Pumptec ELECTRIC SPRAYER 12V User Manual
Page 10
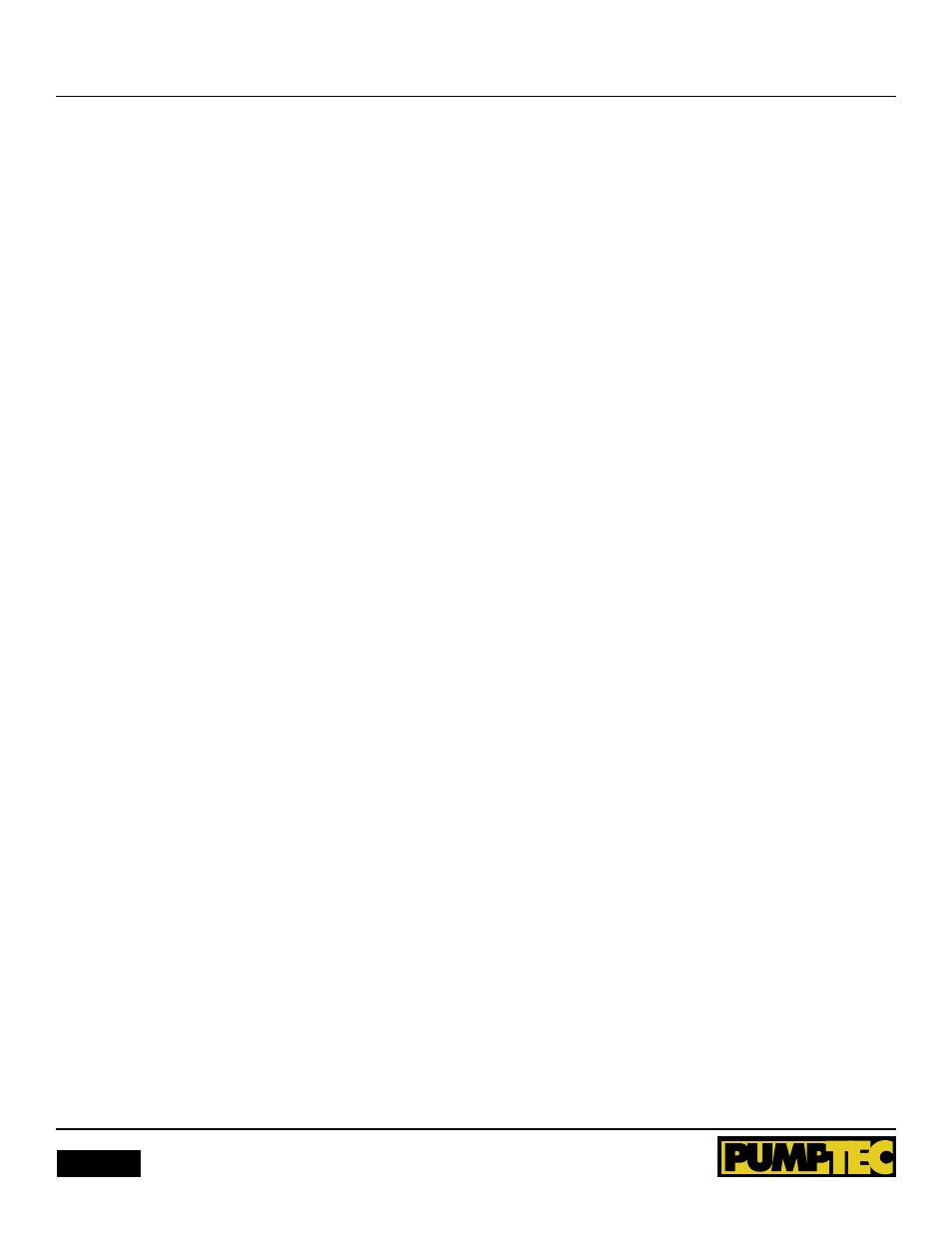
10
Version 110112
Pumptec Operating Instructions and Parts Manual
12V ELECTRIC SPRAYER
iNLEt coNditioN chEckLiSt
Inadequate inlet conditions can cause serious malfunctions in
the best designed pump. Surprisingly, the simplest of things
can cause the most severe problems or go unnoticed to the
unfamiliar or untrained eye. REVIEW THIS CHECKlIST BEFORE
OPERATIOn OF AnY SYSTEM. Remember, no two systems are
alike so there can be no OnE best way to setup a system. All
factors must be carefully considered.
iNLEt SUPPLy
should exceed the maximum flow being
delivered by the pump to assure proper performance.
