APTech KT12 User Manual
APTech Relay
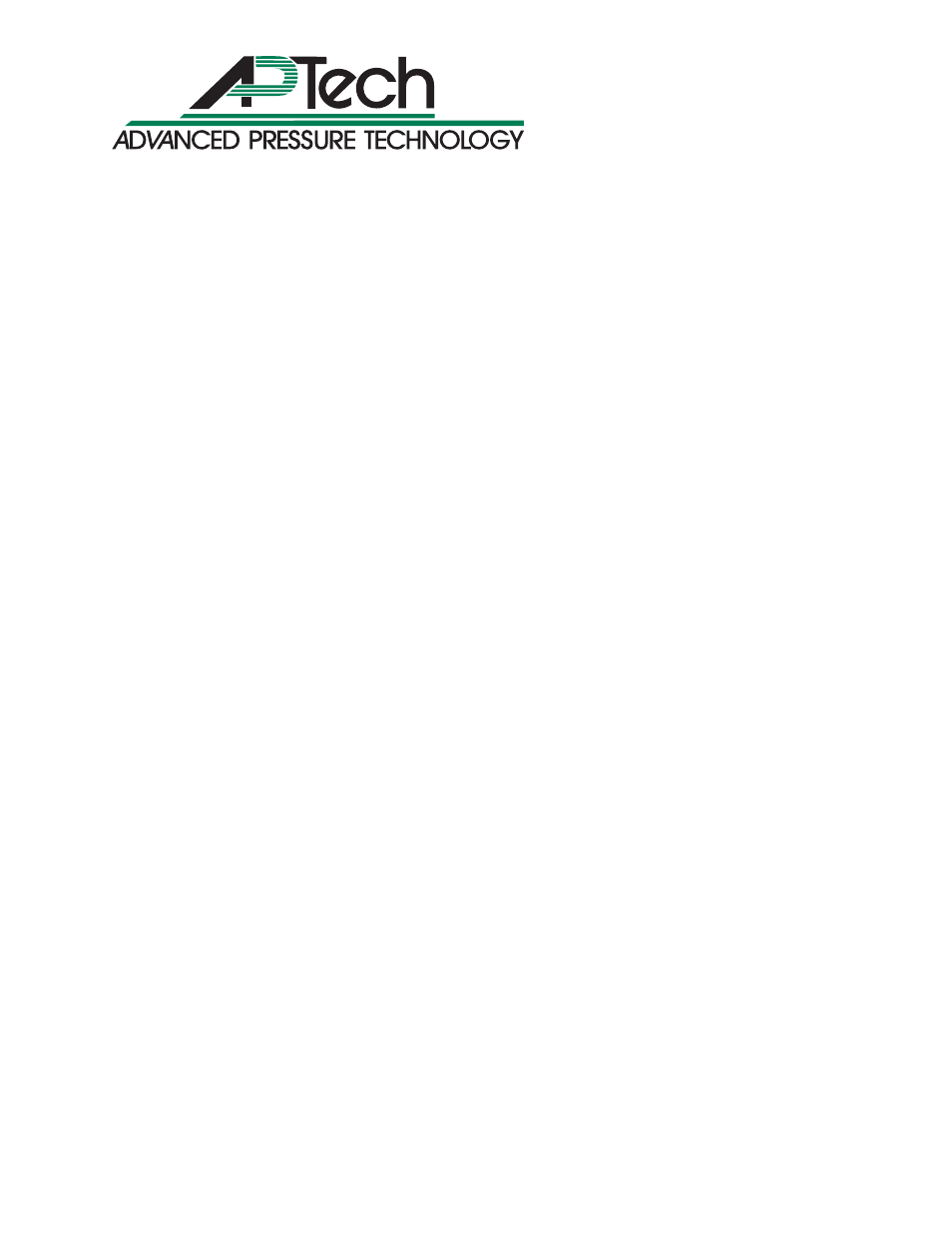
687 Technology Way
Napa, CA 94558
Phone: (707) 259-0102
FAX: (707) 259-0117
www.aptech-online.com
Operation Manual
Piston Sensed Gas Pressure Regulators
(Models KT10, Welded KT10, KT12)
Table of Contents:
A. General information ...................................................................................................................... 1
B. System Design/Product Selection ................................................................................................. 1
C. Installation..................................................................................................................................... 1
D. Manually Adjustable, Non-relieving (non-venting) Regulator Operation .................................... 4
E. Manually Adjustable, Self-relieving (self-venting) Regulator Operation .................................... 5
F.
A. General information
AP Tech pressure regulators are used in gas delivery systems to reduce the source pressure to a
lower delivery (outlet) pressure. This operation manual is applicable to gas pressure regulators that
use a piston to sense the delivery pressure.
