Vi piping continued. vii initial start-up – Midco Unipower G-Series User Manual
Page 8
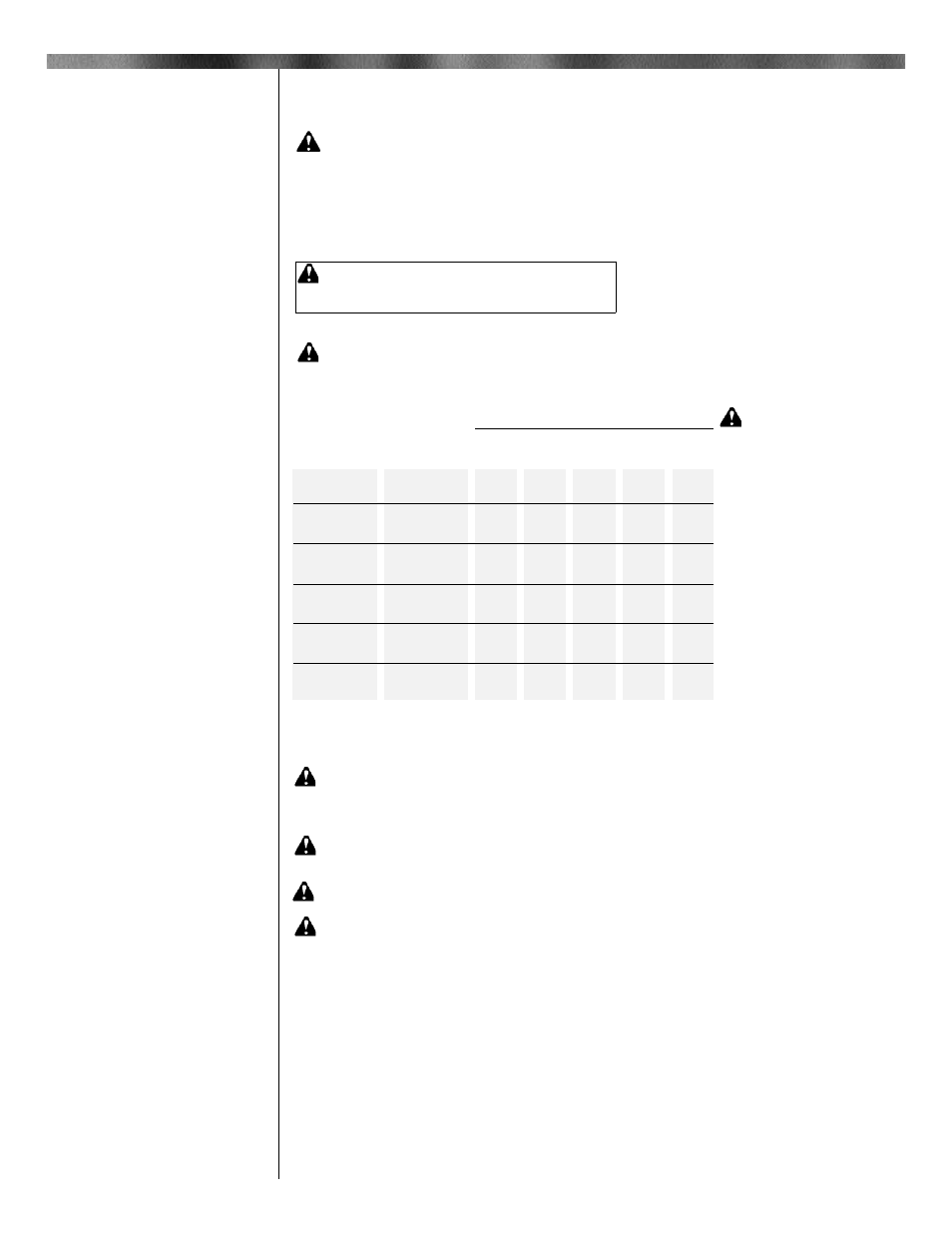
■
■
When high supply gas pressure is encountered, as in the case in many industrial plants, the gas line
size can be reduced to allow for a greater pressure drop; however, the size must be sufficient to deliver
necessary burner gas pressure.
