Service and maintenance – Detcon TP-524D User Manual
Page 29
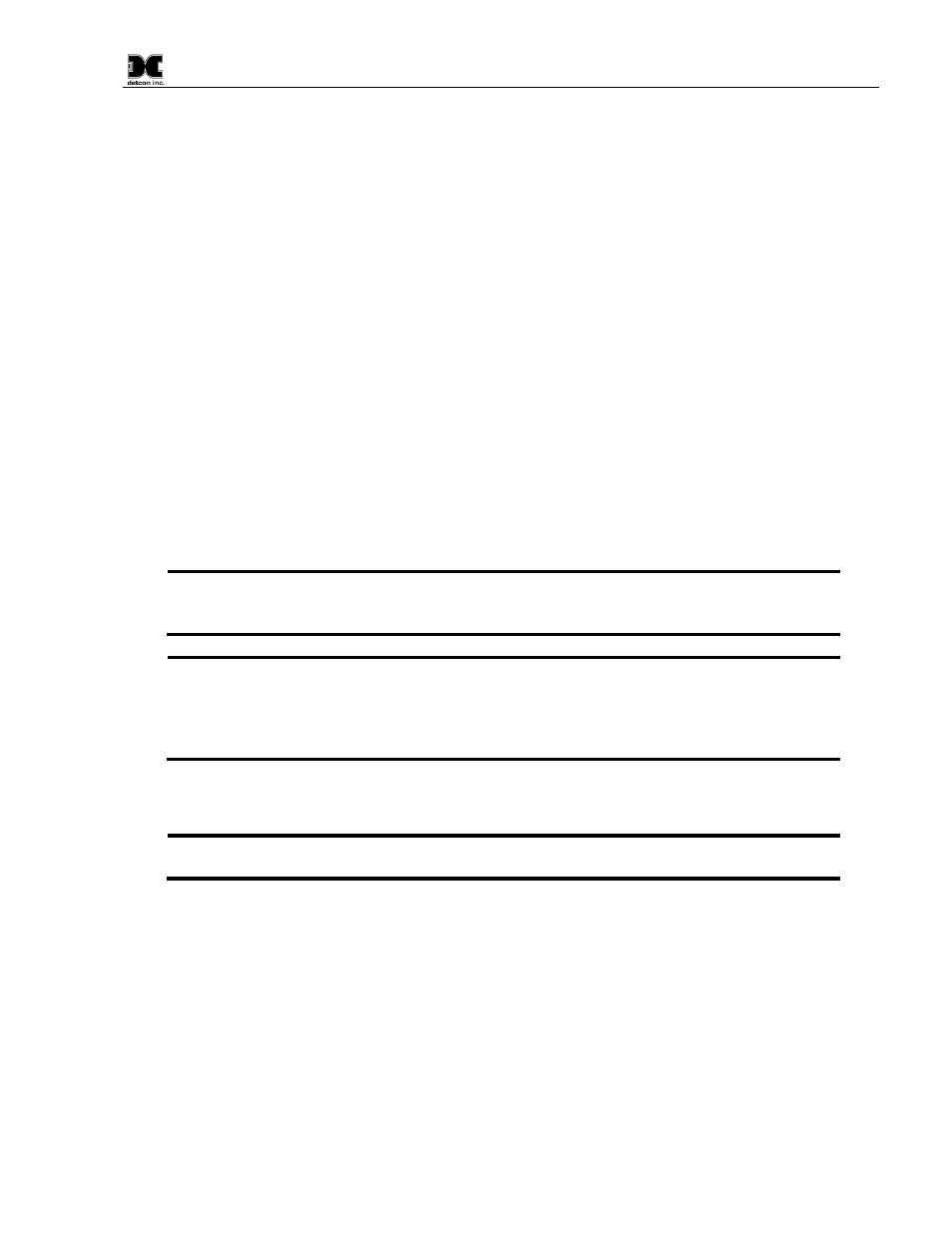
Model TP-524D
TP-524D Instruction Manual
Rev. 0.5
Page 25 of 36
4. Service and Maintenance
Calibration Frequency
In most applications, monthly to quarterly span calibration intervals will assure reliable detection. However,
industrial environments differ. Upon initial installation and commissioning, close frequency tests should be
performed, weekly to monthly.
Test results should be recorded and reviewed to determine a suitable
calibration interval. If, after 180 days, an AutoSpan Calibration is not performed, the sensor will generate an
AutoSpan Fault.
Visual Inspection
The Sensor should be inspected annually. Inspect for signs of corrosion, pitting, and water damage. During
visual inspection, the Splash Guard should be inspected to insure that it is not blocked. Examine the porous
316SS flame arrestor within the sensor’s bottom housing for signs of physical blockage or severe corrosion.
Also, inspect inside the Junction Box for signs of water accumulation or Terminal Block corrosion.
Condensation Prevention Packet
A moisture condensation packet should be installed in every explosion proof Junction Box. The moisture
condensation prevention packet will prevent the internal volume of the J-Box from condensing and
accumulating moisture due to day-night humidity changes. This packet provides a critical function and should
be replaced annually. Detcon’s PN is 960-202200-000.
NOTE: A desiccant cap with a desiccant packet is attached to the sensor cell housing to avoid
damage during storage and shipping. This prevents water from contacting the sensor film, and
as a result helps to retain the stability of the factory span calibration.
NOTE: Store the desiccant caps with the desiccant packets in a sealed container (i.e. zip-lock
bag) for future use. It is advisable (but not mandatory) to reinstall the desiccant cap and packet
during prolonged periods without power (more than 1 day is considered “prolonged”). An
active desiccant packet is blue in color and turns pink when consumed. (P/N 960-399800-000
Package of 10)
Replacement of H
2
S Sensor
NOTE: It is necessary to remove power while changing the H
2
S sensor in order to maintain
area classification while the junction box cover is removed. Proper “Hot Permits” may apply.
a) Remove the junction box cover and remove the Transmitter Module from the Connector PCB.
b) Remove the black, white, blue, and yellow wires coming from the H
2
S Sensor from the connector PCB.
c) Unthread the H
2
S Sensor from the junction box and thread the new H
2
S Sensor onto the junction box.
d) Connect the black, white, blue, and yellow wires from the new H
2
S sensor to the connector PCB.
e) Reinstall the Transmitter Module, and the junction box cover.
f) Perform “Set Heater Power (Section 3.5.4) to match the new H
2
S sensor with the Transmitter Module.
g) Perform a successful AutoSpan to match the new H
2
S sensor with the Transmitter Module (Section 3.4).