Meter problem solving, Fault symptom causes / solutions – UEi Test Instruments SMART BELL User Manual
Page 9
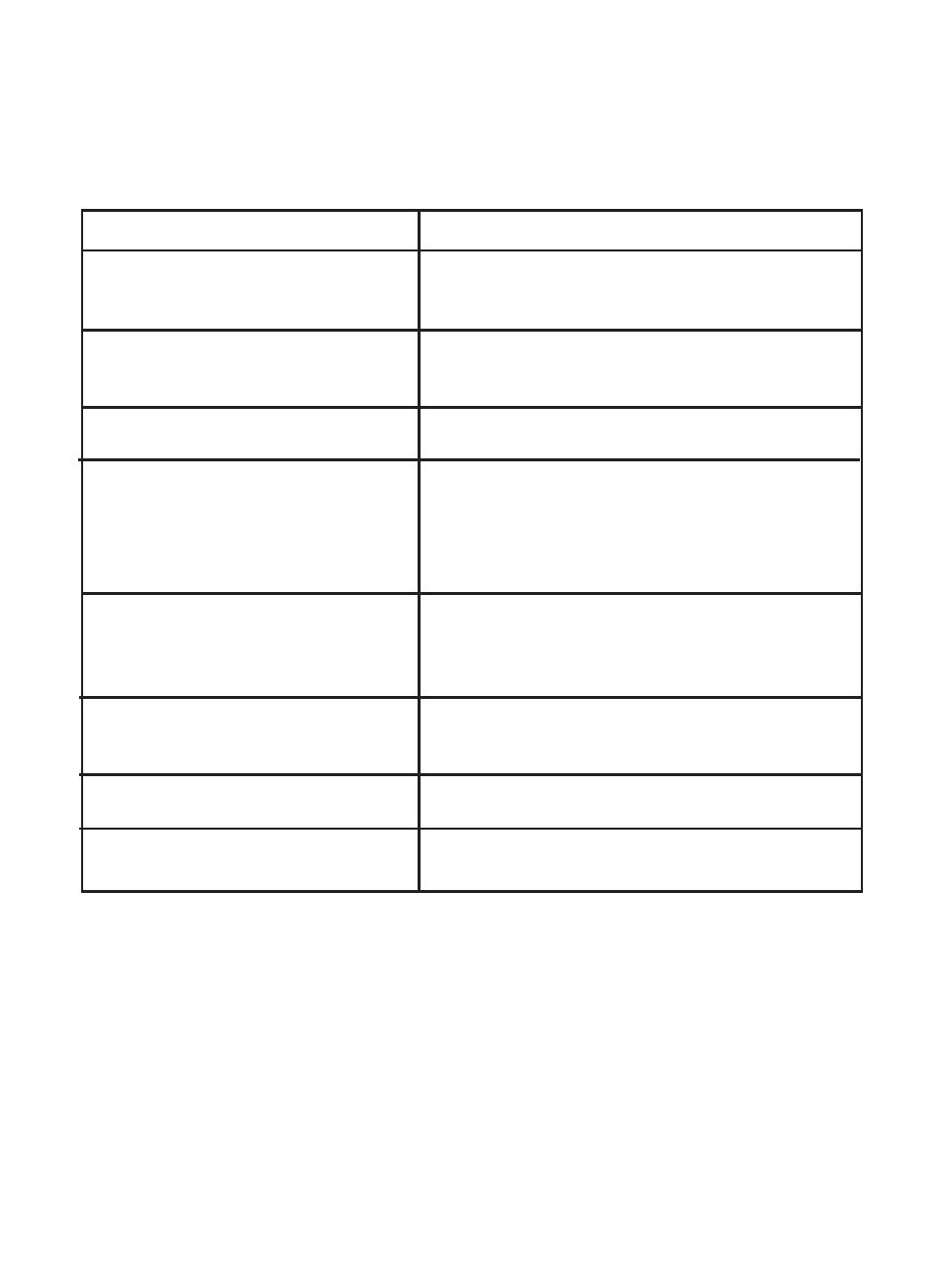
METER PROBLEM SOLVING
If any problems are not solved with these solutions, contact us or an authorized repair
center.
v
erify
P
roPer
o
PeratioN
o
f
C
omBuStioN
e
quiPmeNt
• To verify that equipment is operating as the manufacture designed it to work. This includes installation
tests for CO2, O2, Excess Air and stack temperatures
- A properly tuned combustion appliance will perform better, and reduce the likelihood of
call-backs for no-heat
• To verify that the maintenance work performed has corrected the problem
• To detect any defects early – possibly at installation
- Higher efficiency equipment is running at peak only when properly adjusted. As the complexity
of a system increases, so does the importance of proper adjustment of the combustion process.
• Improperly adjusted equipment not only fails to meet expected performance but could lead to future failures
• To check that the equipment is supplied with enough combustion air, make-up air and has proper
venting to exhaust the combustion by-products
• To establish a base-line of desired performance
- By tracking the performance over time you are able to see changes before they lead to
equipment failure.
v
erify
S
afe
o
PeratioN
o
f
C
omBuStioN
e
quiPmeNt
• Equipment that is not properly adjusted, or that has insufficient draft to vent combustion gases could
produce carbon monoxide in deadly quantities. The UEi CO91(Sold Seperately) test both flue gas and
ambient
• When customers complain about fumes it is usually an indication of improper operation. CO is a
colorless, odorless gas so the fumes are not the CO, but an indication that a problem may exist.
i
mProve
y
our
P
roduCtivity
& P
rofit
• The UEi S
mart
B
ell
combustion meter gives a quick, continuous readout of the combustion process.
Readings change in real-time as adjustments are made to help zero in on the proper setting. Compare
this to spot tests or other methods, and you will see your productivity rise.
• Proper testing with documented results will help you provide the proper service or equipment replacement
recommendations, and have the data to support this. Sales will increase because you are no longer
guessing, and the work provided is proper for the needs of the customer.
• Customers on a service contract will be provided excellent service, and you will quickly diagnose failures
and help keep the equipment up for the season.
i
mProve
C
uStomer
P
erCePtioN
o
f
y
our
S
erviCeS
• Provide your customers results of the performance of their equipment
• Reduce your customers energy expense by properly adjusting and maintaining their equipment
• Increase your confidence in the work performed and remember
i
f
y
ou
d
oN
’
t
t
eSt
, y
ou
d
oN
’
t
k
Now
Fault symptom
Causes / Solutions
CO2 too low
• Air leaking into probe, tubing, water trap
or connectors.
CO2 reading (- - - -)
• Meter was stored in a cold environment and
is not at normal working temperature.
Batteries not holding charge
• Batteries exhausted.
Meter does not respond to flue gas
• Particle filter blocked.
• Probe or tubing blocked.
• Pump not working or damaged with
contaminants.
Net temperature or Efficiency
• Ambient temperature set wrong during
calculation incorrect.
Automatic Calibration.
Flue temperature readings erratic
• Temperature plug reversed in socket.
• Faulty connection or break in cable or plug.
T flue or T nett displays (- - - -)
• Probe not connected or faulty
X-Air, EFF display
• CO2 reading is too low.
(- - - -)
∑
7