S&S Cycle Forged Pistons For Stock Bore And 35/8 Bore Harley-Davidson 1936-99 Big Twin And 1957- Present Sportster Models User Manual
Page 2
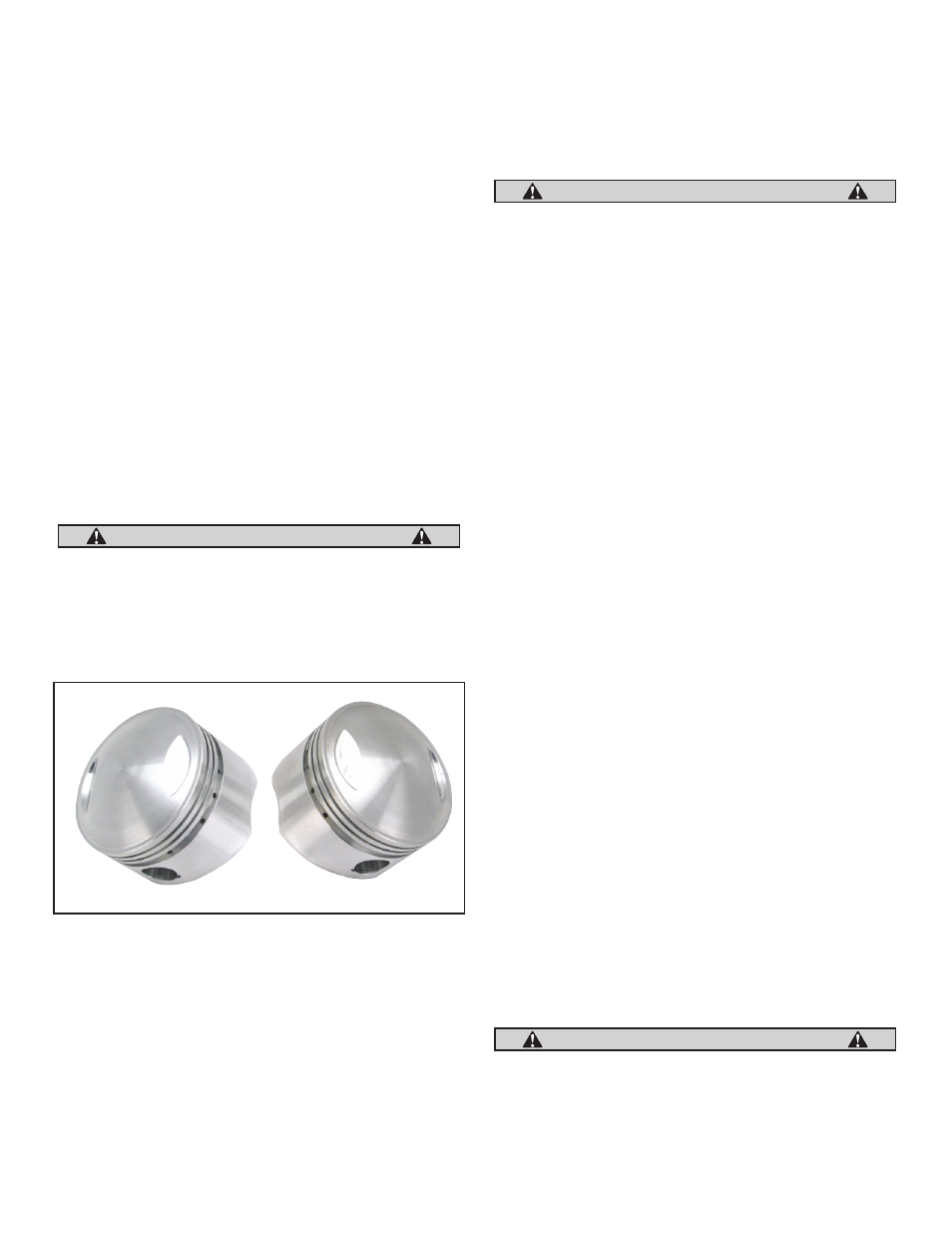
2
GENERAL INFORMATION
1. For maximum piston and ring life, fit pistons using close fit
dimensions. Close fit requires absolute adherence to new engine
break-in as described on page 6.
