Meltric PFQ User Manual
Pf/pfq, Operating instructions, Warning
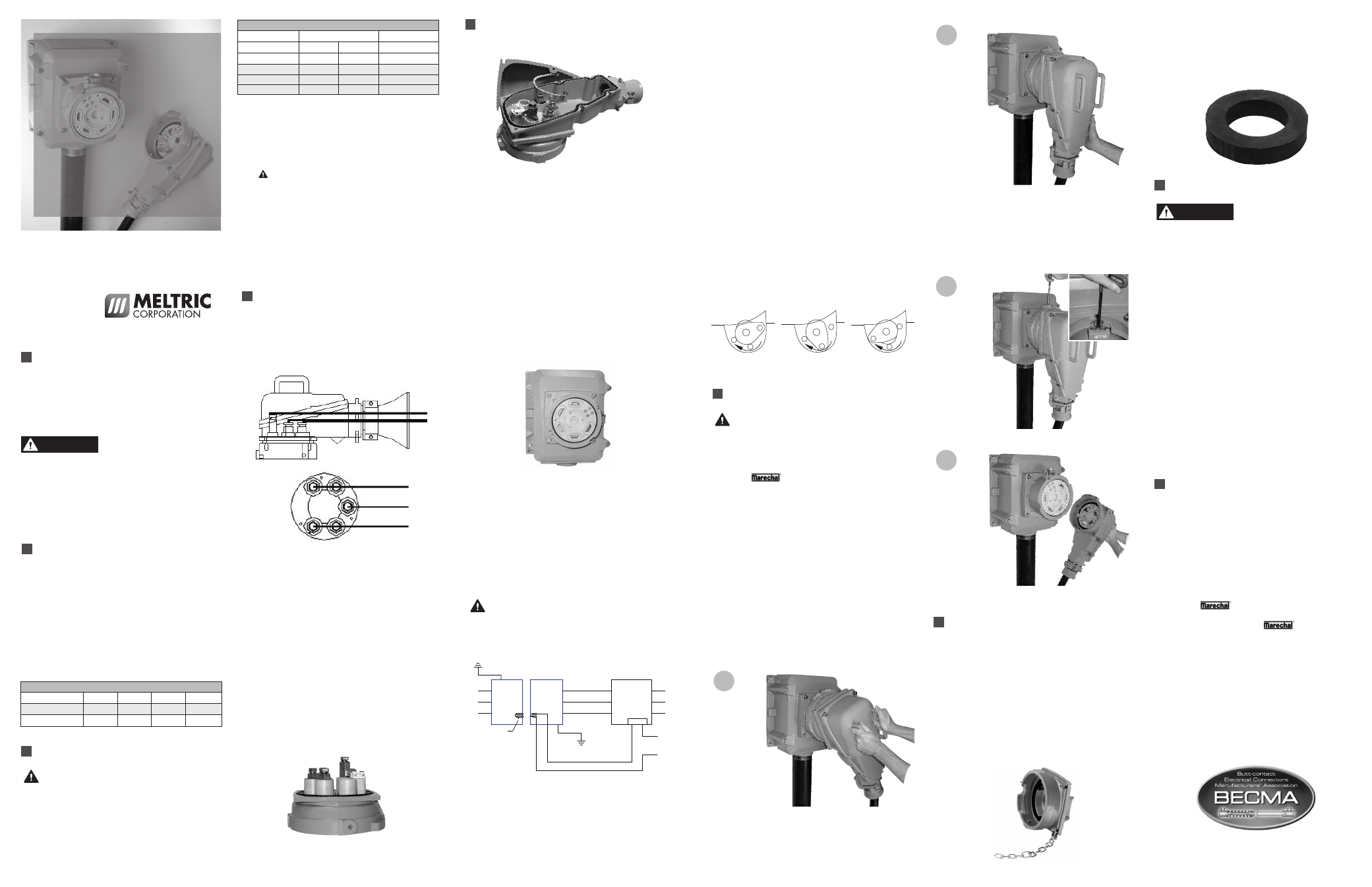
gENERAL
PF and PFQ Series plugs and receptacles are engi-
neered for use in high amperage applications where
routine plug insertion and high reliability are required.
To ensure proper installation and use of the product,
please follow all of the instructions carefully.
There are inherent dangers
associated with electrical
products. Failure to follow safety precautions can
result in serious injury or death. These instructions
must be followed to ensure the safe and proper
installation, operation and maintenance of the Meltric
devices. Before installation, disconnect all sources of
power to the circuit to eliminate the risk of electrical
shock. In order to prevent disconnection under
load, electrical interlocking is required.
