Val-Matic Swing Check Valve User Manual
Page 2
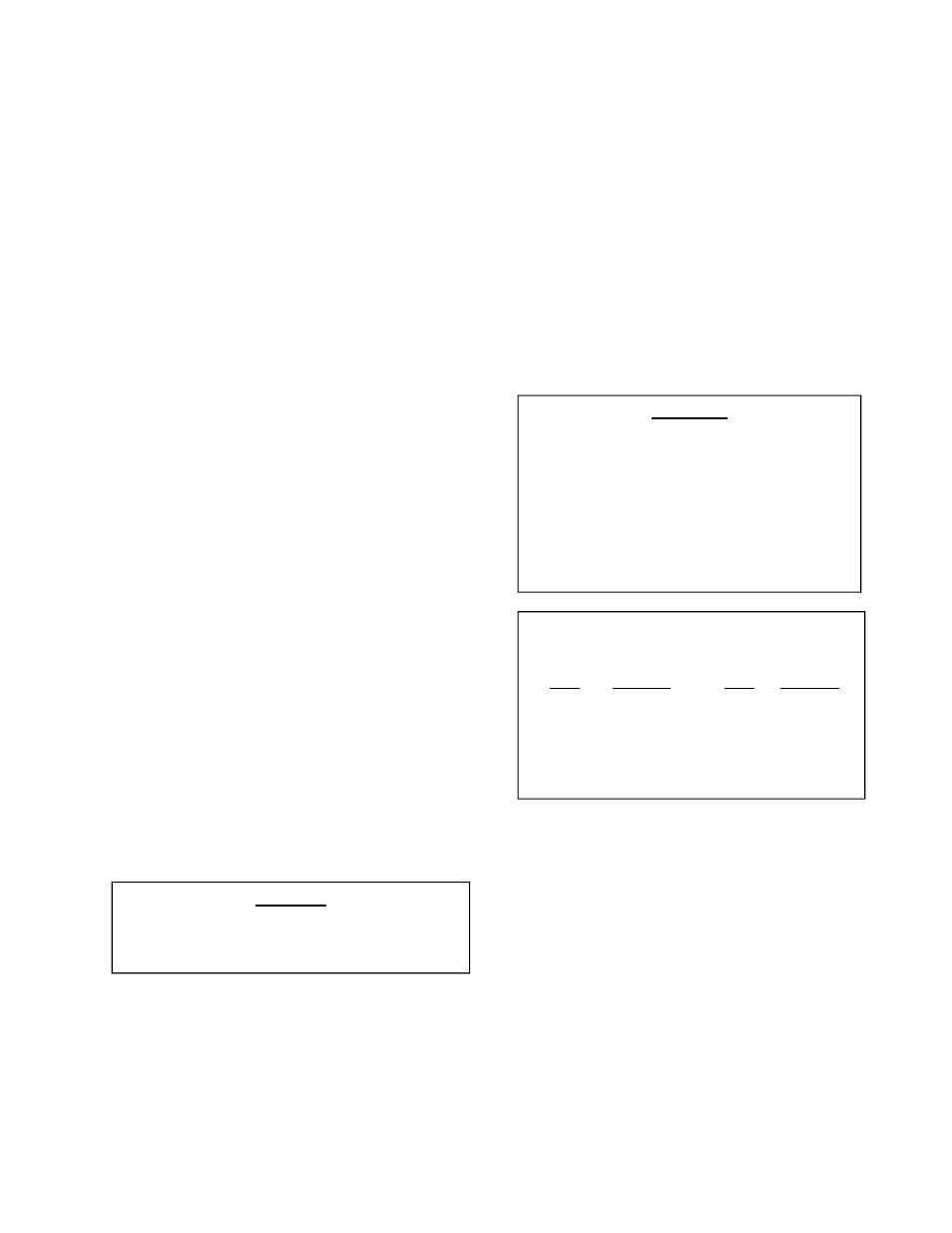
VAL-MATIC'S SWING CHECK VALVE
OPERATION, MAINTENANCE AND INSTALLATION
Page
2
of 13
INTRODUCTION
Val-Matic's Swing Check Valve has been designed
to give many years of trouble free operation. All
parts are inspected prior to final assembly to
insure complete interchangeability of parts. After
assembly, each valve receives a hydrostatic seat
test, using a pressure equal to the valves rated
working pressure and a hydrostatic shell test,
using a pressure equal to the hydrostatic shell test
pressure outlined in AWWA C508 for the valve's
flange class. The valves are designed to meet
AWWA C508 which covers 2” through 24”. The
pressure rating of the 2” through 24” is 250 psi.
The 30” through 48” valves meet the intent of
C508 and are design for 150 psi in cast iron or 250
psi in ductile iron.
This manual will provide you with the information
needed to properly install and maintain the valve
and to ensure a long service life. The valve is
opened by the fluid flow in one direction and
closes automatically to prevent flow in the reverse
direction.
Optional lever and spring, lever and weight and air
cushion may be mounted on the valve to allow for
better control of surges and valve slamming
closed.
Optional Limit Switches may be mounted on the
valve to provide local and remote position
indication.
The valve is capable of handling a wide range of
fluids including flows containing suspended solids.
The size, flow direction, maximum working
pressure, and model no. are stamped on the
nameplate for reference.
The "Maximum Working Pressure" is the non-
shock pressure rating of the valve at 150
o
F. The
valve is not intended as an isolation valve for line
testing above the valve rating.
RECEIVING AND STORAGE
Inspect valves upon receipt for damage in
shipment. Unload all valves carefully to the ground
without dropping. Valves should remain crated,
clean and dry until installed to prevent weather
related damage. When lifting the valve for
installation, make sure that lifting chains, slings or
straps are not attached to or allowed to come in
contact with the seat areas, hinge pin,
counterweight arm or the side mounted air cushion
assembly. Use hoist rings or lifting eyebolts in
cover lifting tapped holes or use hoist rings
through the flange holes on large valves.
Do not rest the weight of the valve on the hinge
pin, counterweight arm or the side mounted air
cushion assembly.
This precision equipment must remain crated,
clean and dry until installed; to prevent weather
related damage to the valve or to the pneumatic
cylinder. Improper storage and installation
procedures will void warranty.
For long term storage greater than six months, the
rubber surfaces of the disc should be coated with
a thin film of FDA approved grease such as
Lubriko #CW-606. Do not expose disc to sunlight
or ozone for any extended period.
CAUTION
Do not use valve for line testing at pressures
higher than nameplate rating or damage to
valve may occur.
WARNING
Use caution if using threaded holes in
cover for lifting the valve. All three eye
bolts should share the entire weight
directly and equally.
Use of additional slings and/or straps is
recommended for safety and ease of
orientation during installation.
Table 1. Cover Lifting Eye Bolts
Valve
Lifting
Valve Lifting
Size
Eye Bolt
Size
Eye Bolt
14”
M14
30”
M24
16”
M16
36”
M24
18”
M20
42”
M30
20”
M20
48”
M30
24”
M20