APTech SL 5800 User Manual
A. general information, B. system design/product selection
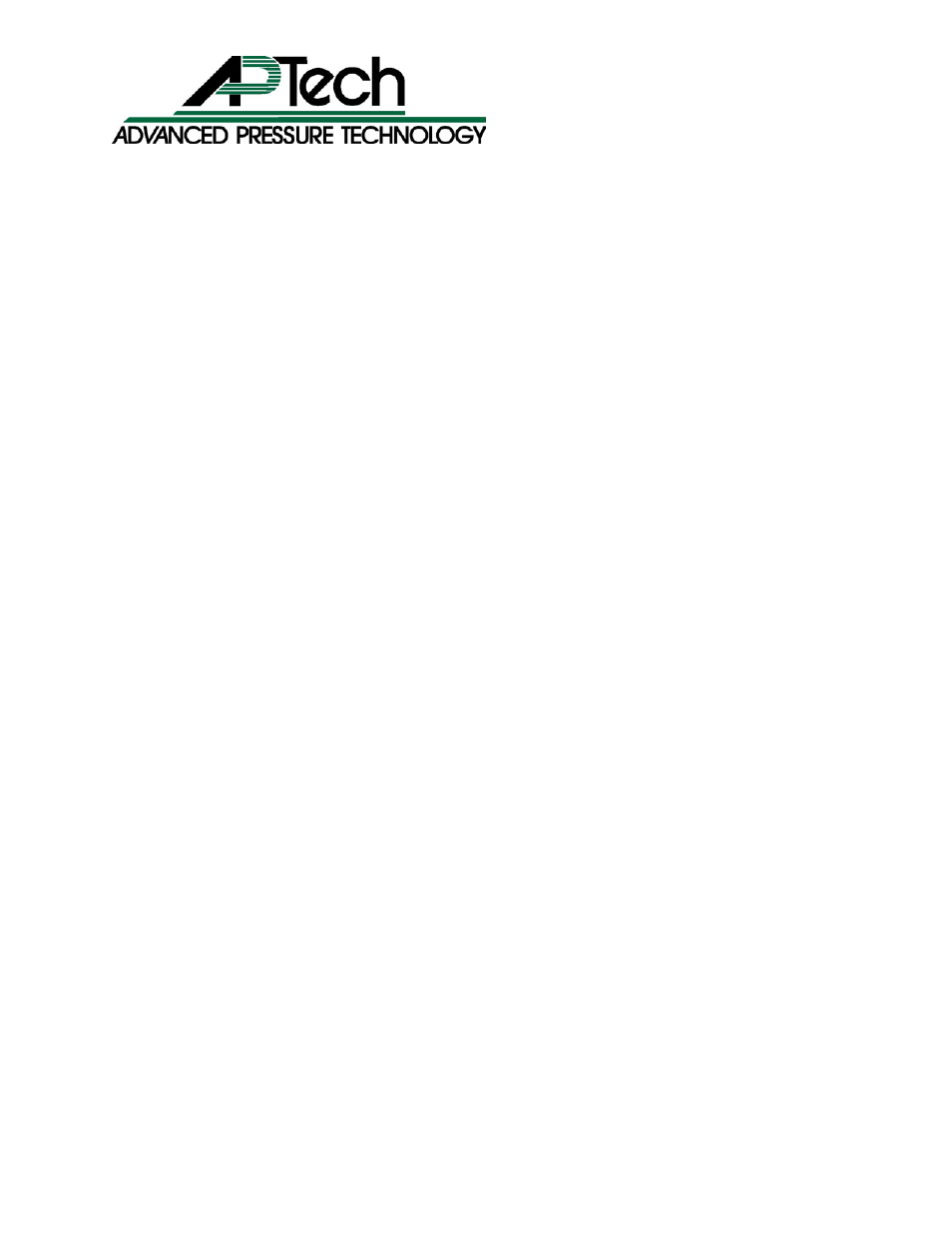
687 Technology Way
Napa, CA 94558
Phone: (707) 259-0102
FAX: (707) 259-0117
www.aptech-online.com
Manual 15000006 Rev 6
Page 1 of 4
Operation Manual
Diaphragm Sensed Gas Pressure Regulators
(AP/AZ/AK Models: 500, 1000, 1000T 10PA, 1100, 1200, 12PA, 1300, 1400T, 14PAT, 1500,
15PA, 1600, 1700, 1900, 2700, 9000, 90PA, 91PA, 9200
SL Models: 5200, 5400, 5500, 5800)
A. General information
AP Tech pressure regulators are used in gas delivery systems to reduce the supply (inlet) pressure
to a lower delivery (outlet) pressure. Many different models are available with many different
operating characteristics (pressure ratings, flow capabilities, etc.) and porting configurations.