RATINgS
PF and PFQ Series plugs and receptacles are UL
and CSA listed according to UL 1682 and CSA C22.2
No.182.1 These listings only apply for 300A and
400A devices at 600V or less. 600A devices are
not UL or CSA listed. WARNINg! All PF and PFQ
devices are provided with manually operated auxiliary
contacts that must be wired to the coil of a contactor
or similar switching device to prevent accidental con-
nection or interruption of live main power contacts.
See schematic for safety circuit example. The ratings
for auxiliary contacts are shown in Table 1.
INSTALLATION
PF and PFQ devices should be installed by
qualified electricians in accordance with all
applicable local and national electrical codes.
Before starting verify that the power is off, that the
product ratings are appropriate for the application,
and that the conductors meet NEC code require-
ments. Tools required for installation include 7/8”
(22mm) wrench or socket, 5/16” (8mm) allen wrench
and 10 mm wrench for PFQ only.
Recommended Torques:
Main Contacts: 30 ft-lb. (40 N-m)
Aux/Pilot Contacts: 15 in-lb (1.80 N-m).
general Notes & Precautions
1.
To prevent short circuiting the heat shrink
sleeves provided must be used over lugs and
terminals after wiring.
2. The PF and PFQ inlets and receptacles and
handles are symmetrical and thus they can be
mounted in any of four positions provided that
the locking cam on the receptacle remains easily
accessible.
3. Lugs are not included with devices unless ordered.
WIRINg INSTRUCTIONS
The cable sheath should extend at least 2 in. into
handle or junction box.
For Plug or Connector with Angled handle
or Receptacle on Box or Inlet on Box
• Use straight type compression lugs with 9/16”
or 5/8” hole.
• Run the neutral & ground wires above the phases.
• Apply heat shrink over lugs at terminals.
For Plug or Connector with Straight handle
• Use 90° lugs with 9/16” or 5/8” hole. Arrange
the 90° lugs to minimize the possibility of lugs
touching
• Run the neutral & ground wires above the phases.
• Apply heat shrink over lugs at terminals.
NOTICE: Lugs crimped on the conductors must be
bolted on the terminals with the supplied M14 screws
and washers. In order not to transmit this torque to
the molding, contact bodies should be held with a
suitable wrench when tightening the M14 screw.
The phase contacts are lower to allow the passage
of the ground and neutral above the phases.
ASSEMBLY
Angled handle to Inlet or Receptacle Assembly
1. Attach inlet or receptacle to handle body then
open cover on handle.
2. Connect the conductors to the terminals as
described previously in ‘wiring instructions.’
3. Attach handle cover using a 8mm allen tool and
6 screws supplied.
4. Compress grease coated cable gland by tightening
hub. NOTICE: The recommended torque to
achieve IP 67 is 150 to 280 ft-lb (200-400 N-m),
depending on cable jacket material and diameter.
5. Then tighten the cable clamps.
Junction Box to Inlet or Receptacle Assembly
1. Attach junction box to conduit. Attach cover to
junction box using bolts provided.
2. Connect conductors to terminals as described
previously in ‘wiring instructions.’
3. Mount receptacle or inlet to junction box cover
using bolts provided.
Auxiliary/Pilot Contacts
In order to prevent disconnection under load
electrical interlocking is required. Failure to do
so could result in death or serious injury.
Typical PF/PFQ Control Circuit
PF: The four pilot/auxiliary terminals are numbered
1 to 4 and color coded. Conductors must be stripped
by 0.5 in (12 mm) and fully inserted into their respec-
tive spring-assisted, tunnel type terminals. Tighten ter-
minal screws until hand tight with a 4 mm flat screw-
driver. Recommended torque is 13 in-lb (1.5 N-m).
Terminals will accept flexible conductors up to 10
AWG (6 mm
2
).
Table 2 - Wiring Terminal Capacity
Main Contacts Aux. Contacts
Device Minimum Maximum Maximum
PFQ - 300A 4/0 AWG 350 MCM 10 AWG
PF - 300A 250 MCM 600 MCM 10 AWG
PF - 400A 250 MCM 600 MCM 10 AWG
PF - 600A 250 MCM 600 MCM 10 AWG
FEMALE PILOT
CONTACTS
MALE PILOT
CONTACTS
PILOT CIRCUIT
C
B
A
PF/PFQ
LOAD
TO
LINE
SWITCH ETC.
POWER
COIL
PILOT CIRCUIT
PHASE
RECEPTACLE/
INLET/PLUG
PF/PFQ
C
B
A
CONNECTOR
CONTACTOR
OR
BREAKER WITH
UNDER VOLTAGE
TRIP
JUMPER 2 PILOT
CONTACTS TO
COMPLETE CIRCUIT
NOTE:
ROTATE RECEPTACLE LOCKING
CAM TO ENGAGE PILOTS
Table 1 - Auxiliary Contact Ratings
Device 120vAC 240vAC 480vAC 600vAC
PFQ300 7A 5A 2A* 2A*
PF series 10A* 10A* 10A* 10A*
* Rating is not UL or CSA listed.
