Caution – Goulds Pumps 3409 - IOM User Manual
Page 47
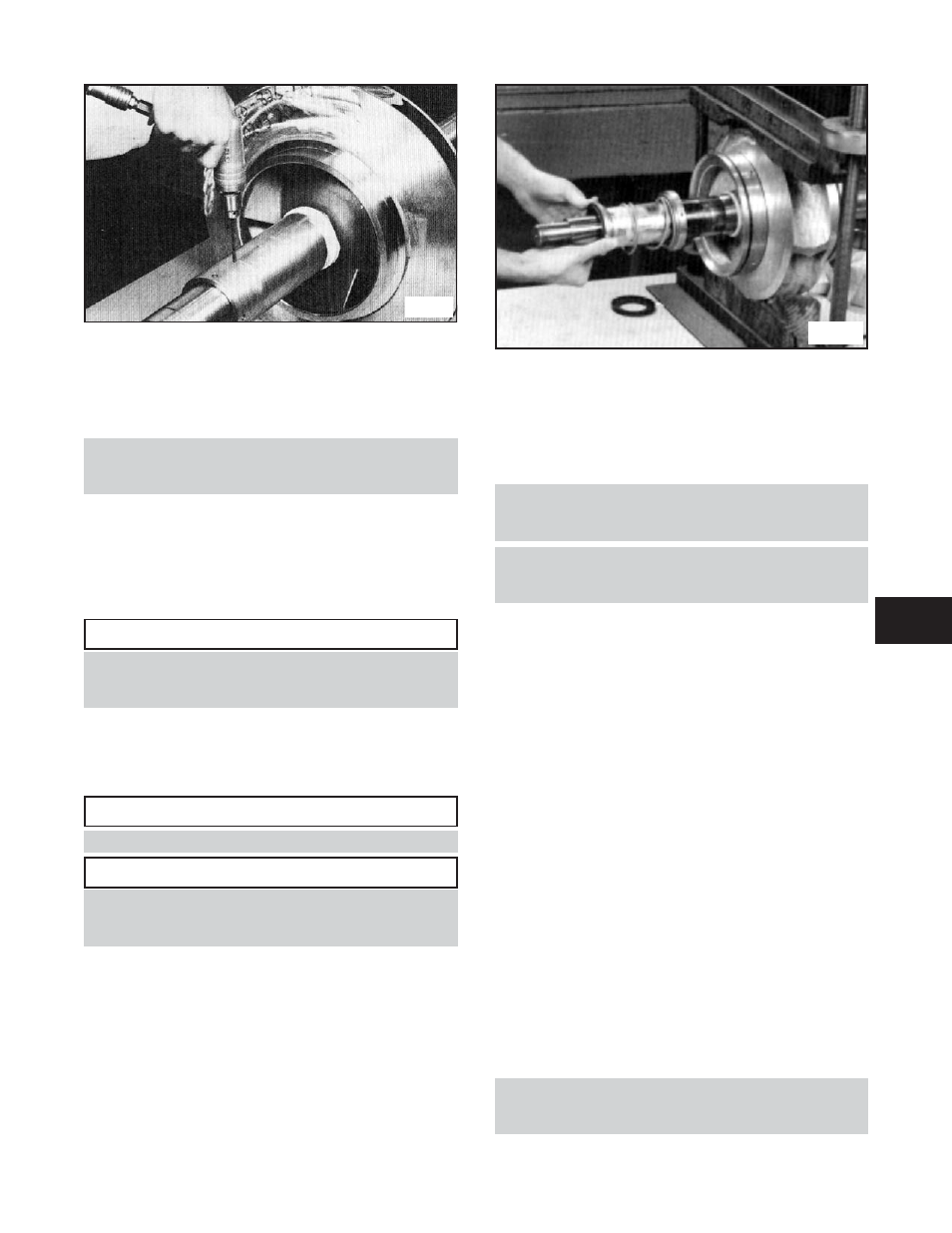
7.
Assemble casing rings (127). (See Adjustable Wear Ring
Section, if required.)
8.
Install stationary seats (383) into the glands (250) with
lapped surface facing outward.
NOTE: Do not scratch or damage seal faces during
assembly. Stationary seat must bottom squarely in
gland.
9.
Apply fine coat of silicon grease or equivalent to shaft
sleeve, and slide seal head assembly (383) over sleeve.
(See Fig. 26) If seal is a John Crane Type 8, set seal to
approximate dimension shown in Fig. 28 and tighten
set screws. Next, install O-rings (412G) onto glands
(250) and install glands on the shaft.
$
CAUTION
Do not use petroleum based products for installing
mechanical seal head as it may attack the rubber
elastomers.
10. Start heating bearings (168 & 410) so that they will be
ready when called for in step 13. Use dry heat from
induction heat lamps or electric furnace, or a 10-15%
soluble oil and water solution.
$
!
CAUTION
Do not exceed 275° F.
$
CAUTION
These are precision, high quality bearings. Exercise
care at all times to keep them clean and free of foreign
matter.
11. Press inboard bearing isolators (333A) in each bearing
cover. Install gaskets (360) on each bearing cover.
12. Slide bearing covers (109 & 119) on the shaft. Install snap
rings (276). Install thrust washer (535) on the outboard
end.
NOTE: For ease of assembly and protection of rubber
parts while sliding rubber parts onto shaft, cover O-ring
groove, keyways, and threads with electrical tape.
NOTE: Inboard bearing cover (119) is approximately 1/4
inch less in width than the outboard bearing cover (109).
This is the only dimensional difference.
13. Press heated bearing (168 & 410) on shaft against snap
ring or thrust washer. Install locknut (136) and lockwasher
(382) on outboard end. Make certain the locknut is secured
and then bend over tab on lockwasher.
PUMPS WITH GREASE LUBRICATION
14. Cool bearings at room temperature and coat with 2 or 3
ounces of a recommended grease.
PUMPS WITH OILLUBRICATION
See Oil Lubricated Bearings Section for installation of oil
lubricated parts.
15. Press outboard bearing isolator (332A) in coupling end
bearing housing.
16. Slide bearing housings (134) over bearings (168 & 410).
17. Assemble bearing cover to bearing housing with two cap
screws (371C).
18. Replace pump coupling half and key (400).
19. Assemble rotating element in lower half casing (100).
Correctly locate casing ring pins (445A) in casing main
joint slot.
NOTE: Sliding inboard bearing housing toward coupling
prior to assembling rotating element in casing will ease
assembly.
3409 IOM 11/04
47
Fig. 25
Fig. 26
6