Refer to the appropriate catalog data sheet for specific product information.
In this document, the term “supply pressure” is used to refer to the gas pressure on the high
pressure or inlet side of the regulator being discussed. “Supply pressure” may also commonly be
referred to as “inlet pressure”, “upstream pressure”, or “source pressure”.
“Delivery pressure” is used to refer to the gas pressure on the low pressure or outlet side of the
regulator being discussed. “Delivery pressure” may also commonly be referred to as “outlet
pressure” or “downstream pressure”.
B. System Design/Product Selection
1. AP Tech diaphragm sensed gas pressure regulators are not safety accessories per EU Pressure
Equipment Directive 97/23/EC or safety related devices per EU ATEX Directive 94/9/EC.
The EU Pressure Equipment Directive requires the system designer to install a safety
accessory (for example, safety relief valve or burst disc) where the design pressure of the
downstream system is lower than the upstream pressure.
2. When selecting the pressure regulator model and configuration, verify the following
information.
a.
Verify the materials of construction are compatible with the intended process gas.
b.
Verify the pressure and temperature ratings are acceptable for the intended application.
c.
If the regulator is to be equipped with either a supply or delivery pressure gauge, verify
that the pressure gauge range is suitable for the application. For high flow regulators used
at high supply pressures, be sure to consider the supply pressure effect when selecting
gauges. Refer to AP Tech Product Note PN 425 regarding supply pressure effect.
d.
Verify that the flow capability of the regulator is appropriate for the application.
3. Pressure regulators can be used under a large variety of operating conditions. The system
designers shall decide product selection based upon their own analysis and testing to verify
acceptable operation with specific equipment.
- SL 5500 SL 5400 SL 5200 AK 9200 AZ 9200 AP 9200 AK 91PA AZ 91PA AP 91PA AK 90PA AZ 90PA AP 90PA AK 9000 AZ 9000 AP 9000 AK 2700 AZ 2700 AP 2700 AK 1900 AZ 1900 AP 1900 AK 1700 AZ 1700 AP 1700 AK 1600 AZ 1600 AP 1600 AK 15PA AZ 15PA AP 15PA AK 1500 AZ 1500 AP 1500 AK 14PAT AZ 14PAT AP 14PAT AK 1400T AZ 1400T AP 1400T AK 1300 AZ 1300 AP 1300 AK 12PA AZ 12PA AP 12PA AK 1200 AZ 1200 AP 1200 AK 1100 AZ 1100 AP 1100 AK 1000T 10PA AZ 1000T 10PA AP 1000T 10PA AK 1000 AZ 1000 AP 1000 AK 500 AZ 500 AP 500
Document Outline
- A. General information
- B. System Design/Product Selection
- 1. AP Tech diaphragm sensed gas pressure regulators are not safety accessories per EU Pressure Equipment Directive 97/23/EC or safety related devices per EU ATEX Directive 94/9/EC. The EU Pressure Equipment Directive requires the system designer to in...
- 2. When selecting the pressure regulator model and configuration, verify the following information.
- a. Verify the materials of construction are compatible with the intended process gas.
- b. Verify the pressure and temperature ratings are acceptable for the intended application.
- c. If the regulator is to be equipped with either a supply or delivery pressure gauge, verify that the pressure gauge range is suitable for the application. For high flow regulators used at high supply pressures, be sure to consider the supply pressur...
- d. Verify that the flow capability of the regulator is appropriate for the application.
- 3. Pressure regulators can be used under a large variety of operating conditions. The system designers shall decide product selection based upon their own analysis and testing to verify acceptable operation with specific equipment.
- C. Installation
- 1. Verify the pressure rating is acceptable for the intended application.
- 2. If the regulator is equipped with either a supply or delivery pressure gauge, verify that the pressure gauge range is suitable for the application. For high flow regulators used at high supply pressures, be sure to consider the supply pressure effe...
- 3. Inspect the regulator to determine the flow path through the regulator and how the regulator will need to be installed in the system.
