Air inlet & priming, Air exhaust, Between uses – SANDPIPER ST25A User Manual
Page 2: Check valve servicing, Diaphragm servicing
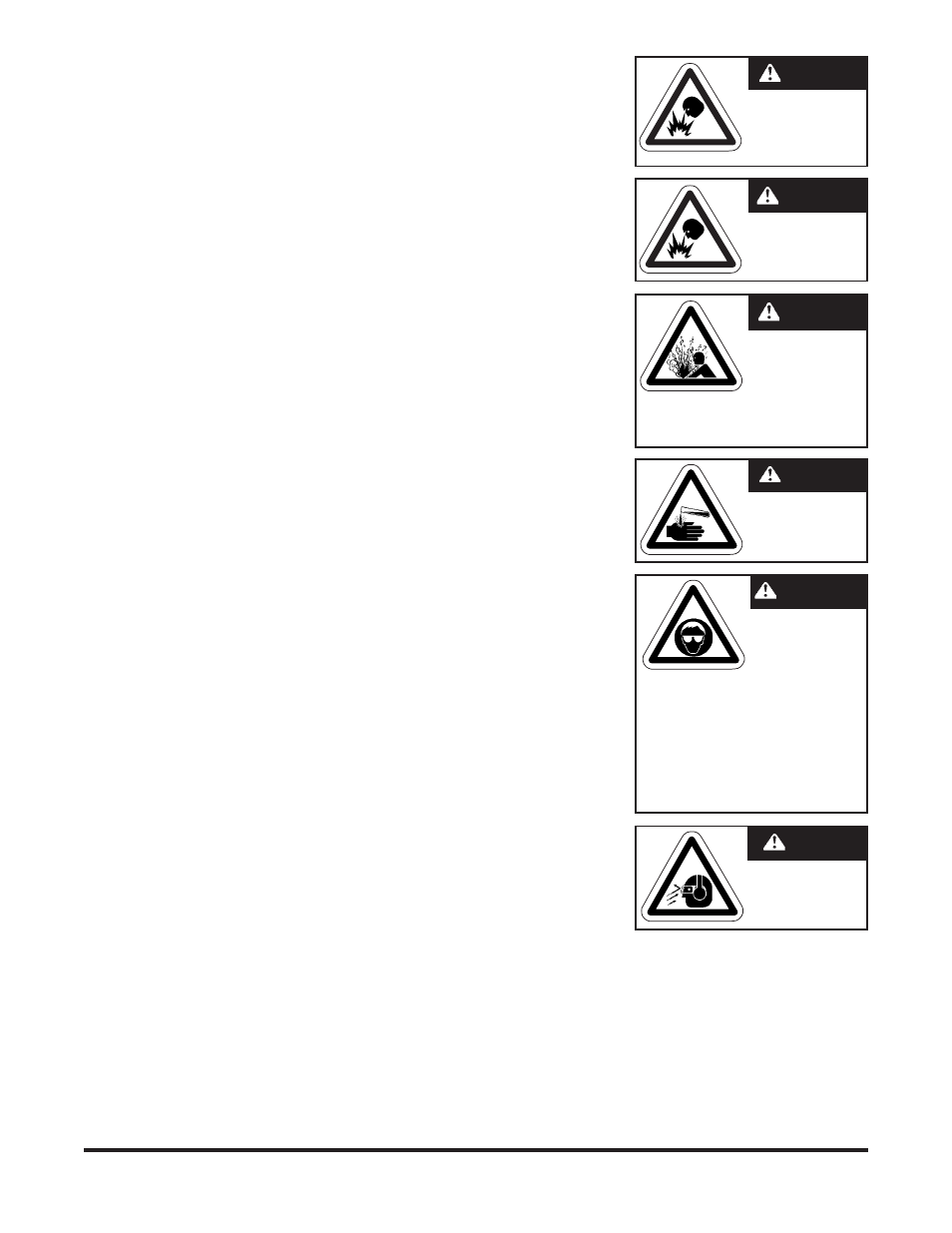
520-005-000 1/04
Models ST1-A, ST25A Type 4 Page 2
Air inleT & PriMinG
For start-up, open an air valve approximately 1/2" to 3/4"
turn. After the unit primes,
an air valve can be opened to increase flow as desired. If opening the valve increases
cycling rate, but does not increase flow rate, cavitation has occurred, and the valve
should be closed slightly.
For the most efficient use of compressed air and the longest diaphragm life, throttle
the air inlet to the lowest cycling rate that does not reduce flow.
