Liebherr MK 88 User Manual
Page 5
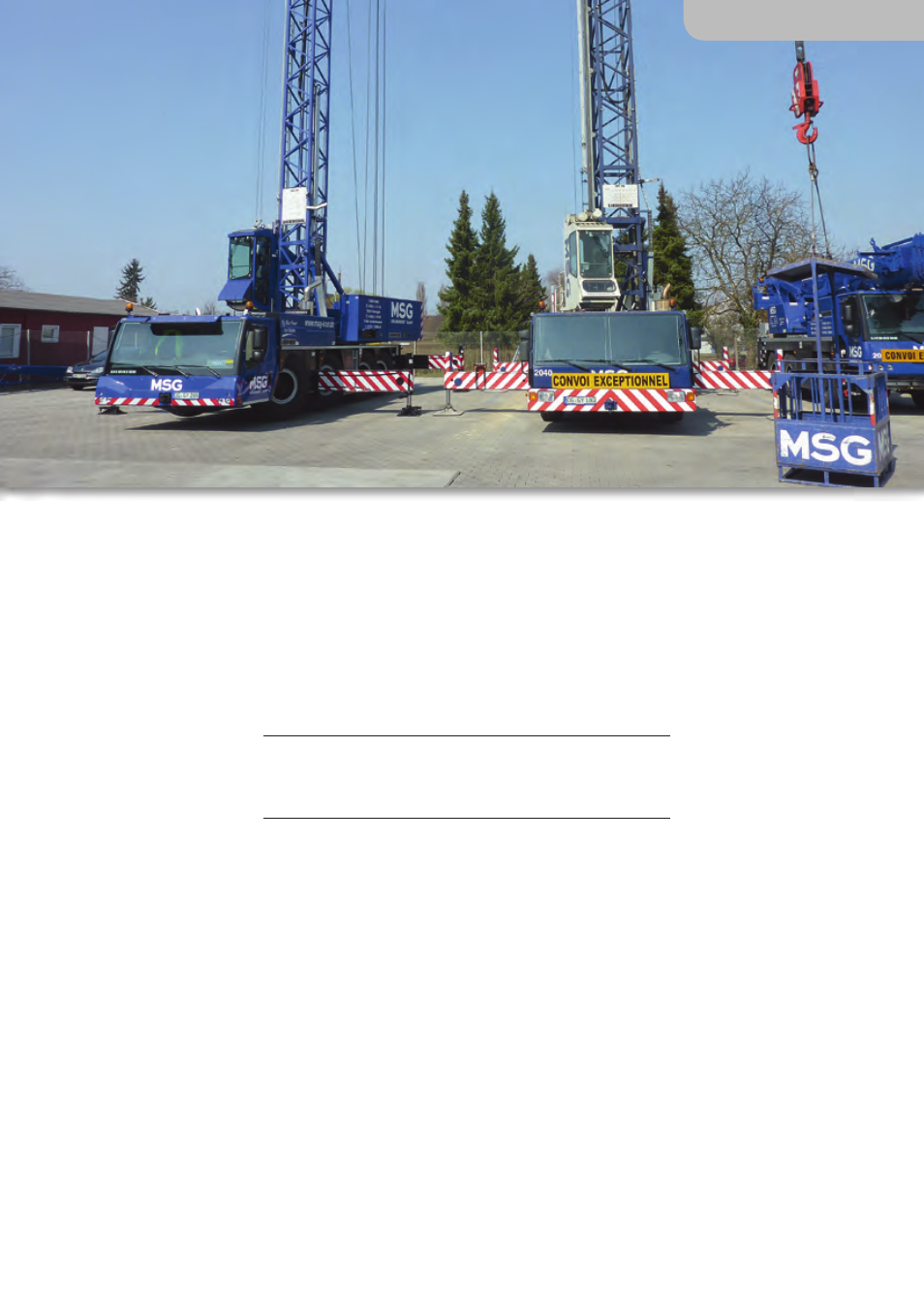
In Aktion
KM Nr. 83 | 2012
Kranmagazin
“Smallest turning radius”,
“Crawler gear”, “Reduced
swing-out” and “Independent
rear-axle steering”.
