Technical data, Engine, Hydraulic system – Liebherr LRB 125 XL User Manual
Page 6: Swing, Auxiliary winch, Crawlers, Control, Noise emission, Rope crowd system
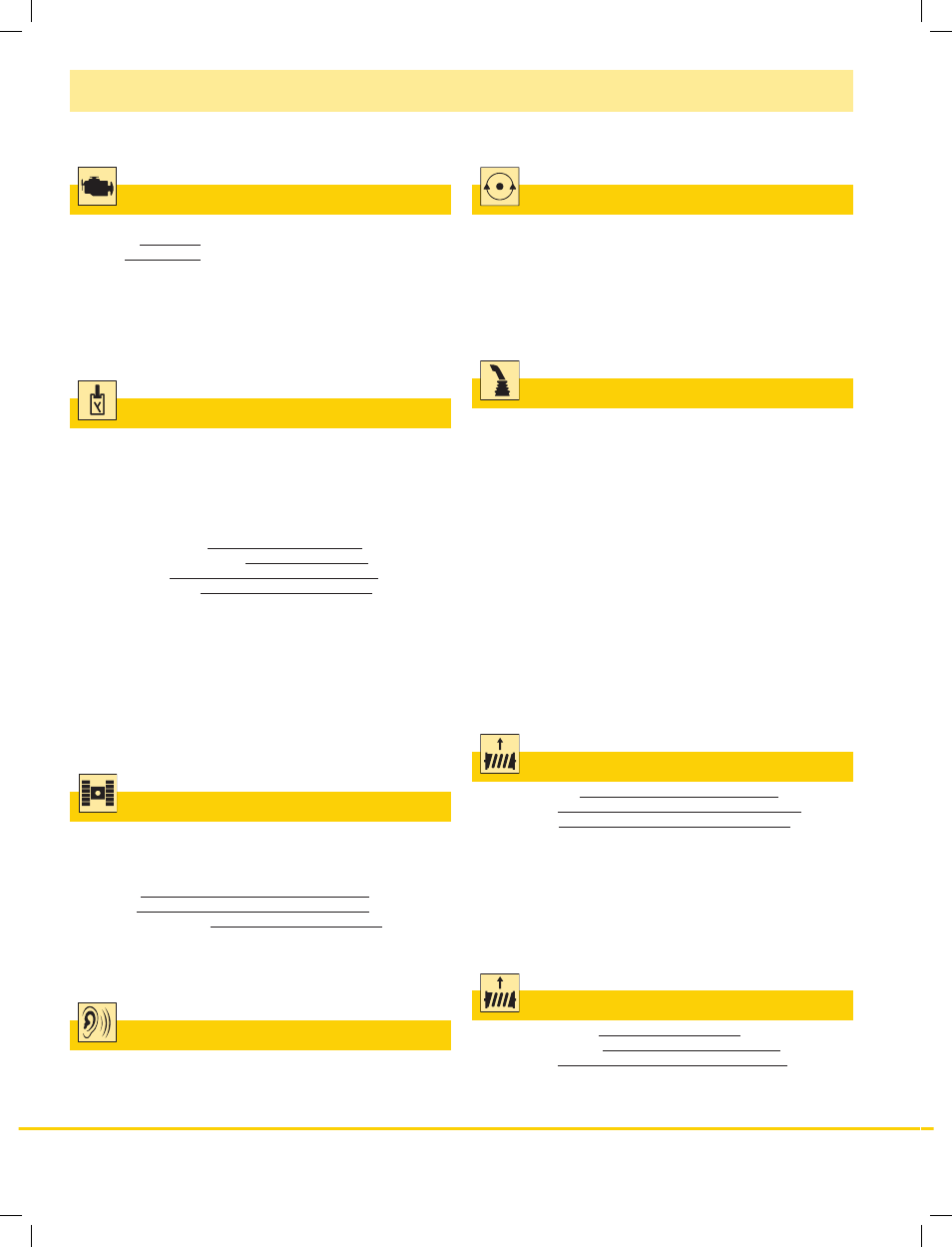
6
LRB 125
Technical data
Engine
Power rating according to ISO 9249, 505 kW (677 hp) at 1900 rpm
Engine type
Liebherr D 9508 A7 SCR
Fuel tank
264 gal capacity with continuous level
indicator and reserve warning
Engine complies with NRMM exhaust certification EPA/CARB Tier 4i
or 97/68 EC Stage III B.
Hydraulic system
The main pumps are operated by a distributor gearbox. Axial piston
displacement pumps work in open circuits supplying oil only when
needed (flow control on demand).
The hydraulic pressure peaks are absorbed by the integrated
automatic pressure compensation, which relieves the pump and
saves fuel.
Pumps for working tools
2x 106 gal/min
Separate pumps for kinematics
2x 50 gal/min
Hydraulic oil tank
225 gal
Max. working pressure
5076 bar
No auxiliary power packs are required as application specific
hydraulics supply power to all components.
The cleaning of the hydraulic oils occurs via an electronically
monitored pressure and return filter.
Any clogging is shown on the display in the cab.
The use of synthetic environmentally friendly oil is also possible.
Swing
Consists of single row ballbearing, fixed axial piston hydraulic motor,
spring loaded and hydraulically released multi–disc holding brake,
planetary gearbox and pinion.
Swing speed from 0 – 3.3 rpm is continuously variable.
Auxiliary winch
Line pull (effective)
11,240 lbf
Rope diameter
17 mm
Drum diameter
16.5 inch
The winch is noted for compact, easily mounted design.
Propulsion is via a maintenance-free planetary gearbox in oil bath.
Load support by the hydraulic system; additional safety factor by a
spring–loaded, multi–disc holding brake.
Crawlers
Propulsion through axial piston motor, hydraulically released spring
loaded multi–disc brake, maintenance free crawler tracks, hydraulic
chain tensioning device.
Drive speed
0 – 1.37 mph
Track force
103,190 lbf
Width of 3-web grousers
27.55 inch
Control
The control system – developed and manufactured by Liebherr – is
designed to withstand extreme temperatures and the many heavy–
duty construction tasks for which this machine has been designed.
Complete machine operating data are displayed on a high resolution
monitor screen. A GSM/GPRS telematics module allows for remote
inquiry of machine data and operational conditions. To ensure clarity
of the information on display, different levels of data are shown in
enlarged lettering and symbols.
Control and monitoring of the sensors are also handled by this high
technology system. Error indications are automatically displayed on
the monitor in clear text. The machine is equipped with proportional
control for all movements, which can be carried out simultaneously.
Two joysticks are required for operation. Pedal control can be
changed to hand control.
Options :
PDE
®
: Process data recording
Noise emission
Noise emissions correspond with 2000/14/EC directive on noise
emission by equipment used outdoors.
Rope crowd system
Crowd force push/pull
33,720/44,960 lbf
Line pull (nominal load)
22,480 lbf
Rope diameter
18/20 mm
The ropes are actuated by a powerful hydraulic cylinder.