Bendix Commercial Vehicle Systems BENDIX 720CC COMPRESSOR User Manual
Page 6
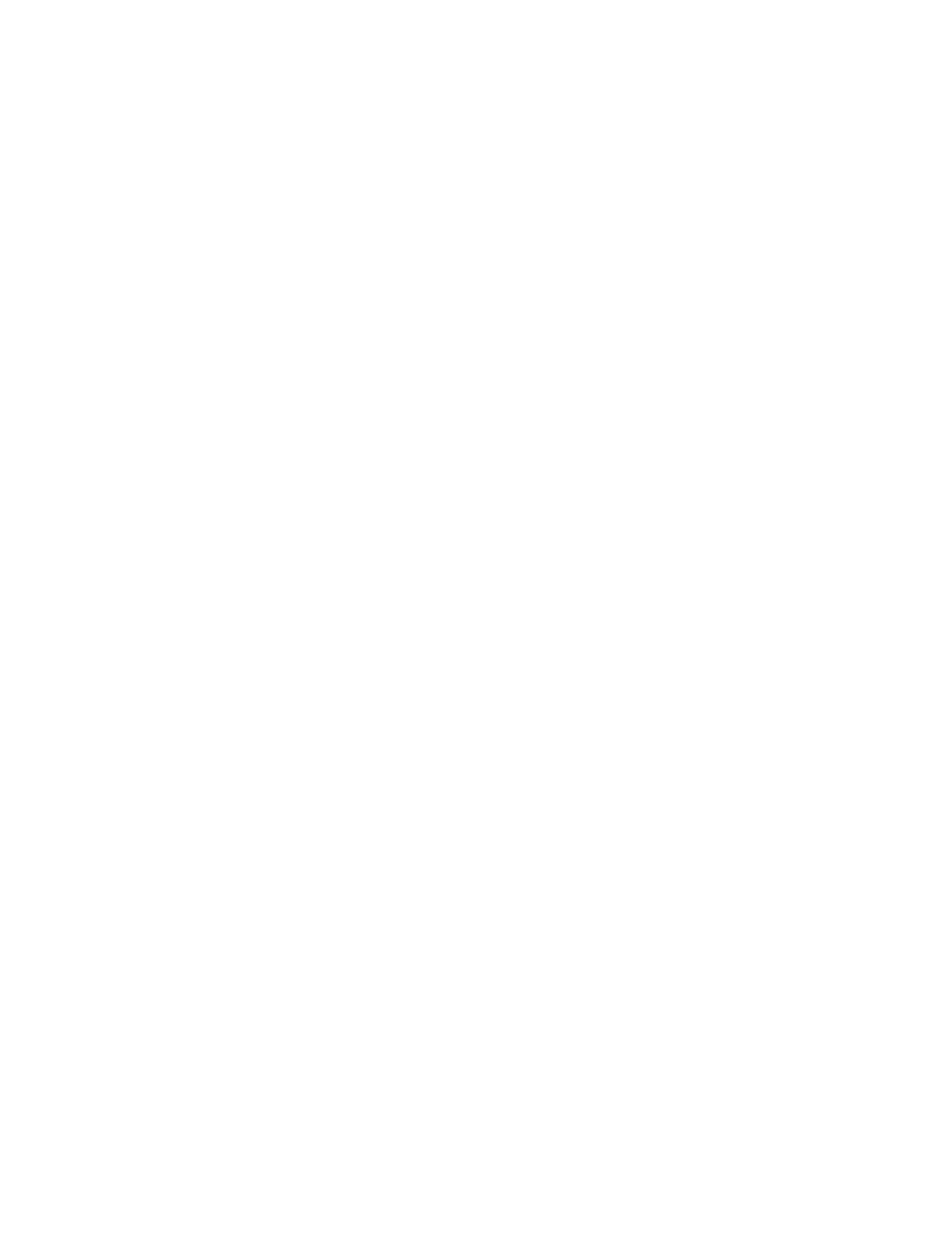
6
LUBRICATION INSPECTION
The compressor utilizes an internal oil feed design. Check
the exterior of the compressor (e.g. around the mounting
face) for the presence of oil seepage, and refer to the
troubleshooting section for appropriate tests and corrective
action. Refer to the tabulated technical data in the back of
this manual for oil pressure minimum values.
