Troubleshooting – RIKON Power Tools 80-805 User Manual
Page 17
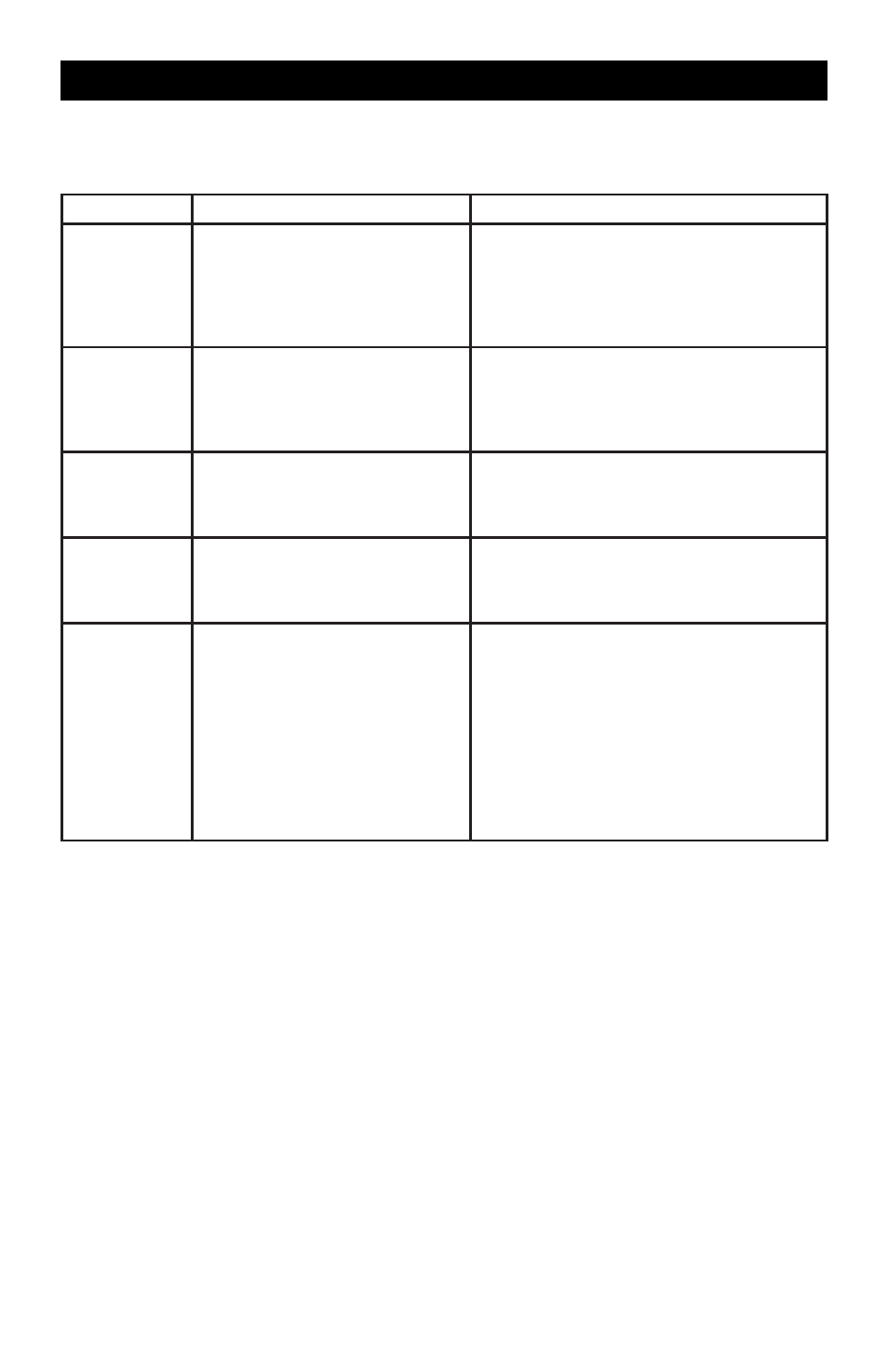
TROUBLESHOOTING
TO PREVENT INJURY TO YOURSELF or damage to the Bench Grinder, turn the switch to the
“OFF” position and unplug the power cord from the electrical receptacle before making any
adjustments.
Page 16
PROBLEM
LIKELY CAUSE(S)
SOLUTION(S)
Motor does
not run
1. Machine not plugged in
2. Power switch in “OFF” position
3. Power switch or cord is faulty
4. Fuse or circuit breaker are open
5. Material wedged between wheel
and tool rest or guard
1. Plug power cord into electrical receptacle
2. Lift switch to “ON” postion
3. Replace switch or power cord
4. Overloaded electrical circuit
5. Turn grinder off, unplug power cord and
remove material
Motor does
not have full
power
1. Incorrect line voltage
2. Motor capacitor has failed
1. Have a qualified electrican check circuit for
proper voltage
2. Replace motor capacitor
Motor runs hot
1. Motor is overloaded
2. Poor air circulation around motor
3. Overuse in high ambient
temperature room
1. Reduce pressure on workpiece
2. Remove any blockage around motor
3. Reduce runtime to 20 minutes or less
Motor stalls or
runs slow
1. Motor is overloaded
2. Incorrect line voltage
3. Motor capacitor has failed
1. Reduce pressure on workpiece
2. Have a qualified electrican check circuit for
proper voltage
3. Replace motor capacitor
Fuses blow or
circuit breaker
trips
1. Motor is overloaded
2. Overloaded electrical circuit
3. Undersized fuse or circuit breaker
4. Defective cord, plug or switch
creating a short circuit
5. Undersized or excessive length of
extention cord, see page 8
6. Material wedged between wheel
and tool rest or guard
1. Reduce pressure on workpiece
2. Reduce the amount of items on circuit
3. Replace with correct fuse or circuit breaker
4. Replace with new parts
5. Use correct size and length of extension cord
6. Turn grinder off, unplug power cord and
remove material
CORRECTING EXCESSIVE WHEEL WOBBLE
The performance of your bench grinder can be improved with just a little time performing a few
simple tune-up steps. Make sure the grinder is always unplugged during any adjustment or wheel
changes.
The stamped steel flange washers may not run perfectly true and can be adjusted by making a
reference mark on each flange washer and the wheel to record their original location. Next, loosen
the shaft nut and slightly rotate one flange washer clockwise and the other counterclockwise.
These movements should only be about one-half an inch at a time; then snug up the shaft nut by
hand and spin the wheel by hand. Observe any change. This rotation should minimize any
oscillation caused by flange washers. Now re-tighten the shaft nuts and dress the wheel. The
center bushings supplied by aftermarket grinding wheel manufacturers are designed to roughly
center the wheel on the shaft. The flange washers hold the wheel; dressing with a wheel dresser
will make the wheel run true.
If adjusting the flange washers does not make the wheel run without side-to-side oscillation, then
remove the wheel and flange washers and check the shoulder on the motor shaft at the point
where the flange washer seats against it. A slight burr on the edge of the shoulder can stop the
flange washer from seating properly. This can be removed by using a file to smooth the edge of
the shoulder. Look for any roughness on the surfaces of the flange washers and smooth these
spots on sandpaper placed on a flat surface. Then replace the wheel, re-adjust the flange
washers, and dress the wheel.