Gradall 534D-10 Service Manual User Manual
Page 254
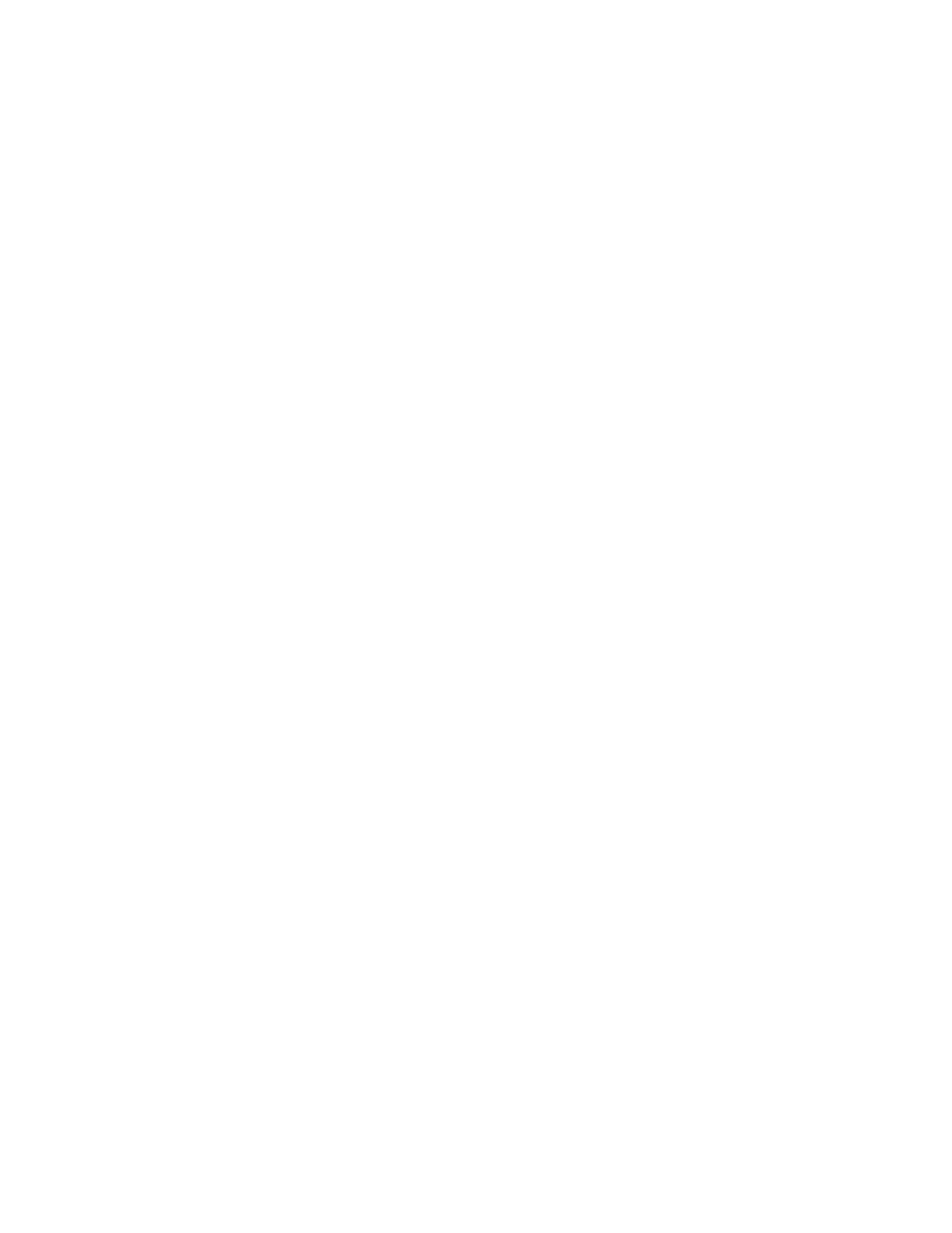
ASSEMBLY OF POWER WHEEL
STEP 1
Press new bearing cups (7 & 10) in each side of the hub (9). It is recommended that bearing
cups (7 & 10) and cones (6 & 11) be replaced in sets.
STEP 2
Assemble bearing cone (6) into cup (7) at seal end of hub (9) and press a new seal (5) into hub
(9). Install boot seal (4) on hub (9) if unit is so equipped.
STEP 3
Position spindle (3) upright on bench. Lubricate lips of seals (4) and (5) and lower hub (9) onto
spindle (3). Hub (9) shouid be centered as it is lowered over spindle (3) to prevent seal damage.
STEP 4
Assemble bearing cone (11) over spindle end. Press bearing cone (11) over spindle bearing
journal using press and cylindrical bearing tool AG08404B. Press bearing cone (11) down until
roller just touches cup (10). (OPTIONAL: Use hammer and bearing tool AG08404B to install cup
(11) over spindle (3). Take care when using this method to avoid pressing cone (11) too far. As
in other method, rollers should just touch cup (10)).
STEP 5
Install thrust washer (12) and bearing nut (14). DO NOT install lockwasher (13) at this time.
STEP 6
Place rolling torque tool AG08771C over spindle (3) and bolt or pin to hub (9).STEP 7
Check initial rolling torque by installing an inch-lb. torque wrench on center nut of rolling torque
tool and turning hub (9) slowly and steadily with the torque wrench. Note mean torque. An initial
bearing rolling torque of greater than 52 in-lbs. means that the cone (11) was pressed on too
tightly in step 4. In this case, back off bearing cone (11) by pressing spindle (3) out of cone (11)
until initial preload is relieved.
STEP 8
Torque bearing nut (14) with bearing nut wrench AG07366B until a bearing rolling torque of 44-52
in-lbs., with a boot seal installed, or 4048 in-lbs., without a boot seal, is reached. This may
require several trials of pressing the cone (11) by torqueing the nut (14) and then checking the
rolling torque. Rotate hub (9) by hand as nut is being tightened in order to seat bearings. NOTE:
Up to 250 ft-lbs. of torque may have to be applied to bearing nut (14) in order to press cone (11)
into position.
STEP 9
Remove bearing nut (14) and install lockwasher (13). Install nut (14).
STEP 10
Re-torque bearing nut (14) to 65-75 ft-lbs.
STEP 11
Secure bearing nut (14) by bending a lockwasher (13) tab into one of four bearing nut slots. If no
tab aligns with a slot, the nut may be tightened until one of the slots aligns with a lock washer tab.
STEP 12
Assemble a washer (16), spring (17), a second washer (16), and a retaining ring (15) in the middle
grooves of input shaft (2). Install a second retaining ring (15) in groove near small end of input
shaft (2).
STEP 13
Assemble the splined end of the input shaft (2) down into spindle (3).
STEP 14
Assemble the secondary carrier assembly (19) to spindle (3) at splines.
STEP 15
Clean mating surfaces and apply a bead of silicone sealant to face of hub (9) that mates with ring
gear (18). (See instructions on sealant package). Assemble ring gear (18) to hub (9) being
careful to align bolt holes.
STEP 16
Assemble the primary carrier assembly (20) into the ring gear (18). It will be necessary to rotate
carrier to align secondary sun gear (part of primary carrier assembly (20)) with planet gear teeth in
secondary carrier assembly (19). Assemble primary sun gear (21) over input shaft (2). Rotate
primary sun gear (21) to align input shaft (2) to gear splines and gear teeth in primary carrier
assembly (20).
STEP 17
Lubricate O-ring (24) and assemble in groove inside cover hole, push disengage plunger (23) into
cover (25) with pointed end facing inside of unit.
3