Air eXHAUST
If a diaphragm fails, the pumped liquid or fumes can enter the air end of the pump,
and be exhausted into the atmosphere. When pumping hazardous or toxic materials,
pipe the exhaust to an appropriate area for safe disposition.
This pump can be submerged if materials of construction are compatible with the
liquid. The air exhaust must be piped above the liquid level. Piping used for the air
exhaust must not be smaller than 1" (2.54 cm). Reducing the pipe size will restrict air
flow and reduce pump performance. When the product source is at a higher level than
the pump (flooded suction), pipe the exhaust higher than the product source to prevent
siphoning spills.
Freezing or icing of the air exhaust can occur under certain temperature and humidity
conditions. Use of an air dryer should eliminate most icing problems.
BeTWeen USeS
When used for materials that tend to settle out or transform to solid form, the pump
should be completely flushed after each use, to prevent damage. Product remaining
in the pump between uses could dry out or settle out. This could cause problems with
valves and diaphragms at re-start. In freezing temperatures, the pump must be drained
between uses in all cases.
cHecK VAlVe SerVicinG
Need for inspection or service is usually indicated by poor priming, unstable cycling,
reduced performance or the pump’s cycling but not pumping. (See Fig. 3)
Inspect the surfaces of both check valve and seat for wear or damage that could
prevent proper sealing. If pump is to prime properly, valves must seat air tight.
DiAPHrAGM SerVicinG
Driver Diaphragms:
Drain the intermediate diaphragm housing (Item 36) by removing the pipe plug
directly beneath and behind the mounting flange. This port is also used for the optional
Electronic Leak Detector (Warren Rupp p/n 032-017-000 115 volt or p/n 032-018-000
220 volt). Remove four bolts securing the manifold flange to the chamber. Remove eight
nuts (Item 42) securing the inner diaphragm chamber (Item 22) and remove the outer
driver diaphragm assembly by pulling it axially off the studs. This permits inspection of
the Virgin PTFE diaphragm and the driver diaphragm. Pumping diaphragm chambers
need not be separated for access to the driver diaphragm. Loosen the plate which
secures the diaphragm and plate to the rod by keeping the diaphragm engaged with
the inner diaphragm chamber (Item 22) by inserting two or three capscrews through the
bolt holes so that the diaphragm cannot rotate when loosening. The diaphragm plates,
diaphragm and bumper will now come off the assembly. Repeat all actions if the other
diaphragm needs to be inspected or replaced.
noTe: See “filling of Driver chamber with liquid” for the correct procedure to
recharge the pump for operation.
Reassembly is the reverse of the tear down. During reassembly, be sure that the
rubber bumper is on the rod on each side (see Figure 5). Install the diaphragm with the
natural bulge to the outside as marked on the diaphragm. Install the heavier plate on the
outer side of the diaphragm. Be sure that the large radius side of each plate is toward the
diaphragm. Place the sealing washer between the inner diaphragm plate and the end
of the rod. Tighten the plate to approximately 25 ft. lbs. (33.89 Newton meters). Torque
while allowing the diaphragm to turn freely with the plate. Hold the opposite side with a
wrench on the plate to prevent rotation of the rod. If the opposite chamber is assembled,
this will not be necessary.
When reassembling the outer chambers and the manifold, the bolts securing the
manifold flange to the chamber should be snugged prior to tightening the manifold flange.
Finish tightening the manifold flange bolts after the chamber bolting is secured.
Do not smoke near
t h e p u m p o r u s e
the pump near an
open flame. Fire or
explosion could result.
WArninG
This pump must not be
used for fluid transfer
into aircraft.
WArninG
T h i s p u m p i s
pressurized internally
with air pressure
during operation.
Always make certain
that all bolting is in good condition and
that all of the correct bolting is reinstalled
during assembly.
WArninG
When used for toxic or
aggressive fluids, the
pump should always
be flushed clean prior
to disassembly.
WArninG
Before doing any
main-tenance on the
pump, be certain all
pressure is completely
v e n t e d f r o m t h e
pump, suction, discharge, piping, and
all other openings and connections. Be
certain the air supply is locked out or
made non-operational, so that it cannot
be started while work is being done on
the pump. Be certain that approved eye
protection and protective clothing are
worn all times in the vicinity of the pump.
Failure to follow these recommendations
may result in serious injury or death.
WArninG
Airborne particles and
loud noise hazards.
Wear ear and eye
protection.
WArninG