Flex (sam), 45 & 60 mil thick reinforced tpo sheet – Flex TPO Self Adhered Reinforced Membrane User Manual
Page 3
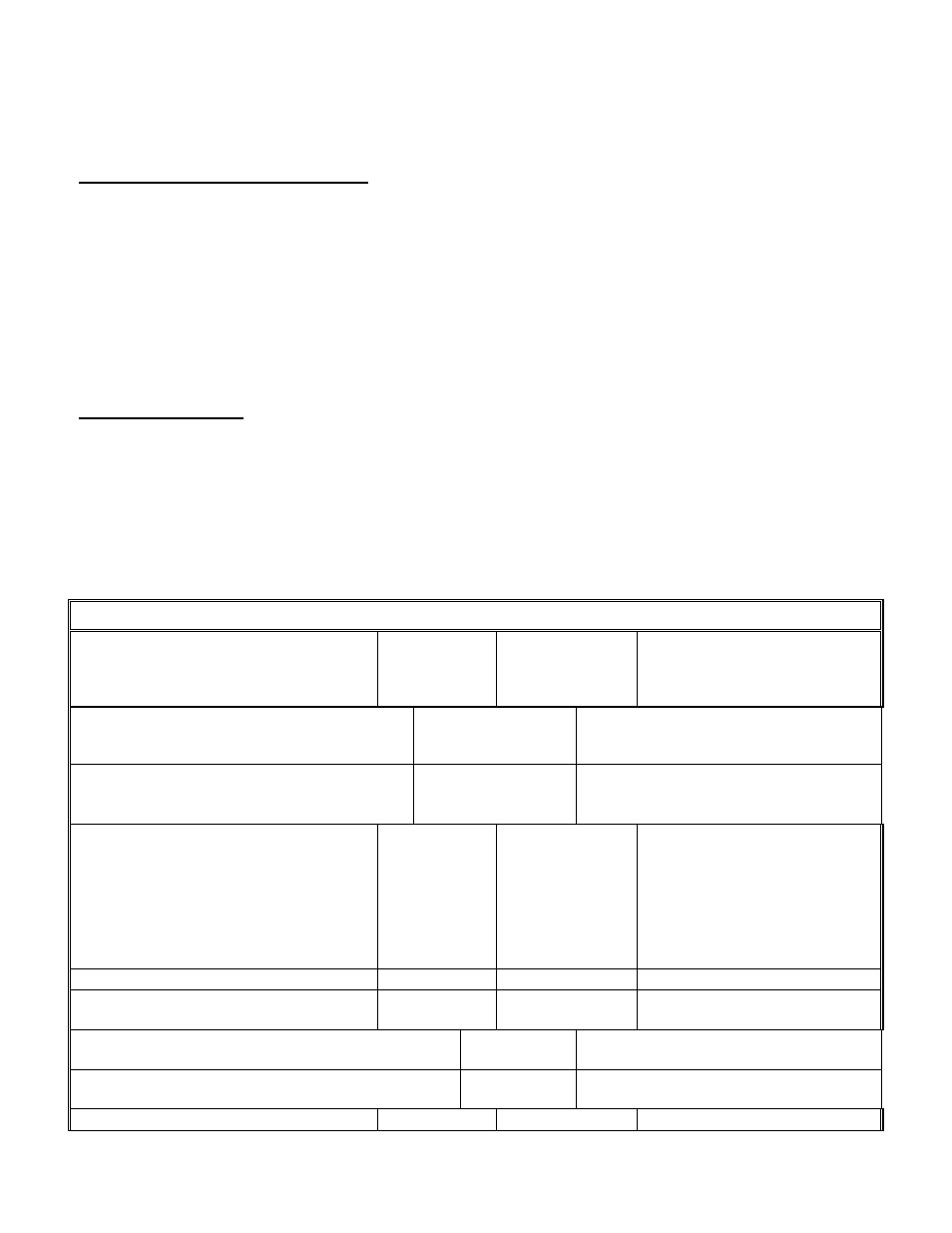
3
membrane. This will help eliminate creases and bubbles that cannot be removed after the sheet is
in place.
3. Roll the Flex (SAM) TPO Membrane with a segmented roller to ensure full contact with the
substrate.
4. Fold back the remaining half of the sheet and repeat the above process.
HEAT WELDING PROCEDURES:
1. Refer to the Flex Adhered Application specification for typical heat welding procedures.
2. The membrane has an uncoated edge on one side along the length of the sheet for membrane
welding. Adjoining membrane sheets are overlapped lengthwise a minimum of 2 in. to provide
for a minimum 1-1/2 in. wide heat weld. It is recommended that all splices be shingled to avoid
bucking of water.
3. An uncoated edge is not provided at the ends of the rolls. Adjoining membrane sheets must be
butted together and overlaid with 6 in. wide Flex Reinforced Membrane, hot air welded along all
edges. Seal all membrane edges (where scrim reinforcement is exposed) with Cut-Edge Sealant.
WALL FLASHING:
1. Walls may be flashed using standard TPO membrane with Flex Bonding Adhesive or with (SAM)
TPO (primer must be utilized on all vertical surfaces).
Contact your Flex Representative for the specific design requirements and installation procedures for this
system.
FLEX (SAM)
45 & 60 MIL THICK REINFORCED TPO SHEET
BASIC PROPERTIES AND CHARACTERISTICS
Physical Property
Test
Method
Property Of
Unaged Sheet
Property After ASTM
D573 aging
1
28 days @ 240 °F
Nominal thickness with adhesive, in. (mm)
45-mil
(adhesive nominal thickness is 0.010)
60-mil
(adhesive nominal thickness is 0.010)
ASTM D751
0.055 (1.40)
0.070 (1.78)
Thickness over scrim, in. (mm)
45-mil
60-mil
ASTM D6878
Optical Method
(avg. of 3 areas)
typical
0.018 (0.457) ± 10%
0.024 (0.610) ± 10%
Breaking strength, lbf (kN)
ASTM D751
Grab Method
225 (1.0) min.
45-mil
320 (1.4) typical
45-mil
250 (1.1) min.
60-mil
360 (1.6) typical
60-mil
225 (1.0) min. 45-mil
320 (1.4) typical 45-mil
250 (1.1) min. 60-mil
360 (1.6) typical 60-mil
Elongation at break of fabric, %
ASTM D751
25 typical
25 typical
Tearing strength, lbf (N) 8 by 8 in. specimen
ASTM D751
B Tongue Tear
55 (245) min.
130 (578) typical
55 (245) min.
130 (578) typical
Brittleness point, °F (°C)
ASTM D2137
- 40 (- 40) max.
- 50 (- 46) typical
Linear Dimensional Change (shrinkage), %
After 6 hours at 158ºF (70 ºC)
ASTM D1204
+/- 0.5 max.
- 0.2 typical
Ozone resistance, 100 pphm, 168 hours
ASTM D1149
No cracks
No cracks