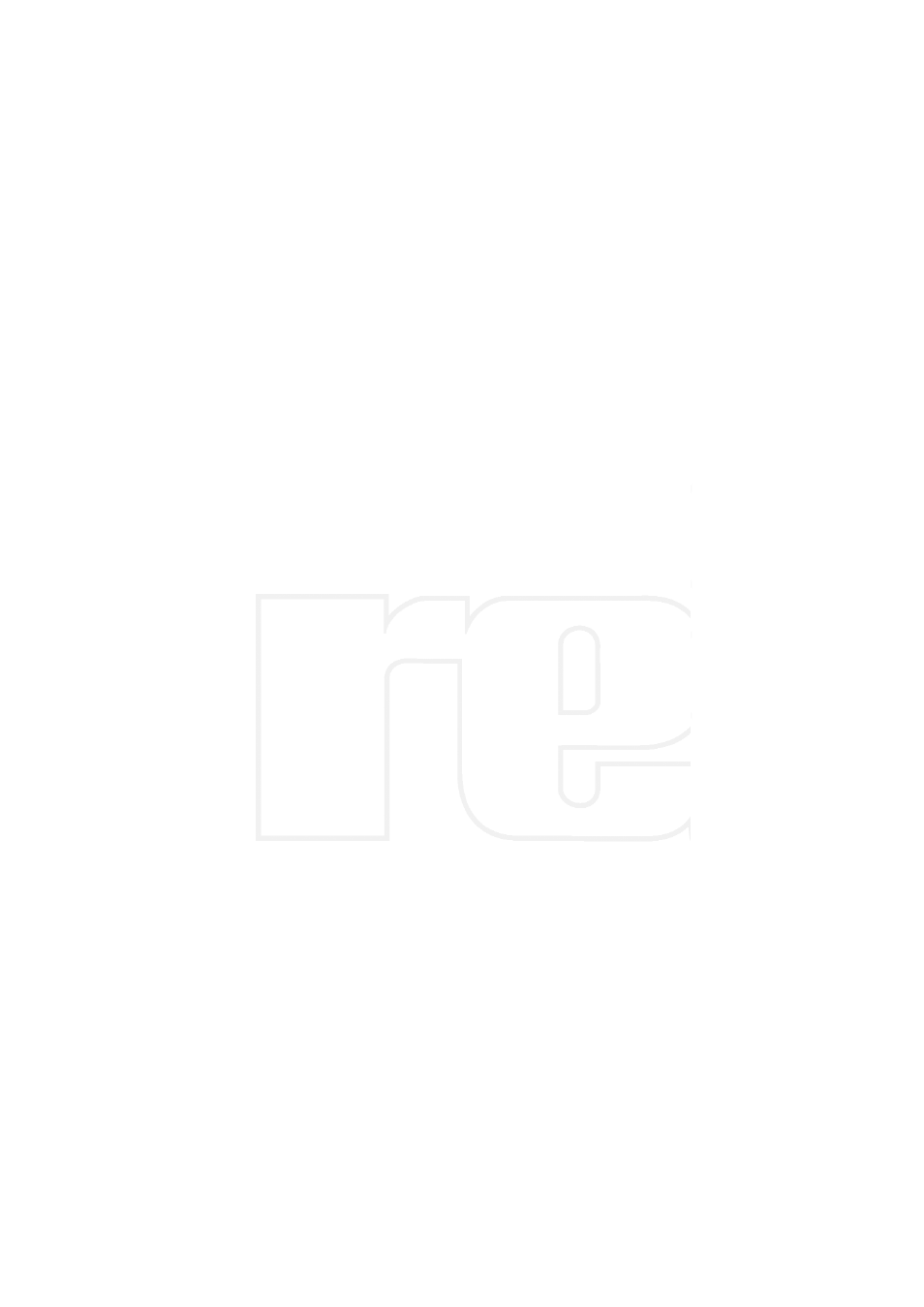
3
DESIGN AND INNOVATION
SKELETAL PLINTH DESIGN WITH POLYOLEFIN FOAM CORE
Controversially Rega has always researched methods of producing light but stiff and
rigid plinths. The technology is simple: unwanted noise at microscopic levels is
developed by the turntable motor and main bearing. The plinth can also pick up airborne
vibration from the music. From the beginning in the 1970’s Rega pioneered the use of a
stressed skin structure for the plinth. This uses two layers of phenolic resin with a
lightweight particle or fibre board sandwiched between the skins. This technique has
been used in many applications where stiff, light structures are needed such as an
aircraft wing or a Formula 1 chassis.
The current revival in turntables has allowed Rega to research and develop higher
technology structures for the customer who is happy to pay a little more for higher
sound quality. The RP8 turntable utilises a unique new stressed skin structure
produced from thin phenolic skins sandwiching a featherweight nitrogen expanded,
closed cell, polyolefin foam core. This material has been developed exclusively for Rega
over a three year period. The RP8 plinth is 7 times lighter than the weight of the original
Planar 3 plinth. In addition Rega has added even more stiffness in the crucial area
between the arm and the main bearing.
SUPER FLYWHEEL EFFECT TRIPLE LAYER GLASS PLATTER
The new RP8 three piece laminated glass platter is the result of a collaboration with a
small, emerging, young British glass engineering company. As a general rule the only
part of a turntable that requires extra mass is the turntable platter in order to achieve
constant rotational speed. However a heavier platter creates more problems for the
main bearing design so again an ideal compromise creates the best solution.