Instruction manual ni-281e – WIKA PCA_HP User Manual
Page 4
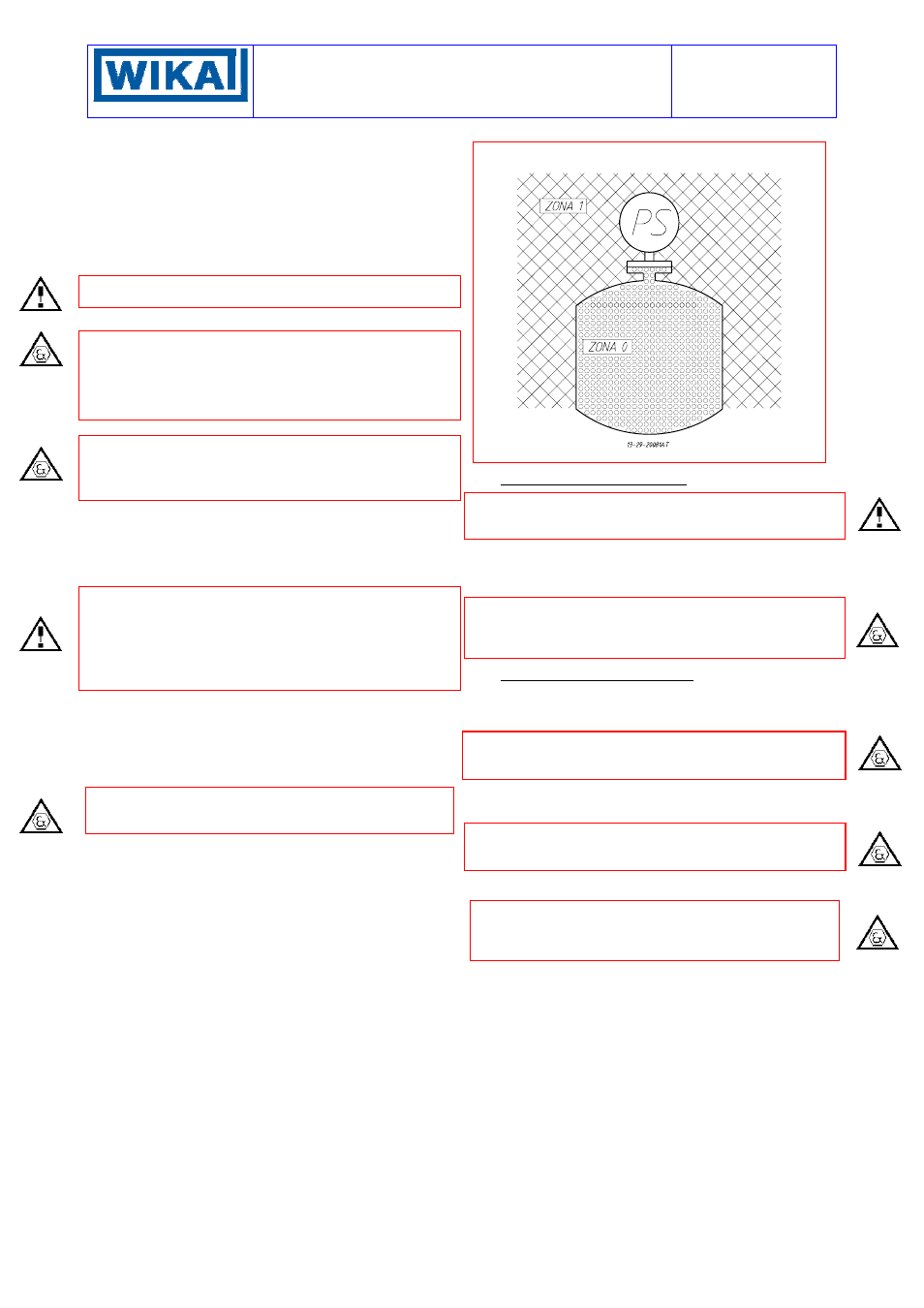
INSTRUCTION MANUAL
NI-281E
Rev. 5 11/02
valve is closed with a plug to prevent the outlet of the process
fluid caused by the incorrect use of said valve.
Mount a three piece joint onto the threaded attachment of the
instrument to permit the easy mounting or removal of the
instrument itself.
Carry out the connection using a flexible tube in such a way that
the tube itself does not force the instrument attachment due to
variations in temperature.
Ensure that all the pressure connections are airtight. It is
important that there are no leakages in the circuit.
Close the root valve and the relative drain device. Close the
service valve fitted with a safety plug.
7.3 ELECTRICAL CONNECTIONS
It is recommended to carry out the electrical connections
according to the applicable standards. In case of explosionproof
instruments (Series PCA) see also the Standard EN-60079-14. If
the electrical connection is carried out in a protected tube, it shall
be made so that condensate is prevented from entering
instrument enclosure.
The arrangement shown in Fig. 5 or 6 is therefore recommended.
CAUTION:
fittings used for the electrical connection of the
pressure switch Series PCA (explosionproof) shall be certified to
Standards EN 50014 and 50018, and shall guarantee instrument
degree of protection (IP65).
Check that there is no power in the lines.
Remove the cover and carry out the cabling and connections to
the terminal block (see Fig. 2).
Flexible cables with a maximum section of 1,2 mm
2
(16AWG) are
recommended using the pre-insulated thimbles with a maximum
diameter of 2,5 mm supplied with the instrument.
When inserting cables into the enclosure pay attention not to
force the microawitch with cable or tools, otherwise instrument
calibration or even its operation could be compromised. The
microswitch has been factory mounted and positioned in order to
obtain the best performances. Any tampering made on site
without following instructions authorised by the E. CELLA SPA
may result in instrument malfunction.
Ensure that no deposits or wire ends remain inside the case.
Once the connection operations have been completed, replace
the cover and ensure that it is properly sealed and blocked. See
Fig. 3.
7.4
SPECIAL NOTE FOR INSTALLATION OF
CATEGORY 1 / 2 G PRESSURE SWITCHES
Explosionproof pressure switches (Series PCA) can be installed
on processes requiring apparatus of group II category 1 in an
ambient requiring apparatus of group II category 2 (see Fig. 5).
Fig. 5 -
Installation of Group II Cat. 1 / 2 G instruments
8 - PUTTING INTO OPERATION
As the signal transmitted by the instrument is used in a complex
system, it is necessary that the means of putting it into operation
are established by personnel in charge of the plant
.
The instrument comes into operations as soon as the root valve is
opened. Any possible drainage of the connection tubing can be
carried out by removing the safety plug and opening the service
valve with the necessary caution.
In case of explosionproof instruments (Series PCA), initial
inspections are to be carried out according to customer
procedures and at least in accordance with Standard EN-60079-
17.
9 - FUNCTIONAL VERIFICATION
This will be carried out according to the Client’s control
procedures. Series PCS instruments can be verified on the plant if
installed as illustrated in Fig. 6 and 7.
The instruments Series PCA may be checked on site only if
apparatus suitable for explosive atmosphere are used and
provided that the electric line is not energized.
If this is not the case it is necessary to stop operation, dismount
by means of the three piece joints and carry out the verification in
a test room.
CAUTION: do not open the cover of explosionproof pressure
switches (Series PCA) when energized, in explosive
atmospheres.
Verification consists in check the calibration value and possibly
regulating the adjustment bush (see §5).
In case of explosionproof instruments (Series PCA), inspections
of the electrical installation are to be carried out also according to
customer procedures and at least in accordance with Standard
EN-60079-17.