Duff-Norton EM1010-100 (TMD02) User Manual
Page 5
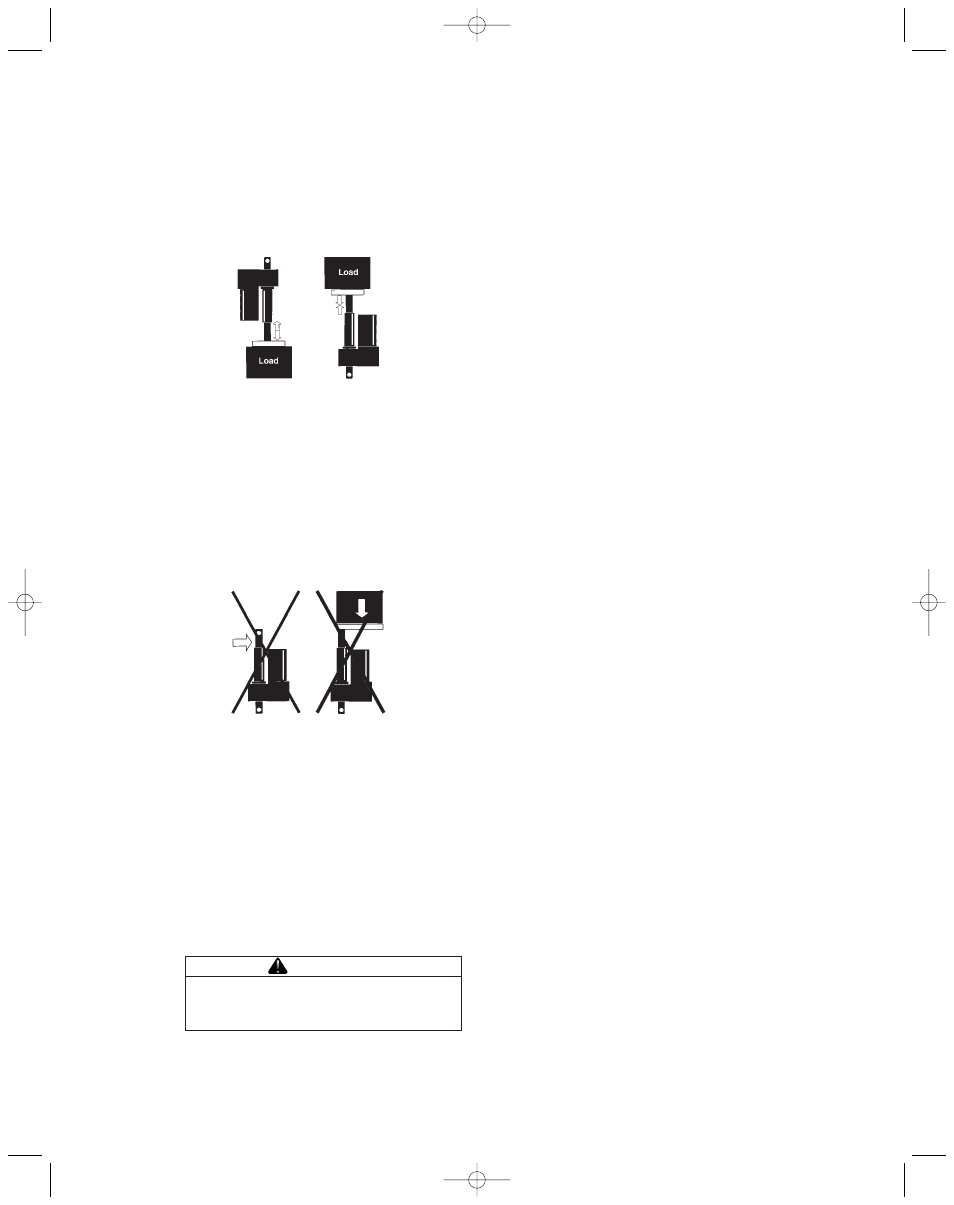
INSTALLATION
2-1 Direction of Loading
Duff-Norton electromechanical actuators
can be used in tension, compression, or
combination tension/compression applica-
tions. Examples are as shown below.
It is important to mount the actuator so that
side loading or eccentric loading are avoid-
ed. To optimize the ----- performance and
life of the actuator, it should be mounted so
that the load is applied along the longitudi-
nal axis of the translating tube, with freely
pivoting clevis attachments. Examples of
improper loading are shown below.
2-1 Limit Switches
These actuators do not have clutches or
other provision for accommodating end of
stroke jamming. Thus, electrical limit
switches must be provided. Actuators are
available from the factory with or without
magnetically activated limit switches are not
utilized, external limit switches must be pro-
vided by the installer.
2-1 Wiring Connections
Actuators with factory installed Limit Switches
1. Either 12 or 24 volts DC, to match the voltage rat-
ing of the actuator, should be connected to the two
terminals of the relay board which do not have other
connections (see wiring diagram). Reverse DC polar-
ity to reverse actuator.
2. Actuator speed control by operation on reduced
voltage should not be used, as this will prevent prop-
er operation of the control relay.
Actuators with limit switches by installer
1. Power supply to the actuator should be protected
by a fuse with standard blow characteristics. Proper
fuse sizing is 8 amps for 12 volt units and 5 amps for
24 volt units.
2. Power from the control circuit, which should
include limit switches and appropriate controls,
should be connected directly to motor terminals.
2-4 Limit Switch Adjustment
Actuators with factory installed switches are shipped
with switches adjusted for maximum retraction and
travel. Attempting to increase stroke in either direc-
tion invites actuator jamming which will result in
irreparable damage. Stroke may be reduced on
either end of travel by loosening screws attaching
switches, sliding along tube, and resecuring.
OPERATION
3-1 Operating Conditions
The actuator should be operated within its ratings for
load, duty, and temperature (see 1-3. Specifications).
Rapid jogging or plug-reversals should be avoided.
Stalling the actuator by overloading or by improper
limit switch setting will result in rapid failure.
INSPECTION AND MAINTENANCE
4-1 Safety Note
Disconnect power from actuator before making
repairs.
4-2 Inspection
Inspect periodically for loose or damaged parts,
including clevis attachment pins.
4-3 Maintenance
No periodic maintenance is required or prescribed.
Replacement parts are not available.
4-4 Lubrication
The actuator is lubricated at the factory.
Relubrication is not generally required.
IMPROPER SIDE LOADING
PROPER LOADING
Tension
Compression
CAUTION
Be sure power connections are not live
before connecting to actuator.
EM-1010-100_0706 7/31/07 2:40 PM Page 4