• Open inlet shut-off valve and turn on water supply to avoid
starving the pump. DO nOT RUn PUMP DRY.
• Avoid closed loop systems especially with high temperature,
ultra-high pressure or large flows. Conditions vary with
regulating/unloader valve.
• When using an inlet supply reservoir, size it to provide
adequate liquid to accommodate the maximum output of the
pump, generally a minimum of 6-10 times the gPM (however,
a combination of system factors can change this requirement).
iNLEt LiNE SiZE
should be adequate to avoid starving the
pump
• line size must be a minimum of one size larger than the pump
inlet fitting. Avoid tees, 90-degree elbows or valves in the inlet
line of the pump to reduce the risk of flow restriction and
cavitations.
• The line MUST be a FlEXIBlE hose, nOT a rigid pipe, and
reinforced on SUCTIOn systems to avoid collapsing.
• The simpler the inlet plumbing the less the potential for
problems. Keep the length to a minimum, the number of
elbows and joints to a minimum (ideally no elbows) and the
inlet accessories to a minimum.
• Use pipe sealant to assure airtight, positive sealing pipe joints.
iNLEt PrESSUrE
should fall within the specifications of the
pump.
• High RPM, high temperatures, low vapor pressures or high
viscosity may increase acceleration loss of liquids.
• Optimum pump performance is obtained with +20 PSI (1.4
BAR) inlet pressure. With adequate inlet plumbing, most
pumps will perform with flooded suction.
• After prolonged storage, pump should be purged of air to
facilitate priming. Disconnect the discharge port to allow liquid
to pass through pump and measure flow.
USiNG chEMicaLS
Chemicals can be mixed into the fluid and it is necessary to
understand whether these chemicals will damage the pump or
other system components. Another way to put chemicals into
the fluid is with a downstream injector.
An injector works as a result of the difference of pressure
between the inlet side of injector and discharge side. In most
cases, the pressure on the discharge side cannot exceed 1/2
of the inlet pressure. For example, 1000 PSI into an injector
should allow up to 500-600 PSI spray pressure on discharge
side. There are dual-function nozzles that permit high pressure,
chemical free rinse and low pressure, chemical spray. These
are convenient for the operator and will not harm a properly
designed system.
The advantages of an injector are:
Fewer items touching chemical, the chemical injection rate can
be controlled, and applying chemical at lower pressure increases
chemical use efficiency.
hEatiNG FLUid
The pumps may sometimes be used with downstream heaters
and precautions need to be taken to protect the system and
persons from harm. Refer to the skilled staff at the equipment
manufacturer for guidance and proper system care. Please
be aware that heated water expands and additional pressure
release safety devices may be required.
SyStEM dESiGN
A pump is the heart of every system and proper selection is
critical to equipment function and durability. If a pumping set
with excess flow is chosen, then energy and fluid is wasted.
If excess pressure results, then equipment effectiveness can
decrease and so can pump life.
tyPicaL aPPLicatioNS aNd thEir
PerforMANce coNSIderAtIoNS
PRESSURE ClEAnIng
The optimal combination of PSI and gPM for cleaning is a ratio
of 1 gPM for every 300-400 PSI. This combination maintains
sufficient droplet size for cleaning force and distance. If the flow
is increased without an increase in pressure, the cleaning impact
does not increase with the increased use of fluid. If pressure
increases, and flow does not, then the water droplet size reduces
and has less impact force, requiring closer cleaning distances and
increased risk of surface damage.
lInE lOSS
When choosing a pump for spraying, pressure loss in the hose
must be considered. The pressure is greatest at pump and
decreases over the length of the hose. Typically, these systems
utilize very long hoses, 200-300 ft. is common, and requires
a certain minimum amount of performance to move the flow