On the other hand, with
the MK 80 both front axles
are steered and the rear axle
is rigid during road travel.
All-wheel drive is possible
with building site operation
and crawler gear is achiev-
able with the MK 80. In other
words, the MK 80 offers a
high degree of mobility and
manoeuvrability, but not in
such a versatile or comfort-
able manner as its successor.
After the test drive both
cranes returned to MSG’s
yard, where both cranes were
to be erected. A start was
made with the MK 80, and
the design differences be-
tween this crane and its suc-
cessor became obvious very
quickly.
To summarize: with the
MK 88, cables and winches
are used to erect the crane –
in other words the whole
process is carried out with
wire ropes – but with the
MK 80 much of the work is
done by a hydraulic cylinder
in combination with tie and
erection bars.
And while with the MK 88
the undercarriage engine is
needed only for the outrig-
gers and the superstructure
is then used for the erection
process, with the MK 80 be-
cause the central hydraulic
cylinder is required for the
erection process, the under-
carriage engine has to run
for most of the time. This hy-
draulic cylinder and under-
carriage engine are also used
when the MK 80 jib is to be
positioned at the 30° angle.
With the MK 88 the luffed jib
positions of 15°, 30° and 45°
are implemented by adjusting
the guying winch.
The MK 80 was ready for
operation in 24 minutes – in-
cluding raising it on the out-
riggers. With the MK 88, the
entire process took 14 min-
utes and 40 seconds. How-
ever, you can probably reduce
this by the four to five min-
utes that was needed to ex-
plain some of the differences
to the KM editor.
For example, that fact that
if the MK 80 is to be used at
just half hook height, some
manual work is needed before
the start of the actual erection
process – such as rearranging
certain bolts – which is un-
necessary with the MK 88.
Generally, the MK 80 needs
more manual work, since as
opposed to its successor it
does not have an automatic
boom slewing facility, for ex-
ample. For the crane driver
that means once the tower/jib
unit is erected: he has to pick
up a rod and slew the jib man-
ually. In addition, with the
MK 80 the jib interlock must
be released manually.
Another
differentiating
feature is that, as opposed to
the MK 88, with the MK 80
the hook is not stored in the
lattice mast jib but hangs
down outside and therefore
has to be released manually
for deployment and locked
for driving. And when the
cranes have been erected and
the MK 80 and MK 88 cabs
slide down on the towers, the
MK 88 cab automatically has
its full legroom. However,
the MK 80 driver has to re-
lease the locks outside the cab
manually before being able to
enjoy the full working space.
Although with the MK 88
the complete tower is extend-
ed before the jib heel section
is hoisted, assembly is faster
than with the MK 80, which
unfolds the jib while the tow-
er is being extended.
“The clear advantage with
the MK 88 is that for the erec-
tion process it doesn’t need
the MK 80’s hydraulic cyl-
inder which operates much
slower. The MK 88 also of-
fers three different assembly
modes, so that we can erect it
in many different deployment
and space situations”.
As mentioned at the start,
the MK 88 also allows three
different jib luffed positions,
apart from 15° and 30° also
a 45° angle. The MK 80, on
the other hand, offers only a
30° luffed position. “We work
mainly with the 15° and 30°
luffed positions,” says Felix
Bildstein. “But we have had
jobs that would have not
been possible without the
45° luffed position. I remem-
ber we had a job on a church
that we could not have done
at all with the MK 80 because
we couldn’t have reached the
necessary hook height with
it,” adds Martin Hartmann.
During driving and operation it‘s clear that the MK 88 is the more modern crane.
In general, more manual work is needed to erect
the MK 80.