- a. The high pressure (inlet/supply) ports are labeled with an “HP” marked into the body near the ports. Arrows are sometimes used next to the HP to point toward a high pressure port.
- b. The low pressure (outlet/delivery) ports are labeled with an “LP” marked into the body near the ports. Arrows are sometimes used next to the LP to point toward a low pressure port.
- c. Dual stage regulators such as the AP1700 and AP2700 may have a monitor (1st stage outlet) port. The monitor port is labeled with an “MP” marked into the body near the port. Arrows are sometimes used next to the MP to point toward a monitor port.
- d. Always connect the gas source to the high pressure port. Never connect the gas source to the low pressure port or monitor port as the regulator will be damaged and leakage can result.
- 4. Install the regulator using the appropriate method described below. A large variety of porting options and connections are available.
- a. For tube stub connections, weld connectors or other components to the tube stubs per standard industry practice (reference SEMI standard F78).
- b. For metal face seal connectors, assemble connections per standard practice described by fitting supplier (typically 1/8 turn past fingertight).
- c. For NPT and BSPT connections, apply PTFE (e.g. Teflon) tape to connector threads and install connector in regulator body wrench tight.
- d. For compression tube fittings, insert the tubing until it bottoms out in the fitting. Assemble nut fingertight. Then tighten the nut 1-1/4 turns past fingertight for 1/4 inch to 1 inch tube connections. For remaking connections, only tighten the nu...
- e. For pneumatically actuated regulators (AP/AK/AZ10PA, AP/AK/AZ12PA, AP/AK/AZ14PAT, AP/AK/AZ15PA, AP90PA, and AP91PA), a separate line will need to be plumbed to provide the pneumatic actuator control pressure. The actuation port is 1/8th inch NPT a...
- f. Most regulators have threaded holes on the bottom for mounting. Refer to the applicable data sheet for details. However, for panel mount options, please refer to APTech Operation Manual Panel Mounting Gas Pressure Regulators for mounting procedures.
- 5. After installation, perform a leak test. A helium leak test, a pressure decay leak test, or a bubble leak test may be used depending on the application. A helium leak test is recommended for all face seal connections and welds per standard industry...
- D. Preset Regulator Operation
- 1. Perform the following to adjust the regulator delivery pressure set point
- a. Close the source valve.
- b. Open a downstream valve to vent the inlet and outlet side of the pressure regulator to atmospheric pressure.
- c. Remove the acorn nut from the stem.
- d. If present on the stem, loosen any hex nuts.
- e. Using a hex wrench, rotate the stem fully counterclockwise to close the regulator.
- f. Close the downstream valve.
- g. Slowly open the source valve to pressurize the regulator high pressure port.
- h. Using a hex wrench, rotate the stem clockwise to increase the delivery pressure to the desired set point.
- i. If present on the stem, tighten the bottom hex nut to 75 in-lb. If there is a second hex nut on the stem, tighten it against the bottom hex nut.
- j. Thread the acorn nut onto the stem and tighten against the hex nut (or cap if there are no hex nuts on the stem).
- 1. Perform the following to adjust the regulator delivery pressure set point
- E. Manually Adjustable Regulator Operation (non-PA models)
- 1. Perform the following to open the regulator or increase the regulator delivery pressure set point.
- 2. Perform the following to decrease the regulator delivery pressure set point.
- a. Open a downstream valve to initiate a flowing condition.
- b. Slowly rotate the wheel counterclockwise to reduce the delivery pressure.
- c. In order to obtain a specific set point under flowing conditions, continue to rotate the wheel counterclockwise to reduce the delivery pressure below the desired set point. Then, rotate the wheel clockwise to increase the delivery pressure to obtai...
- 3. Perform the following to close the regulator.
- F. Pneumatically Actuated Regulator Operation (PA models)
- 1. Perform the following to open the regulator or increase the regulator delivery pressure set point.
- 2. Perform the following to decrease the regulator delivery pressure set point.
- a. Open a downstream valve to initiate flow.
- b. Slowly reduce the actuation control pressure to reduce the delivery pressure.
- c. In order to obtain a specific set point under flowing conditions, continue to decrease the actuation control pressure to reduce the delivery pressure below the desired set point. Then, increase the actuation control pressure to increase the deliver...
- 3. Perform the following to close the regulator.