Operation, Constant current (cc-stick) welding, B-5 tig welding – Lincoln Electric IM976 VANTAGE 300 User Manual
Page 23: Typical vantage® 300 fuel consumption
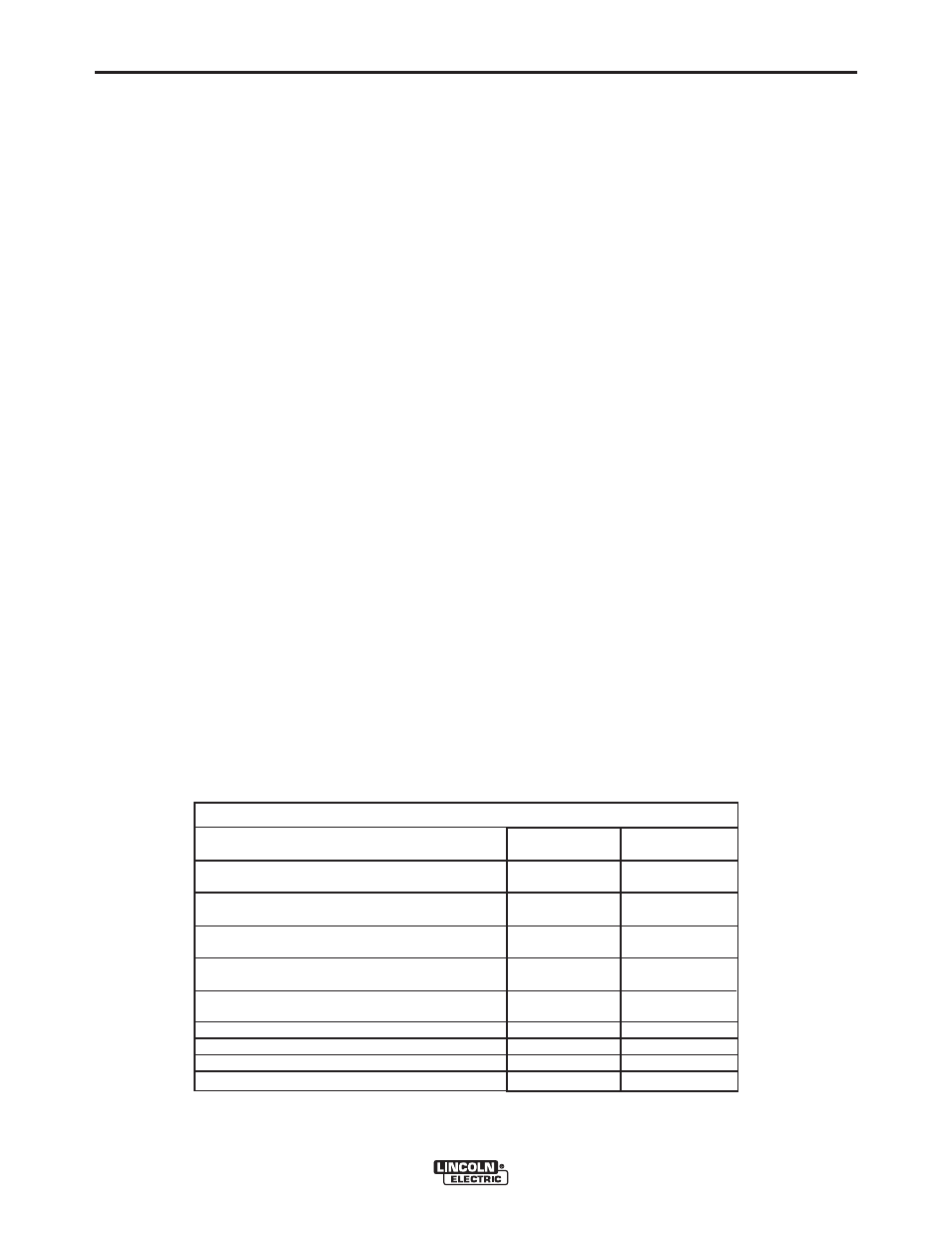
B-5
OPERATION
B-5
TIG WELDING
The TOUCH START TIG setting of the MODE switch is
for DC TIG (Tungsten Inert Gas) welding. To initiate a
weld, the OUTPUT CONTROL dial is first set to the
desired current and the tungsten is touched to the work.
During the time the tungsten is touching the work there is
very little voltage or current and, in general, no tungsten
contamination. Then, the tungsten is gently lifted off the
work in a rocking motion, which establishes the arc.
When in the TOUCH START TIG mode and when a
Amptrol is connected to the 6-Pin connector the OUT-
PUT CONTROL dial is used to set the maximum cur-
rent range of the current control of the Amptrol.
The ARC CONTROL is not active in the TIG mode. To
STOP a weld, simply pull the TIG torch away from the
work. When the arc voltage reaches approximately 30
Volts the arc will go out and the machine will reset the
current to the Touch Start level.
To reinitiate the arc, retouch the tungsten to the work
and lift. Alternatively, the weld can be stopped by
releasing the Amptrol or arc start switch.
VANTAGE® 300
TYPICAL VANTAGE® 300 FUEL CONSUMPTION
TABLE B.1
Deutz D2008 L4
Gal./Hr (Liters/Hr)
---------
.34 (1.30)
---------
.46 (1.75)
-----------
.64 (2.41)
-----------
.86 (3.24)
-------------
1.22 (4.62)
1.10 (4.15)
.89 (3.36)
.73 (2.75)
.58 (2.18)
Running Time for
15 gallons - (Hours)
--------
43.81
--------
32.46
--------
23.54
--------
17.52
--------
12.28
13.67
16.88
20.65
26.07
1400 R.P.M.
1800 R.P.M.
DC Weld Output 150 Amps @ 20 Volts
DC Weld Output 250 Amps @ 24 Volts
DC Weld Output 300 Amps @ 32 Volts
10,000 Watts
7,500 Watts
5,000 Watts
2,500 Watts
NOTE: This data is for reference only. Fuel consumption is approximate and can be influenced
by many factors, including engine maintenance, environmental conditions and fuel quality.
CONSTANT CURRENT (CC-STICK) WELDING
The CC-STICK position of the MODE switch is designed
for horizontal and vertical-up welding with all types of elec-
trodes, especially low hydrogen. The OUTPUT CONTROL
dial adjusts the full output range for stick welding.
The ARC CONTROL dial sets the short circuit current
(arc-force) during stick welding to adjust for a soft or crisp
arc. Increasing the number from -10(soft) to +10(crisp)
increases the short circuit current and prevents sticking of
the electrode to the plate while welding. This can also
increase spatter. It is recommended that the ARC CON-
TROL be set to the minimum number without electrode
sticking. Start with the dial set at 0.
DOWNHILL PIPE Welding
This slope controlled setting is intended for "out-of-posi-
tion" and "down hill" pipe welding where the operator
would like to control the current level by changing the arc
length.
The OUTPUT CONTROL dial adjusts the full output range
for pipe welding.
The ARC CONTROL dial sets the short circuit current
(arc-force) during stick welding to adjust for a soft or more
forceful digging arc (crisp). Increasing the number from -
10(soft) to +10(crisp) increases the short circuit current
which results in a more forceful digging arc.Typically a
forceful digging arc is preferred for root and hot passes. A
softer arc is preferred for fill and cap passes where weld
puddle control and deposition (“stacking” of iron) are key
to fast travel speeds. This can also increase spatter.
It is recommended that the ARC CONTROL be set to the
minimum number without electrode sticking. Start with the
dial set at 0.
Low Idle - No Load
High Idle - No Load