Check valve servicing, Diaphragm servicing/filling driver fluid, Cylinder piston servicing – SANDPIPER MHP2M User Manual
Page 2: Air valve lubrication
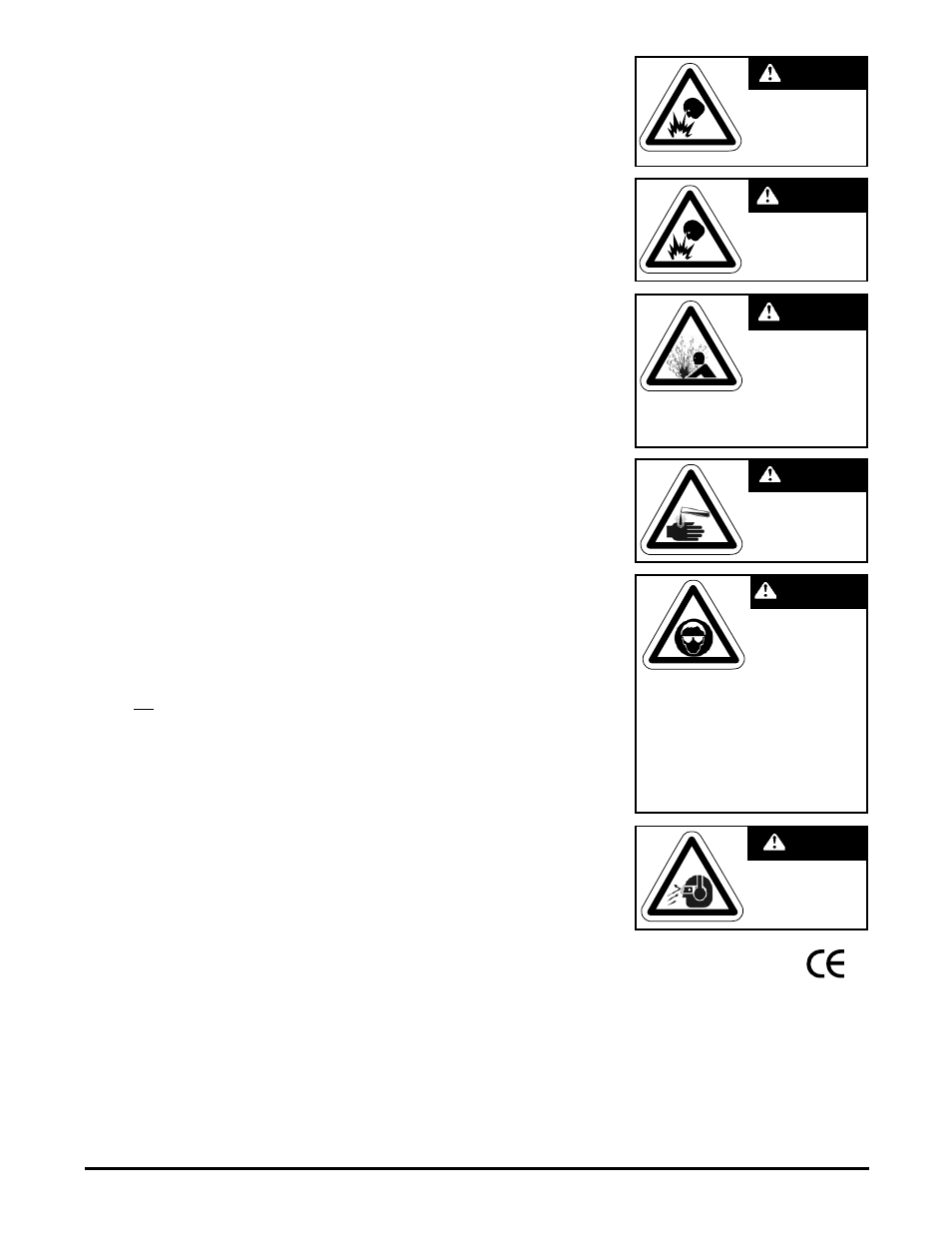
Model MHP2M Page 2
mhp2mdl4sm-rev0513
CHECK VALVE SERVICING
Need for inspection or service is usually indicated by poor priming, unstable cycling,
reduced performance or the pump’s cycling but not pumping.
DIAPHRAGM SERVICING/FILLING DRIVER FLUID
Motive power is delivered to the single diaphragm of the pump through a
fluid cell located between the diaphragm and the drive piston. During preventative
maintenance servicing (where the diaphragm has not ruptured, and the fluid cell is still
filled), the fluid should be drained from the chamber by removing the pipe plug, in the
lower most portion of inner chamber, item 54.
