Rite-Ride 1003 User Manual
Page 2
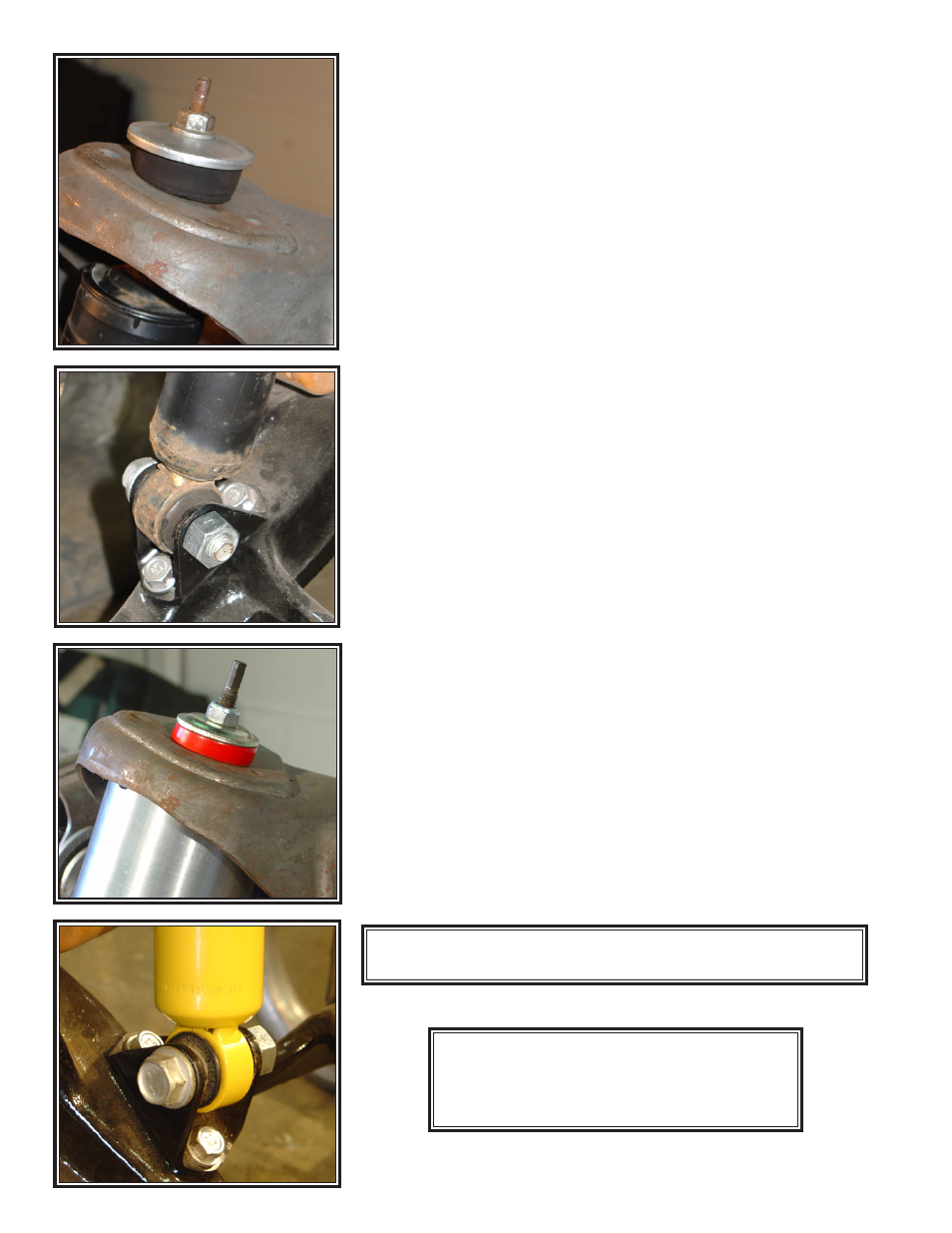
STEP 3— INSTALLING THE AIR OVER SHOCK
Insert the Air Over shock into the upper and lower shock mounts.
Note:
The air fitting should point towards the rear of the truck and the frame.
Attach the bottom of the shock to the lower suspension with the nut and
bolt removed in Step 1. From the top of the upper shock mount, install one
of the upper bushings, with the nipple pointing down, onto the threaded
portion of the rod on top of the shock, followed by one of the large flat
washers. Next, install the nylock hex nut onto the threaded portion of the
rod. Make sure all fasteners are tight.
See Figures “D”, “E” & “F”.
STEP 4— INSTALLING THE AIR LINE AND INFLATION VALVE
Uncoil the air line tubing and cut it into two equal lengths.
DO NOT FOLD
OR KINK THE TUBING. Try to make the cut as square as possible. Insert
one end of the tubing into the elbow fitting installed into the shock. Push
the tubing into the fitting as far as possible,
see Figure “G”.
Select a location on the vehicle for the air inflation valves. The loca-
tion can be on the bumper or the body of the vehicle, as long as it is in a
protected location so the valve will not be damaged, but maintain acces-
sibility for the air chuck,
see Figure “H”. Drill a 5/16" hole and install the
air inflation valve using two 5/16" flat washers per valve as supports,
see
Figure “H”. Run the tubing from the air helper spring to the inflation valve,
routing it to avoid direct heat from the engine, exhaust pipe, and away from
sharp edges. Thermal sleeves have been provided for these conditions. If a
thermal sleeve is required simply slide the sleeve over the air line tubing to
the location requiring protection. The air line tubing should not be bent or
curved sharply as it may buckle. Secure the tubing in place with the nylon
ties provided. Push the end of the air line tubing into the inflation valve as
illustrated,
see Figure “H”.
STEP 5— CHECK THE SYSTEM
Once the inflation valves are installed inflate the Air Over shocks to
70 psi
and check the fittings for air leaks with an applied solution of soap and water.
If a leak is detected at a tubing connection then check to make sure that
the tube is cut as square as possible and that it is pushed completely into
the fitting. The tubing can easily be removed from the fittings by pushing
the collar towards the body of the fitting and then pulling out the tube. If a
leak is detected where the brass fitting screws into the shock, remove the
tubing by pushing the collar towards the body of the fitting and then pull-
ing out the tube, then screw the brass fitting into the shock one additional
turn. Reinstall the tubing and re-inflate the air springs and check for leaks
as noted above.
This now completes the installation. Install the wheels and torque the
lug nuts to the manufactures specifications. Raise the front of the vehicle,
remove the jack stands, and lower the vehicle back onto the ground.
FOR
BEST RIDE use only enough air pressure in the air helper springs to level
the vehicle when viewed from the side (front to rear). This amount will vary
depending on the load, location of load, condition of existing suspension
and personal preference.
FIGURE “E”
NOTE: DO NOT remove the air spring assembly from the shock.
This will cause damage to the product and void the warranty.
FIGURE “B”
FIGURE “C”
FIGURE “D”
NOTE:
MIN PRESSURE
10 PSI
MAX PRESSURE (LOADED)
100 PSI