Selecting the right abrasive for the job, Ceramic aluminum oxide benefits oxide benefits, About work sharp ™ abrasive technology – Work Sharp WS3000 Woodworking Tool Sharpener User Guide User Manual
Page 10
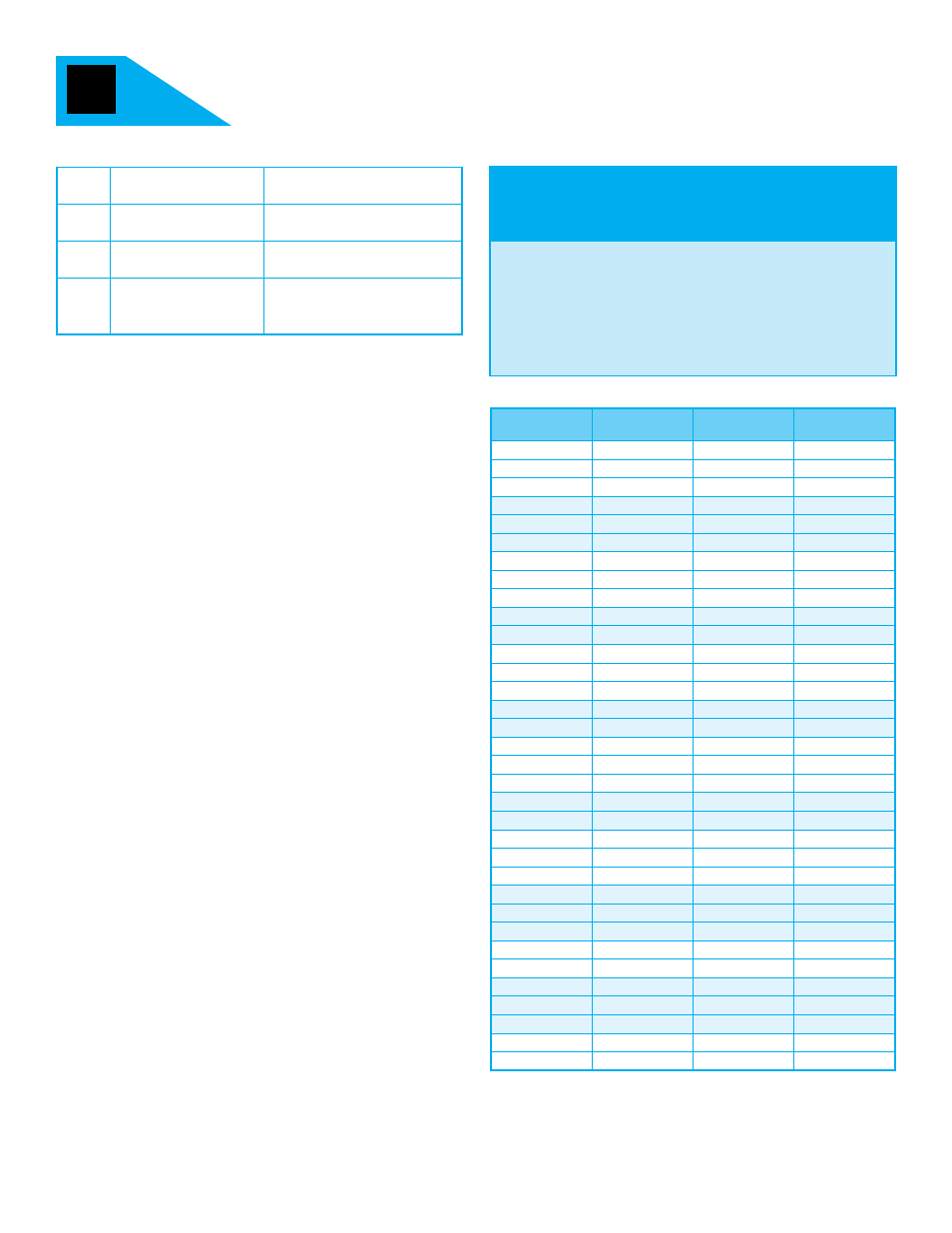
10
www.worksharptools.com
10
www.worksharptools.com
5
Selecting the Right
Abrasive for the Job
About WORK SHARP™ Abrasive Technology
Finish
•
Coated abrasive disks start flat and stay flat. (Bonded abrasives used
in stones and most power systems require frequent dressing to keep
the wheel flat.)
•
Heat treated aluminum oxide and ceramic abrasives provide a pol-
ished finish superior to oil and water stones without the mess.
•
Premium P-graded Abrasives provide more consistent cutter height
and smoother surface finish than traditional bonded and plated abra-
sives. (As bonded wheels wear they tend to round the edges/corner
of the tool. As the abrasive particles wear, the bond breaks down,
exposing new particles but always at a different depth.)
•
The grit size is engineered to provide optimal sharpness and surface
finish at each stage of sharpening. (Users who are interested in a
“utility sharp” edge will find exceptional edge performance on the
faster coarse grits without the need to hone.)
Speed
•
The abrasive selection is integrated with design of the
WORK
SHARP
®
drive train and cooling system to provide the fastest materi-
al removal rate while minimizing the risk of overheating tool steels.
•
The sharpening port includes a lapping abrasive that provides supe-
rior burr control and allows for 1-step re-sharpening.
•
Two-sided wheel and off-the-shelf abrasive makes it easy to switch
between coarse and fine abrasives. (Doesn’t require re-grading the
wheel just to switch between coarse and fine Abrasives. Doesn’t re-
quire an expensive selection of custom wheels or disks.)
Simplicity
•
Accepts standard 150 mm or 6" PSA-backed adhesive that is read-
ily available. (No custom adhesives or expensive custom wheels re-
quired. Coarse grits are available at most hardware/woodworking
stores. Fine grits are readily available at any automotive paint sup-
ply store.)
•
Abrasive disk life can be extended significantly by regular cleaning
using the supplied disk cleaner (Crepe Stick). Simply rub the Crepe
Stick across the surface of the Wheel to remove any loading or build-
up on the Abrasive.
CAMI (USA)
Individual Mesh
FEPA (Europe)
“P”
Micro Mesh
Micron
µ
80
P80
197
100
141
120
P120
127
P150
97
150
93
180
P180
78
220
66
P220
65
P240
58
240
53
P280
52
P320
46
280
44
P360
40
320
36
P400
35
P500
30
360
28
P600
25
400
1500
23
P800
21
500
P1000
18
600
1800
16
P1200
15
800
P1500
12
2400
11
P2000
10
1000
9
P2500
8.5
1200
3200
6.5
1350
3600
6
1500
4000
3
6000
2
8000
1.2
P120
equivalent to 127 µ
(micron)
for use with damaged or chipped
tools
P400
equivalent to 35 µ
(micron)
for use with nearly sharp tools
which only require a touch-up
P1000
equivalent to 18 µ
(micron)
for use when fine sharpening the
tool
Micro-
Mesh™
3600
equivalent to 6 µ
(micron)
for use when honing the tool
Ceramic
Aluminum
Oxide Benefits
Oxide Benefits
•
Fastest cut rate
•
Fast cut rate
•
Cool cutting
•
Consistent finish
•
Longest life
•
Increased life
•
Maximum load resistance
•
Reduced loading