PF/PFQ
OPERATING INSTRUCTIONS
Meltric Corporation
/ 4640 Ironwood Drive Franklin, WI 53132
Tel. : 800 433 7642 / Fax : 414 817 6161 / e-mail : [email protected]
INSPF_PFQ D
A manufacturer of products using Marechal technology
meltric
.com
PFQ: Eight pilot/auxiliary contacts are prewired and
identified. Pilots are marked P1 and P2, whereas
auxiliary contacts are numbered 3 to 8. Conductors
provided have a cross-section of 14 AWG (1.5 mm
2
).
Mechanical Locking: PF Series
The cam has two positions:
Position 1: Unlocked, auxiliary/pilot contacts opened.
Position 2: Locked, auxiliary/pilot contacts closed.
The plug is live and can not be removed.
Mechanical Locking: PFQ Series
The cam on the receptacle has three positions:
Position 1: Unlocked, auxiliary and pilot contacts
opened. The cover or plug can be removed.
Position 2: Locked, pilot contacts opened. The
cover or plug can not be removed but pilot
contacts remain open.
Position 3: Locked, auxiliary and pilot contacts
closed. The plug is live and can not be removed.
Cam can be locked out in any of the three positions.
OPERATION
To ensure safe and reliable operation Meltric
plugs and receptacles must be used in
accordance with their assigned ratings.
They can only be used in conjunction with mating
receptacles or plugs manufactured by Meltric or
another licensed producer of products bearing the
Marechal
technology trademark.
Meltric plugs and receptacles are designed with
different keying arrangements, so that only plugs and
receptacles with compatible contact configurations
and electrical ratings will mate with each other.
Connection
1. Insert the plug into the receptacle. This unlocks
the safety shutter on the receptacle and allows
it to rotate.
2. Rotate plug approximately 30° clockwise to
engage the phase contacts and to make the
unit watertight. Turn the cam/mechanical lock
to secure the receptacle and engage the pilot
contacts which energize the circuit.
Disconnection
1. Turn the cam/mechanical lock to disengage the
pilot contacts and deenergize the circuit.
2. Twist plug 30° counterclockwise to disengage
the phase contacts. Withdraw plug.
AChIEvINg RATED WATERTIghTNESS
NOTICE: Proper steps must be taken to maintain
water tightness at NPT fittings on the plug handles or
at the junction box. The use of a sealer tape is
recommended.
IP 66/67 rated ingress protection applies to the
device when the plug and receptacle are fully mated.
When not in use the plug/inlet or connector/receptacle
can be kept watertight by utilizing the protective cap.
Caps are fully engaged when inserted into
receptacle/inlet, rotated 30° clockwise and
secured in place with the locking cam.
Using the correct bushing and compression washer
size is important. The bushing must have as close
a size as possible to the outer cable diameter. The
portion of the cable that passes through the bushing
must be as circular as possible to maintain ingress
protection.
MAINTENANCE
Before inspecting, repairing, or
maintaining Meltric products,
disconnect electrical power to the receptacle to
eliminate the risk of electrical shock.
Meltric products require little ongoing maintenance.
However it is good practice to periodically perform
the following general inspections:
• Check the mounting screws for tightness.
• Verify the weight of the cable is supported by
the strain relief mechanism and not by the
terminal connections.
• Check the IP gaskets for wear and resiliency.
Replace as required.
• Verify the electrical continuity of the ground circuit.
• Check the contact surfaces for cleanliness.
Deposits of dust or similar foreign materials can be
rubbed off the contacts with a clean cloth. Sprays
should not be used, as they tend to collect dirt. If
any significant pitting of the contacts or other serious
damage is observed they should be replaced.
MANUFACTURER’S RESPONSIBILITY
Meltric’s responsibility is strictly limited to the repair
or replacement of any product that does not conform
to the warranty specified in the purchase contract.
Meltric shall not be liable for any penalties or conse-
quential damages associated with the loss of produc-
tion, work, profit or any financial loss incurred by the
customer.
Meltric Corporation shall not be held liable when its
products are used in conjunction with products not
bearing the technology trademark. The use
of Meltric products in conjunction with mating devices
that are not marked with the technology
trademark shall void all warranties on the product.
Meltric Corporation is an ISO 9001 certified company.
Its products are designed, manufactured and rated
in accordance with applicable UL, CSA and IEC
standards. Meltric is also a member of BECMA, the
international Butt-contact Electrical Connectors
Manufacturers’ Association. Like all members,
Meltric additionally designs and manufactures its
products in accordance with BECMA standards
established to ensure intermatablility with similarly
rated products manufactured by other members.
1
2
1
2
Position 1 Position 2 Postion 3
INSPF_PFQ D
WARNING
WARNING