Wellsaw 1000 User Manual
Page 2
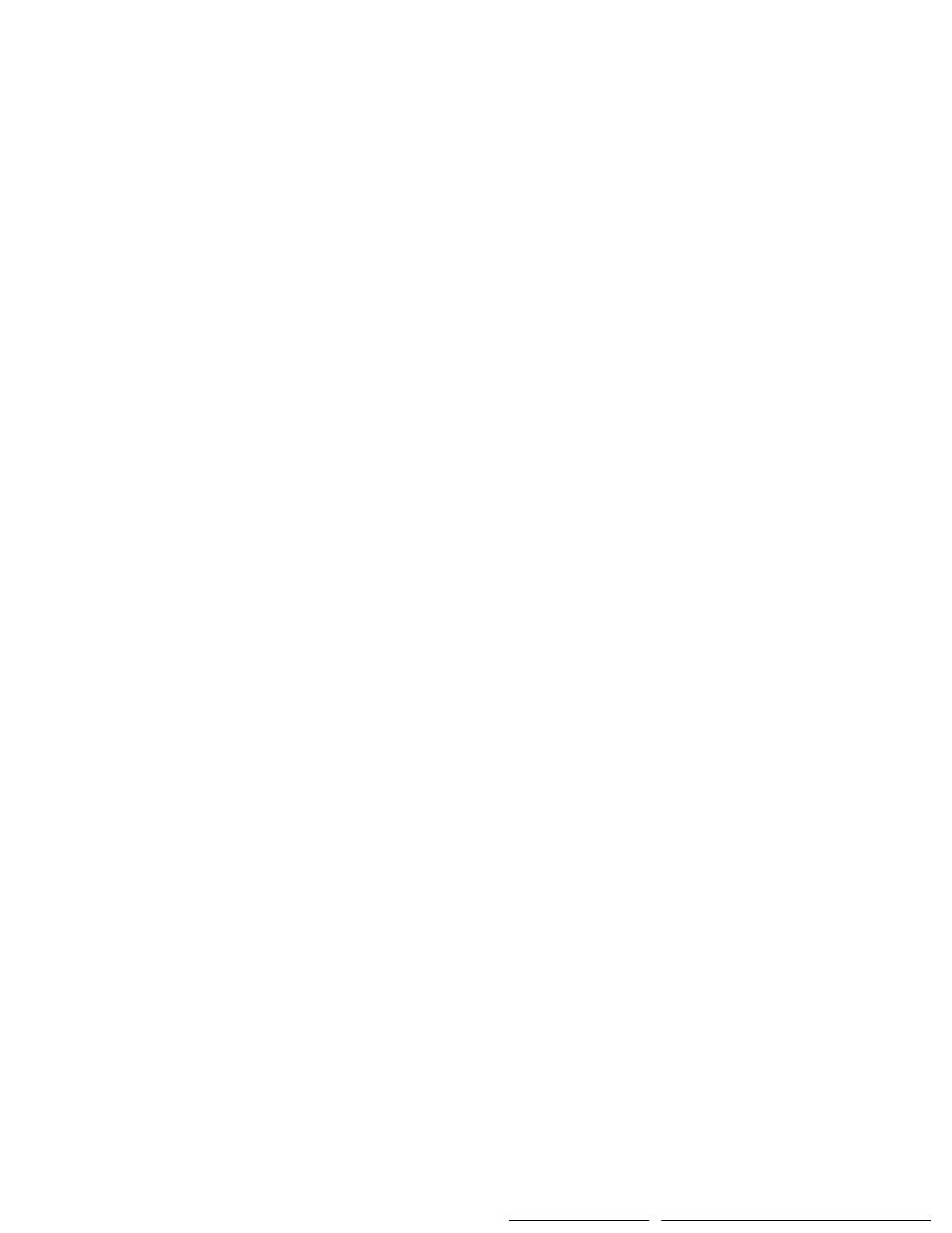
7.
Grasp blade an frame side and push toward
guide bracket beam to hold it in position on
wheels while turning hand wheel tension screw
until blade is taut.
8.
Start motor and tighten blade to proper operating
tension. If blade slips while cutting, increase the
tension.
AUTOMATIC STOP
When the saw blade has completed the cut through
the material, the saw frame drops on a trigger. This
operates a rod which opens the contacts in the
switch and automatically stops the motor.
It will be necessary to raise saw frame clear of the trigger
before machine can be started.
FIXED VISE JAW
The two pins in the fixed vise jaw should be kept
in place in order to insure square cuts. For cutting
angles, the pins must be removed and the vise jaws
turned to desired position and tightened with
clamp bolts. These pins enable operators to
quickly relocate fixed vise jaw for approximate 90'
cutting. For final and accurate adjustment, the vise
jaw should be squared with the blade.
The sliding vise jaw should be loosened and pushed
against fixed vise jaw, then tighten cap screw , leaving
vise parallel.
SLIDING VISE JAW
The sliding vise jaw is equipped with a ratchet and
ratchet dog for quick action and with a hand wheel for
tightening work in vise. Excessive pressure is not
required to hold material secure.
MAXIMUM CAPACITY
To obtain maximum vise capacity, remove vise jaw
pins and move fixed vise jaw toward motor end to
the last holes. Make sure stock in vise will not
strike the ratchet arm.
DASH POT
Machines are equipped with a dash pot (frame check)
for the purpose of stabilizing the downward travel of
the saw frame, thereby protecting saw blade from
damage. The action is hydraulic and controlled by
flow of fluid being by-passed through an orifice in
the piston on the downward stroke.
Fill to within 1 inch of top of the bottom cylinder
with Cities Services "Amplex 05" Hydraulic Oil or
equivalent.
FRAME WEIGHT ADJUSTMENT
Before adjusting frame spring at motor end, remove
the hydraulic dash pot and move sliding weight to
rear position (motor end). The frame spring should
be adjusted for approximately 16 pounds weight at
frame handle.
SWITCH
A "STOP-START" switch is installed across the line
to protect wiring and the motor. A heater coil breaks
the circuit if an overload occurs. The operator
should allow time for the coil to cool before trying
to restart.
Automatic shut-off operates when saw frame con-
tacts the switch trigger.
BELT
Pivoted mounting provides quick belt change. With
the belt in pulley grooves for the desired speed,
swing motor to put proper tension on belt. Tighten
thumb screw to hold motor in operating position.
FEEDING PRESSURE
Variations in feeding pressure are made by moving
weight on bar at top side of frame. Pressure on
blade increases as weight is moved to forward end.
The size and type of material governs the amount of
feeding pressure required on the blade. Excessive
pressure may cause a run-out of the blade.
SPEED SELECTION
Saws are equipped with step pulleys providing
speed selection of 50, 100, 175 and 275 feet per
minute. High speeds are suggested for cutting thin-
wall tubing, channels, aluminum, brass, or any
metal that will not burn the teeth; medium speed for
general cutting such as cold rolled, machine steels,
heavy channels, etc. Run in low speed for cutting
nickel steels, or metal which requires a slow speed
on a lathe. When cutting brass, use a blade which
has not previously cut other metal, and apply bees-
wax to the teeth.
If teeth wear off unusually fast, use a lower speed.
BLADE BRUSHES
Brushes should be cleaned frequently in kerosene
and reversed to take advantage of both rows of
bristles.
For efficient cutting and blade life, replace blade brushes
when worn.
In bolting brushes to angles, be sure wire bristles
are bent in the same direction the blade travels.
SECTION 11 — MAINTENANCE INSTRUCTIONS
BLADE GUIDES
The blade guides are arranged to hold the blade in
alignment both vertically and horizontally.