1 in-situ installation – COSA Xentaur Xentaur LPDT User Manual
Page 12
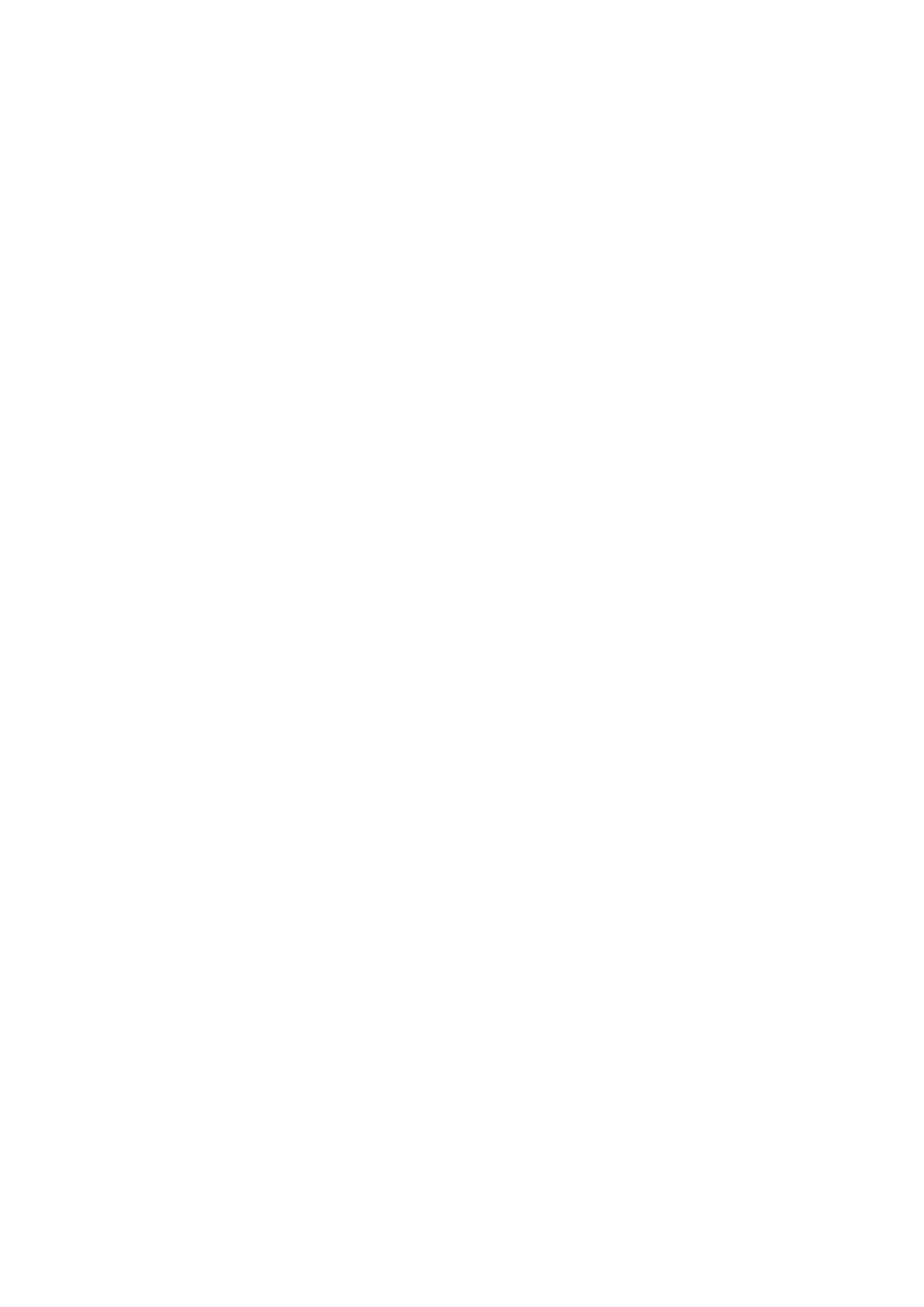
Section 2: Sensor and Sampling Techniques
page 5
diameter of tubing, number of interconnecting fittings, dead
space in tubing and manifolds; will influence the measure-
ment value and response time.
The high capacitance HTF™ sensors can be installed either
directly in the line to be sampled (in-situ), or in a slip stream
of a sample system (extractive).
To assure a long and accurate performance of the sensor, it
should be protected from contaminants such as liquids
(water, oil etc.), and particulates. The sintered stainless steel
sensor encapsulation protects from particulates larger than
100 microns, finer particulates (e.g. from degraded desic-
cant or rust) should be filtered with a particulate filter with
suitable capability, do not use hygroscopic filter materials.
2.3.1 In-situ Installation
In-situ installation is recommended only for measurements
where the gas pressure is expected to vary little, the gas is
expected to be free of contaminants, the gas temperature is
within the operating specifications of the sensor, and there is
no chance of liquids coalescing. Examples of applications
suited for in-situ installations are: pure gases, output of des-
iccant dryers (for instrument air), glove boxes, etc. For most
other applications in-situ installation should be avoided for
the following reasons:
•
Sample conditioning is almost always necessary to
avoid exposure of the sensor to liquid water and other
contaminants, such as hydrocarbons, which may dam-
age the sensor or affect accuracy over time.
•
Variations in line pressure affect the reading of the sen-
sor because dewpoint varies with pressure.
•
If the gas line is under pressure, it is more likely that
water condensation occurs which may damage the sen-
sor.