Refer to the appropriate catalog data sheet for specific product information. For special options that
are not shown in the data sheet, contact the factory or your local representative for questions on
proper operation.
B. System Design/Product Selection
1.
AP Tech piston sensed gas pressure regulators are not safety accessories per EU Pressure
Equipment Directive 97/23/EC or safety related devices per EU ATEX Directive 94/9/EC. The
EU Pressure Equipment Directive requires the system designer to install a safety accessory (for
example, safety relief valve or burst disc) where the design pressure of the downstream system is
lower than the upstream pressure.
2.
When selecting the pressure regulator model and configuration, verify the following information.
a.
Verify the materials of construction are compatible with the intended process gas.
b.
Verify the pressure and temperature ratings are acceptable for the intended application.
c.
If the regulator is to be equipped with either a supply or delivery pressure gauge, verify that
the pressure gauge range is suitable for the application.
d.
Verify that the flow capability of the regulator is appropriate for the application.
3.
KT10, Welded KT10, and KT12 regulators must be ordered with the non-relieving (non-venting)
option if the process gas they are to be used with is hazardous (flammable, toxic, etc.). The
self-relieving (venting) option on these models vents process gas through the regulator cap
directly into the atmosphere surrounding the regulator, which is undesireable with a hazardous
gas.
4.
Pressure regulators can be used under a large variety of operation conditions. The system
designers shall decide product selection based upon their own analysis and testing to verify
acceptable operation with specific equipment.
C. Installation
1.
Verify the pressure rating is acceptable for the intended application.
2.
If the regulator is equipped with either a supply or delivery pressure gauge, verify that the
pressure gauge range is suitable for the application.
Page 1 of 9
Manual 15000011 Rev. 5
Document Outline
- Table of Contents:
- A. General information
- B. System Design/Product Selection
- 1. AP Tech piston sensed gas pressure regulators are not safety accessories per EU Pressure Equipment Directive 97/23/EC or safety related devices per EU ATEX Directive 94/9/EC. The EU Pressure Equipment Directive requires the system designer to insta...
- 2. When selecting the pressure regulator model and configuration, verify the following information.
- a. Verify the materials of construction are compatible with the intended process gas.
- b. Verify the pressure and temperature ratings are acceptable for the intended application.
- c. If the regulator is to be equipped with either a supply or delivery pressure gauge, verify that the pressure gauge range is suitable for the application.
- d. Verify that the flow capability of the regulator is appropriate for the application.
- 3. KT10, Welded KT10, and KT12 regulators must be ordered with the non-relieving (non-venting) option if the process gas they are to be used with is hazardous (flammable, toxic, etc.). The self-relieving (venting) option on these models vents process ...
- 4. Pressure regulators can be used under a large variety of operation conditions. The system designers shall decide product selection based upon their own analysis and testing to verify acceptable operation with specific equipment.
- C. Installation
- 1. Verify the pressure rating is acceptable for the intended application.
- 2. If the regulator is equipped with either a supply or delivery pressure gauge, verify that the pressure gauge range is suitable for the application.
- 3. Inspect the regulator to determine the flow path through the regulator and how the regulator will need to be installed in the system.
- a. The high pressure (inlet/supply) port(s) is labeled with an “HP” marked on the body near the port. Arrows are sometimes used next to the HP characters to point toward a high pressure port.
- b. The low pressure (outlet/delivery) port(s) is labeled with an “LP” marked on the body near the port. Arrows are sometimes used next to the LP characters to point toward a low pressure port.
- c. Always connect the gas source to the high pressure port. Never connect the gas source to the low pressure port as the regulator can be damaged and leakage can result.
- 4. Install the regulator using the appropriate method described below. For assembly of other type connections, consult connector manufacturer or contact the factory.
- a. For NPT connections, apply PTFE (e.g. Teflon) tape to connector threads and install connector in regulator body wrench tight.
- b. For straight thread o-ring connections (such as MS33649 porting), verify the proper mating fittings and o-rings are being used and install the fittings in the regulator. Tighten according to fitting manufacturer specification.
- c. For metal face seal connectors (Welded KT10), assemble connections per standard practice described by fitting supplier (typically 1/8 turn past fingertight).
- 5. For pneumatically actuated KT10 and KT12 regulators, a separate line will need to be plumbed to provide the pneumatic actuator control pressure. Pressurized inert gas, typically nitrogen gas, or air may be used for actuation. The maximum allowabl...
- 6. If appropriate for the application, secure the regulator body using one of the below methods.
- a. For KT10 and KT12 regulators with NPT or straight thread connections, use the panel mount clamp option to secure the regulator. It may be necessary to remove the regulator wheel to install the regulator through the panel. Refer to Figure 1 to rem...