To fill the fluid cell, the piston(s) must be on full discharge stroke. To do this and hold
during fill procedure, remove item 46, (fitting) from the cylinder cap (item 15) and insert
air pressure. This need not be more than 10 PSI. This will move the piston(s) and hold
them in the discharge position. Remove the pipe plug at the top of the fluid chamber,
and fill the chamber with ethylene glycol (anti-freeze). The chamber will take 3000 ml
(101.5 fluid ounces) of fluid. If the diaphragm is Teflon, use 2800 ml (95 fluid ounces).
Tilt the pump to evacuate air pockets from the fluid chamber. A box wrench can be
used to flex the diaphragm and purge air from the fluid chamber. Fill the chamber to
the top of the fill hole, and re-insert the pipe plug, using thread compound.
If the glycol cell fluid is not compatible with the pumped product or would form a
potentially dangerous mixture if the diaphragm ruptured, consult the factory before
choosing an alternative fluid.
CYLINDER PISTON SERVICING
The driver fluid must be drained (see above) to service the cylinder piston. The
piston seals are different on the air side versus the driver fluid side. Typically, the
fluid side will require replacement before the air side. Remove the nuts and wash-
ers that secure the air side piston cap and inner fluid chamber to the intermediate
bracket. The cylinders may now be removed. Inspect the cylinder wall carefully.
Scratches can cause driver fluid to leak to the air side of the pump, which can find
its way to the exhaust muffler. Scratches on the air cylinder will cause too much
air to leak when on pressure stroke. The locknuts holding the cylinder to the rod
can now be removed. Carefully inspect the piston for scratches, burrs and wear,
especially if the piston seals are worn.
The piston seals can now be inspected or replaced. AIR SIDE–The air side piston
has a T-Seal. If the seal is worn showing flat areas or gouges, it will require replace-
ment. Remove seal and back-up (spacer). Remove wear rings and carefully inspect
for wear. During reassembly make sure the ends of the back up spacer and wear ring
end are not across from each other. WET SIDE–The wet side piston has a yellow PSP
seal. Inspect for flat spots and gouges. Behind the seal is an energizer ring that helps
to load the seal against the cylinder wall. (The energizer ring is included with the new
seal.) The wear rings are the same as on the air side. Again, make sure the ends are
not across from each other.
Reassembly of both pistons is the opposite of removal. Make sure the side of the
locknut with the seal is next to the piston. The groove in the piston or o-ring (item
35), must be toward the pump center (o-ring seals next to the rod). Apply a heavy oil to
the piston seals when sliding on the cylinder. The piston/nut should be torqued at 500
in./lbs. (56.49 Newton meters). The studs that secure the cylinders to the intermediate
should be torqued at 250 in./lbs. (28.24 Newton meters).
IMPORTANT NOTE: Reas-
sembly of the wet side piston/seal assembly differs from the air side in that it must be
carefully pressed into the cylinder. An arbor press is commonly used for this purpose.
AIR VALVE LUBRICATION
The SANDPIPER pump’s pilot valve and main air valve assemblies are
designed to operate WITHOUT lubrication. This is the preferred mode of operation.
There may be instances of personal preference, or poor quality air supplies when
lubrication of the compressed air supply is required. The pump air system will operate
with properly lubricated compressed air supplies. Proper lubricatrion of the compressed
air supply would entail the use of an air line lubricator (available from Warren Rupp)
set to deliver one drop of 10 wt., non-detergent oil for every 20 SCFM of air the pump
consumed at its point of operation. Consult the pump’s published performance curve
to determine this.
It is important to remember to inspect the sleeve and spool set routinely. It should
Do not smoke near
the pump or use
the pump near an
open flame. Fire or
explosion could result.
WARNING
This pump must not
be used for fluid
transfer into aircraft.
WARNING
T h i s p u m p i s
pressurized internally
with air pressure
during operation.
Always make certain
that all bolting is in good condition and
that all of the correct bolting is reinstalled
during assembly.
WARNING
When used for toxic or
aggressive fluids, the
pump should always
be flushed clean prior
to disassembly.
WARNING
Before doing any
main-tenance on the
pump, be certain
a l l p r e s s u r e i s
completely vented
from the pump, suction, discharge, piping,
and all other openings and connections.
Be certain the air supply is locked out or
made non-operational, so that it cannot
be started while work is being done on
the pump. Be certain that approved eye
protection and protective clothing are
worn all times in the vicinity of the pump.
Failure to follow these recommendations
may result in serious injury or death.
WARNING
Airborne particles and
loud noise hazards.
Wear ear and eye
protection.
WARNING
P u m p c o m p l i e s w i t h E N 8 0 9
P u m p i n g D i r e c t i v e , D i r e c t i v e
2006/42/EC Machinery, according to
Annex VIII.