2. For immediate drag strip use, fit pistons using loose fit dimensions.
Break in rings and pistons with 50 easy miles if possible. Piston and
ring life will be reduced with loose fit dimensions.
3. Measure all pistons at widest point across thrust face, perpendicular
to wristpin hole. Several measurements should be taken to locate
widest point. Typically, this will be at bottom of piston skirt for pre-
1984 Hareley-Davidson® big twins, and approximately 1⁄2" below
level of wristpin hole in pistons for Evolution® engines. If pre-1984
piston is notched for placement in rear cylinder, use measurement
directly above notch for skirt measurement.
4. S&S® recommends #220-#280 grit stone for final honing of stock
bore and Sidewinder®, S&S T124 and S&S big bore cylinders.
5. Follow procedure recommended in Harley-Davidson® service
manual for boring and honing stock bore cylinders. Follow
instructions included with S&S Cylinder Torque Plate Kit when
boring and honing S&S stock bore and 35⁄8" bore cylinders. Torque
plates must be used when boring or honing aluminum cylinders to
simulate compressive stress in an assembled engine. Cylinder bores
will not be straight when engine is assembled, if torque plates are
not used.
CAUTION
Failure to follow instructions and perform required clearancing,
installation and/or break-in procedures may result in damage
to pistons and/or other engine components not covered under
warranty
PISTON INSTALLATION
NOTE: Pistons may have piston to piston clearance on both the front and
rear. The notches must face each other. Pistons for pre-1984 application
have no wristpin offset and can be installed in the front or rear. Pistons for
1984-up applications should be installed according to the marks on the
top of the piston.
1. Check all installations for minimum of .060" clearance between
pistons at closest point near bottom of stroke.
2. Check all installations for minimum of .060" clearance between
pistons and flywheels at bottom of stroke. Replacement pistons
may or may not have adequate clearance. Compare replacement
pistons with ones being replaced and make corrections accordingly.
Picture 1
NOTE: In all cases it is the engine builder's responsibility to confirm proper clear-
ances when assembling an engine. This is especially critical with performance
components such as higher compression pistons and high lift camshafts. In
addition to clearances mentioned, .060" valve-to-piston clearance must be
confirmed.
CAUTION
Failure to establish proper clearances can result in severe engine
damage not covered under warranty.
WRISTPIN RETAINER INSTALLATION
NOTE: Thoroughly clean wristpin before installation, paying particular
attention to bore. Pass clean, lint-free cloth back and forth through wrist-
pin bore several times to insure removal of contaminants.
1. If wristpin clips are used, insure that groove in piston is free of burrs
and foreign matter.
2. Round "wire" style clips identical to and interchangeable with stock
Harley-Davidson® Evolution® clips. Round wire clips require wristpins
with specially chamfered ends. Install wire clips using procedure
recommended in a Harley-Davidson® service manual. End of clip
must rest over notch in piston below wristpin hole to allow removal
of clip in future. Be sure clip is fully seated in groove.
RING INSTALLATION
1. Ring widths on some piston series are subject to change from time
to time. Part numbers of rings originally supplied with pistons
should be recorded for future reference in the event replacement
rings are required. Measure rings to ensure that you get the correct
replacement ring set.
2. The majority of ring kits presently supplied by S&S® contain a moly
faced top ring, a cast, reverse torsion second ring, and a three piece
oil ring. This may be confirmed as follows:
a. Top compression ring has a gray finish that is relatively light in
color, and may or may not have a slight bevel along the inner edge.
It has no dot or other identifying mark. The light color can best be
recognized by comparing compression rings to each other beneath
a good light. Install light colored ring without dot in top groove,
bevel up. If there is no bevel, ring can be installed either side up.
b. Second compression ring has a darker, charcoal gray finish and
slight bevel along inner surface. This ring has a dot. See Figure 1.
Install in second or middle groove with dot up.
c. Oil rings are three piece type with two rails and one expander. Do
not shorten expander for any reason! Installation is straightforward
with one rail placed above expander, other rail below expander.
Rails may be shortened to correct gap, but burrs must be carefully
removed.
NOTE: In some cases, same expander is used for several bore sizes. Over-
size rings will not necessarily have a larger expander.
CAUTION
Failure to remove burrs may cause engine damage.
Incorrect installation of rings may result in poor performance,
excessive oil consumption or engine damage.