OIL PASSING INSPECTION
All reciprocating compressors pass a minimal amount of
oil. Air dyers will remove the majority of oil before it can
enter the air brake system. For particularly oil sensitive
systems, the Bendix
®
PuraGuard
®
system can be used in
conjunction with a Bendix
®
air dryer.
If compressor oil passing is suspected, refer to the
troubleshooting section (starting on page A-1) for the
symptoms and corrective action to be taken. In addition,
Bendix has developed the “Bendix
®
Air System Inspection
Cup” — or Bendix
®
BASIC
™
kit — to help substantiate
suspected excessive oil passing. The steps to be followed
when using the BASIC kit are presented in APPENDIX B.
COMPRESSOR DRIVE INSPECTION
Check for noisy compressor operation, which could indicate
excessive drive component wear. Adjust and/or replace
as necessary. Check all compressor mounting bolts and
retighten evenly if necessary. Check for leakage. Repair
or replace parts as necessary.
CHARGING SYSTEM UNLOADING & GOVERNOR
TEST
Note: The Bendix
720cc DLU-style twin cylinder
compressor does not contain components to unload
the compressor. Therefore, the compressor pumps
continuously. In most systems that utilize an air dryer, the
governor and DLU-style air dryer are used to unload the
system (e.g. air is not being delivered to the brake system
reservoirs). When system unloading occurs, air from the
compressor will typically flow out the exhaust port of the
air dryer. Refer to Figure 6.
Test and inspect the unloading system (e.g. air dryer and
governor) for proper operation and pressure settings.
1. Make certain the unloader system lines (illustrated in
Figure 6) are connected and leak free.
2. Cycle the charging system between the loaded and
unloaded mode several times. This can be achieved by
applying the brakes to bleed down the system pressure.
Make certain that the governor cuts-in (charging
system resumes compressing air) at a minimum of
105 psi. Governor cut-out (charging system stops
delivering air to the brake system reservoirs) should be
approximately 15 - 20 psi greater than cut-in pressure.
Adjust or replace the governor as required.
AIR INDUCTION
The Bendix
®
720cc twin cylinder compressor is only
permitted to be naturally aspirated – use of an engine
turbocharger as an air source is not allowed.
PREVENTIVE MAINTENANCE
Regularly scheduled maintenance is the single most
important factor in maintaining the air brake charging
system. Refer to
Table A: Maintenance Schedule and
Usage Guidelines in the troubleshooting section (page
A-3) for a guide to various considerations that must be
given to maintenance of the compressor and other related
charging system components.
Important Note: Review the Bendix
Warranty Policy
before performing any intrusive maintenance procedures.
An extended warranty may be voided if intrusive
maintenance is performed during this period.
EVERY 6 MONTHS, 1800 OPERATING HOURS,
OR AFTER EACH 50,000 MILES — WHICHEVER
OCCURS FIRST — PERFORM THE FOLLOWING
INSPECTIONS AND TESTS.
AIR INDUCTION INSPECTION
A supply of clean air is one of the single most important
factors in compressor preventive maintenance. Since
the air supply for the 720cc twin cylinder compressor and
engine is the engine air cleaner, periodic maintenance of
the engine air filter is necessary.
Inspect the compressor air induction system each time
engine air cleaner maintenance is performed.
1. Inspect the intake hose adapters for physical damage.
Make certain to check the adapters at both ends of the
intake hose or tubing.
2. Inspect the intake hose clamps and tighten them if
needed.
3. Inspect the intake hose or line for signs of drying,
cracking, chafing and ruptures and replace if necessary.
4. Inspect the compressor’s cast inlet tube for physical
damage.
COMPRESSOR COOLING INSPECTION
Inspect the compressor discharge port, inlet cavity and
discharge line for evidence of restrictions and carbon
buildup. If more than 1/16" of carbon is found, thoroughly
clean or replace the affected parts. In some case, carbon
buildup indicates inadequate cooling. Closely inspect the
compressor cooling system. Check all compressor coolant
lines for kinks and restrictions to flow. Minimum coolant line
size is 3/8" Inside Diameter (I.D.) Check coolant lines for
internal clogging from rust scale. If coolant lines appear
suspicious, check the coolant flow and compare to the
tabulated technical data present in the back of this manual.