- b. For Welded KT10 regulators with metal face seal connections, use the mounting holes in the bottom of the body to secure the regulator with 10-32 UNF screws.
- 7. After installation, perform a leak test. A pressure decay leak test is recommended to check for leak integrity of the regulator internal parts and external fitting connections. A bubble leak test may be performed to check for leaks at external fitt...
- D. Manually Adjustable, Non-relieving (non-venting) Regulator Operation
- 1. Perform the following to increase the regulator delivery pressure set point.
- a. Before opening the source valve, verify that the regulator adjustment wheel is turned fully counterclockwise (fully decreased position).
- b. Slowly open the source valve to pressurize the regulator high pressure port.
- c. Rotate the regulator wheel clockwise to increase the delivery pressure to the desired pressure.
- 2. Perform the following to decrease the regulator delivery pressure set point for non-relieving (non-venting) regulators.
- a. Open a downstream valve to initiate a flowing condition.
- b. Rotate the regulator wheel counterclockwise to reduce the delivery pressure below the desired pressure.
- c. Close the downstream valve to stop flow.
- d. Rotate the regulator wheel clockwise to increase the delivery pressure to the desired pressure.
- 3. Perform the following to fully decrease the regulator delivery pressure.
- 1. Perform the following to increase the regulator delivery pressure set point.
- E. Manually Adjustable, Self-relieving (self-venting) Regulator Operation
- 1. Perform the following to increase the regulator delivery pressure set point.
- a. Before opening the source valve, verify that the regulator adjustment wheel is turned fully counterclockwise (fully decreased position).
- b. Slowly open the source valve to pressurize the regulator high pressure port.
- c. Rotate the regulator wheel clockwise to increase the delivery pressure to the desired pressure.
- 2. Perform the following to decrease the regulator delivery pressure set point for self-relieving (self-venting) regulators.
- a. Slowly rotate the regulator wheel counterclockwise to reduce the delivery pressure below the desired pressure. The self-relieving feature will vent the delivery pressure through the regulator bonnet to atmosphere.
- b. Rotate the regulator wheel clockwise to increase the delivery pressure to the desired pressure.
- 3. Perform the following to fully decrease the regulator delivery pressure.
- 4. When necessary perform the following to adjust the vent valve. Refer to Figure 1.
- a. Remove the closure (6) on the top of the regulator adjustment wheel (4).
- b. Rotate the adjustment wheel clockwise to set the delivery pressure to approximately 10% of regulator’s rated maximum outlet pressure or 200 psig whichever is greater, with all valves downstream of the regulator closed.
- c. Use a flat tip screwdriver to turn the vent screw (9) clockwise until gas can be heard venting through the bonnet of the regulator.
- d. Once venting is heard, turn the vent screw counterclockwise until audible gas flow stops plus one half additional turn.
- e. Replace the closure on the top of the adjustment wheel.
- 1. Perform the following to increase the regulator delivery pressure set point.
- F. Preset Regulator Operation
- 1. Perform the following to readjust the regulator delivery pressure set point. Refer to Figure 1
- a. Close the source valve.
- b. Vent outlet to atmospheric pressure. This should vent both source and delivery pressures to atmospheric pressure since the regulator is preset to some set point.
- c. Remove acorn nut (8) from top of stem (2).
- d. Loosen jam nut (7).
- e. Place a 3/8 inch open end wrench on stem flats and rotate stem fully counterclockwise (fully decreased position).
- f. Slowly open the source valve to pressurize the regulator high pressure port to the desired inlet pressure.
- g. Using 3/8 inch wrench on stem flats, turn stem clockwise to increase the delivery pressure to the desired pressure.
- h. Reinstall jam nut and tighten to 100 in-lb against regulator bonnet.
- i. Reinstall acorn nut and tighten to 40 in-lb against jam nut.
- 1. Perform the following to readjust the regulator delivery pressure set point. Refer to Figure 1
- G. Pneumatically Actuated, Non-relieving (non-venting) Regulator Operation
- 1. Perform the following to increase the regulator delivery pressure set point.
- a. Before opening the source valve, verify that the actuation control pressure is at atmospheric pressure.
- b. Slowly open the source valve to pressurize the regulator high pressure port.
- c. Slowly increase the actuation control pressure to increase the delivery pressure to the desired pressure. See Figure 4 and Figure 5 for delivery pressure versus actuation control pressure charts for the pneumatically actuated KT10 and KT12 models.
- 2. Perform the following to decrease the regulator delivery pressure set point for non-relieving (non-venting) regulators.
- 3. Perform the following to fully decrease the regulator.
- 1. Perform the following to increase the regulator delivery pressure set point.