CAUTION: High gas pressure supply lines require the proper pressure reducing regulators.
Install two separate high pressure regulators, of the Tight Shut-Off type upstream of the low
pressure regulators. One sized for main gas input, and one suitable
for the minimum flow regulating capacity of the pilot.
■
■
The high pressure regulators may be substituted for the low pressure regulators. If high pressure
regulators are used as substitutes, they must be adjustable down to a minimum of 2"
W.C. outlet pressure for the pilot and 5" W.C. for the main gas. They must be adjustable down to the
maximum burner inlet pressure rating (14" W.C.).
DANGER: Explosion hazard.
Do not use oxygen for pressure testing. An
explosion could occur during initial start-up.
■
■
When the gas supply line is about to be put into service it must be tested to insure that it is gas tight.
Use air or inert gas under pressure and test with soap and water or other liquids to locate leaks.
CAUTION: Because it is difficult to accurately control pressure, disconnect all low pressure
(14" W.C. max.)components (main and pilot) during supply pipe leak testing. Exposing low
pressure regulators and valves to a pressure over 1/2 PSIG (14" W.C.) will damage
components and void their warranties.
CAUTION: Do not
exceed maximum rated
capacity of burner
model-See Tables 1 and
2 .
Capacities shown are for
total pressure drop of .3"
W.C. For higher
permissible pressure drops
consult your fuel supplier.
■
■
Before gas is introduced
to the system, a check
must be made to see that
there are no open fittings
and to make sure the
burner main and pilot
manual valves are closed.
After checking above,
purge the gas line up to
the burner inlet. Purging
the air from the gas supply
line at this step will expedite the first light-off.
CAUTION: Purge outside the building. Do not purge into the gas utilization equipment
combustion chamber.
WARNING: Repeated unsuccessful attempts to light may result in accumulated gases in
gas utilization equipment and chimney. To prevent these gases from reaching an explosive
level, periodically purge the gas utilization equipment.
CAUTION: All cover plates, guards, and enclosures must be maintained in place at all
times except during maintenance and servicing.
CAUTION: Optional equipment and/or special limit controls such as high/low gas pressure
switches can alter the start-up procedure. See Section XIV Special Equipment.
1 .
Check the piping for leaks. A quick way to do this is to close the Main Manual Shut-off Valve and
manual pilot valve, then turn on the gas pressure to the gas supply line and observe the meter test
dial. There should be no movement of the test dial hand for at least twenty minutes. All other gas
appliances must be completely shut off during this test (including pilots). If a leak is detected it
should be located with a soap suds test. Test the main automatic valve for tightness. See Section
XII Main Automatic Valves for instructions. The ball valve is intended to be open at all times
except when testing for main valve leakage. The Main Manual Shut-Off Valve must be used for
manual gas shut-off.
2 .
Make sure that the burner main and pilot gas lines are completely purged of air. Do not purge into
the combustion chamber. Purge outside the building.
3 .
Make sure the burner power switch is off, manual valve is closed, pilot manual valve is closed,
motor is free to rotate, and flame safeguard reset button is set.
4 .
Make the proper settings on all limit controls and set controller to call for heat.
VI Piping Continued.
VII Initial Start-Up
Gas Supply
Pipe Size
N.P.T.
Type
of
Gas
20
1"
1
1
/
4
"
1
1
/
2
"
2"
2
1
/
2
"
3
Natural
Propane
Natural
Propane
Natural
Propane
Natural
Propane
Natural
Propane
Natural
Propane
350
550
730
1150
1100
1730
2100
2500
2500
40
300
400
630
610
960
1150
1800
1850
2500
2500
60
300
480
460
725
870
1370
1400
2200
2500
2500
100
330
320
500
610
960
980
1550
1700
2500
200
Approximate Capacity-MBH
Length of Pipe-Feet
Source: Gas Engineers Handbook—1974
Table 3: Schedule 40 Pipe Capacity Chart
385
500
785
760
1200
1450
2280
2300
2500
2500