Principles of magnetic work holding, 1 principles of magnetic work holding -4, Igure – Walker Magnetics TURBOMILL 40B User Manual
Page 15: Agnetic, Ttraction
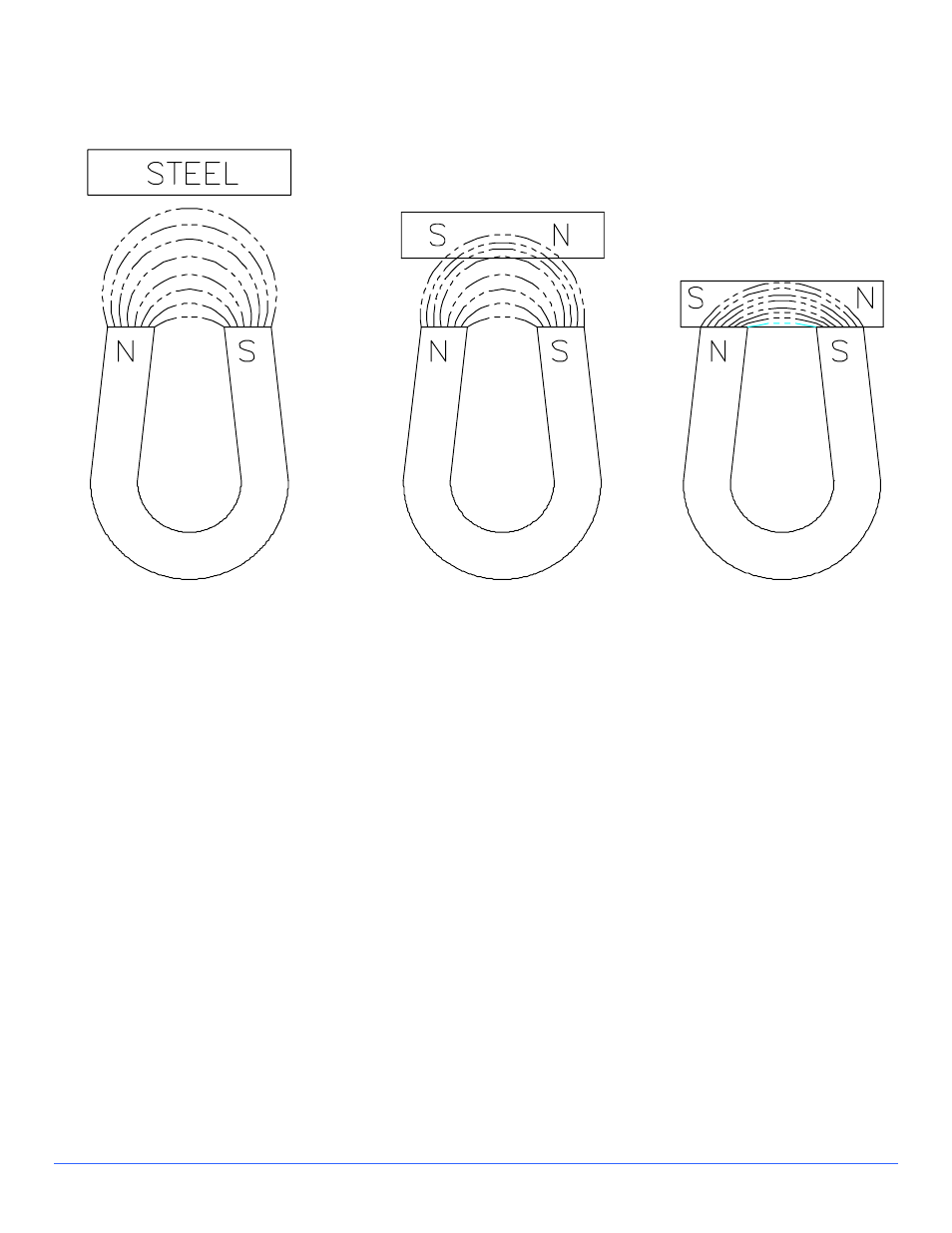
O.S. WALKER Co. Inc., Turbomill Electroperm Chucks
DD15508M.doc Rev. ~, September 17, 2002
4-4
Figure 4-2 Magnetic Attraction
4.5.1 Principles of Magnetic Work Holding
The ability to hold a work piece magnetically on a milling chuck is dependent on the
characteristics of the work piece itself and, of course, the degree of machine force
exerted upon it.
To establish the feasibility of a specific application, three key parameters must be
considered.
1) Work Piece Material
As a rule, though there are some exceptions, magnetic conductivity in a material
decreases with greater alloy content. Mild steel is more conductive than tool steel,
which is more conductive than cast iron, and so on.
2) Work Piece Contact Surface
Any condition that creates a non-magnetic gap between the chuck and the work
piece will reduce holding force. Rust, scale, weld spatter, shims; warped pieces can
all contribute to reduced holding. The greater the air gap in a magnetic circuit, the
more inefficient it is. Therefore, hold down force increases with flatter contact
surfaces.
3) Work Piece Contact Area
Hold down pulling force is measured in lbs/sq. inch Therefore; increased contact
area will ultimately increase hold down force.