Amerex 05618 User Manual
Page 4
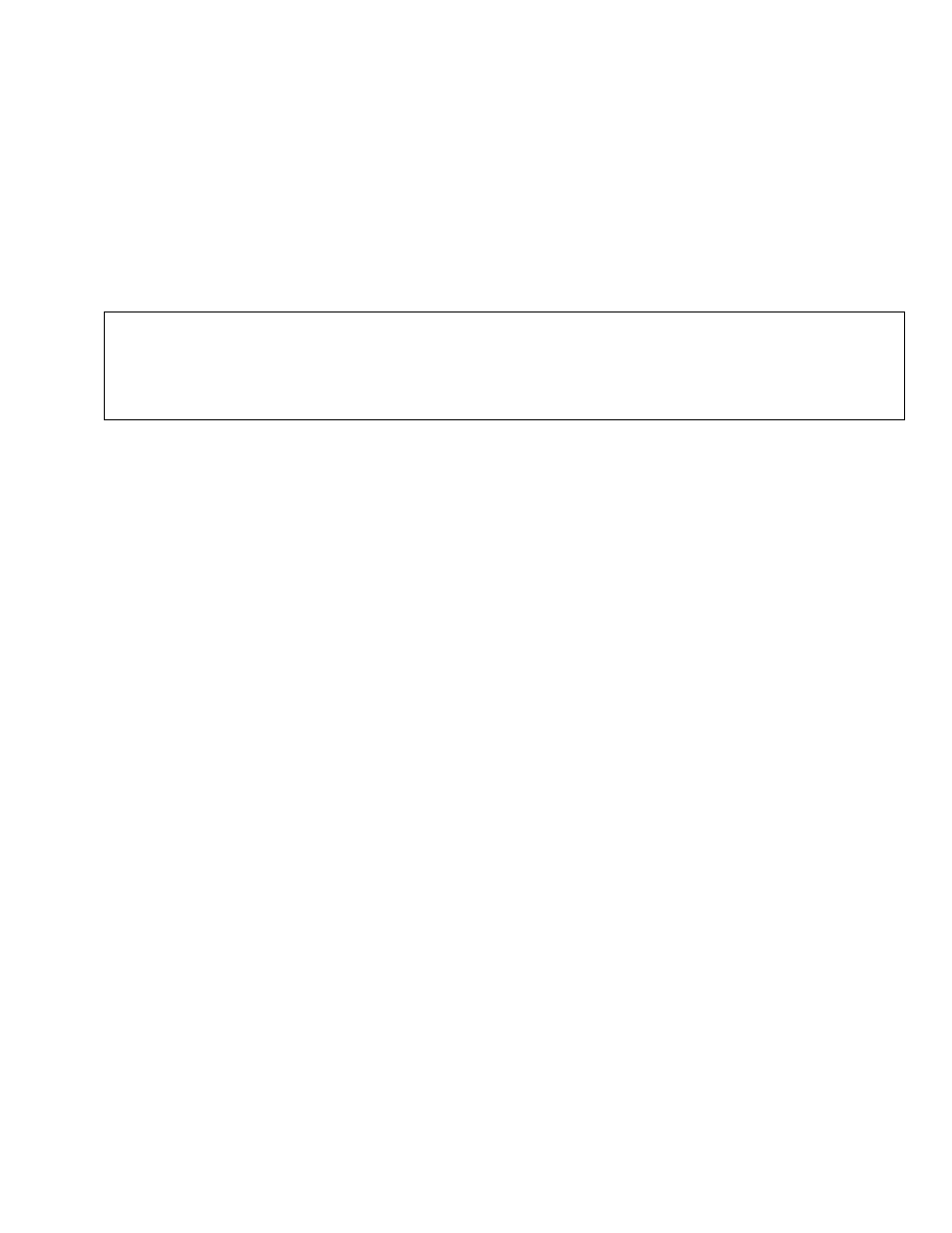
3
[NFPA-10]
A “quick check” should be made of the extinguisher for the following:
1. Located in designated place
2. No obstruction to access or visibility
3. Operating instructions on nameplate legible and facing outward
4. Seals and tamper indicators not broken or missing
5. Determine fullness by weighing
6. Examination for obvious physical damage, corrosion, leakage, or clogged nozzle or horn
7. obstruction
8. Condition of tires, carriage and hose
MAINTENANCE
Maintenance [NFPA 10] At least once a year (or more frequently if indicated by an inspection) Maintenance
should be performed. Maintenance is a thorough examination of the fire extinguisher. It is intended to give
maximum assurance that a fire extinguisher will operate effectively and safely. It includes a thorough examination
for physical damage or condition to prevent its operation and any necessary repair or replacement. It will
normally reveal if hydrostatic testing or internal maintenance is required.
MAINTENANCE PROCEDURE
NOTE: This procedure will be best accomplished with the extinguisher in an upright position on a level
surface.
1. Clean extinguisher to remove dirt, grease or foreign material. Check to make sure that the instruction
nameplate and UL manifest are securely fastened and legible. Inspect the cylinder for corrosion,
abrasion, dents or weld damage. If any of these conditions are found and you doubt the integrity of the
cylinder, hydrostatically test to factory test pressure, using the proof pressure method in accordance with
CGA C-6 and NFPA 10. Properly dispose of cylinder if in violation of the standard.
2. Inspect the extinguisher for damaged, missing or substitute parts. Only factory replacement parts are
approved for use on Amerex fire extinguishers.
3. Check the date of manufacture on the extinguisher cylinder dome. Cylinder must be hydrostatically
tested every 5 years to the test pressure indicated on the nameplate (3000 psi [20.69 MPa]).
Note: Complete maintenance should be performed whenever a hydrostatic test is being done. This
includes an inspection of the interior of the valve assembly, the spring and valve stem assembly, as well
as the interior of the cylinder.
4. Remove ring (locking) pin and check for freedom of movement. Replace if bent or if removal appears
difficult.
5. Check the horn shutoff lever for freedom of movement (squeeze and release several times). If the
operation is impeded, disassemble the nozzle, replace parts and/or properly lubricate as necessary.
Make sure that the horn is clear and unobstructed.
WARNING: SQUEEZE HORN SHUT-OFF LEVER SLOWLY. CARBON DIOXIDE MAY HAVE BEEN
LEFT IN THE HOSE FROM A PREVIOUS DISCHARGE. BE PREPARED FOR A POSSIBLE
DISCHARGE AND NOZZLE RECOIL.
6. Remove the hose and horn and inspect for damage. Replace the hose if cut or cracked, or if threaded
couplings are damaged. Replace the horn if brittle, cracked or deformed. Blow air through the hose and
nozzle assemblies to insure that the passage is clear of foreign material.
CAUTION: Carbon dioxide hose assemblies have a continuous metal braid that connects to both
couplings to minimize static shock. A hose continuity test should be performed using a basic conductivity