NEWPORT iDRA Controller User Manual
Page 38
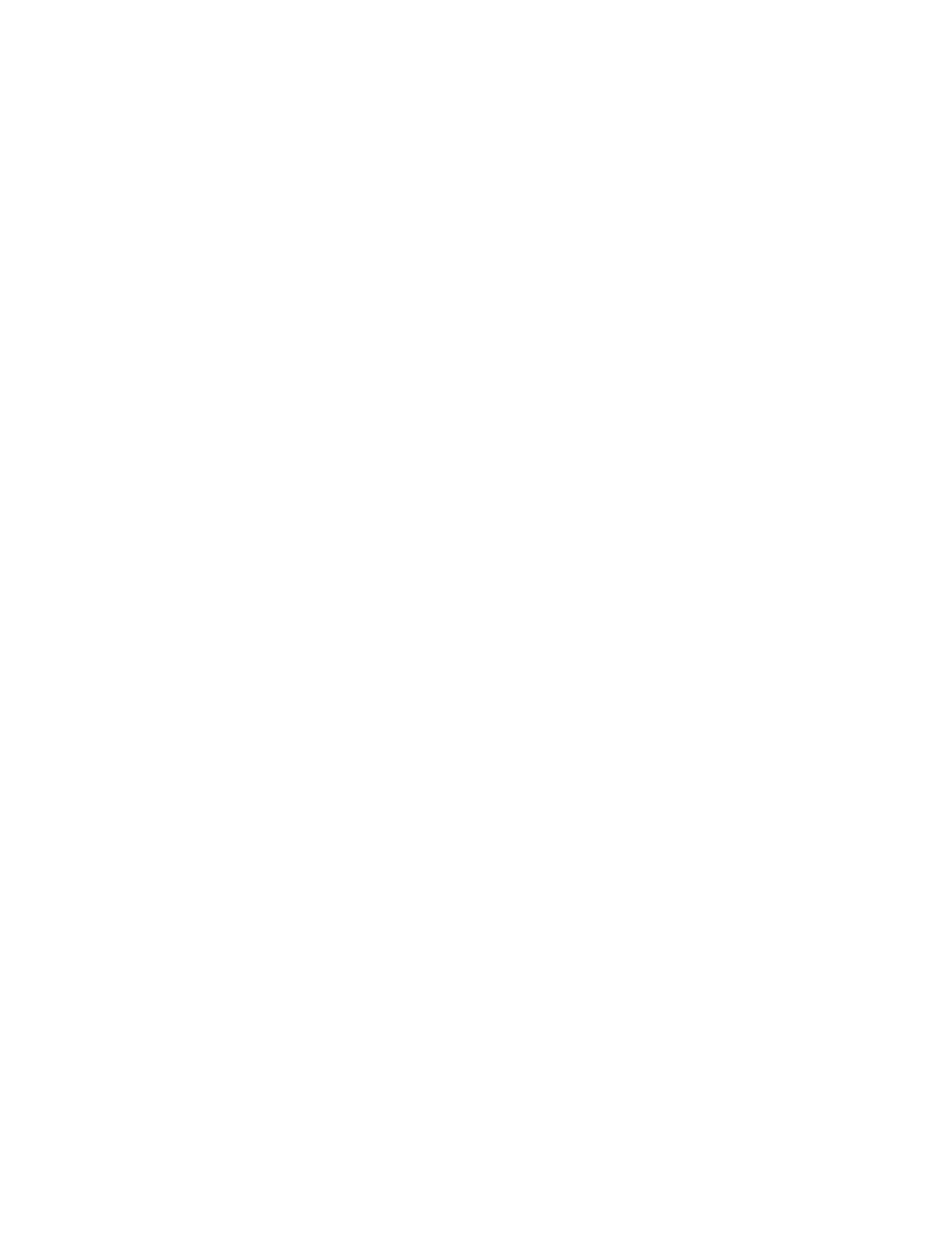
34
MAXIMUM/PERCENT HIGH SUBMENU:
Specify in percent, the maximum value (99) for control output. If the output is
time proportional (Relay, SSR, or Pulse), then the maximum duty-cycle, in
percent, is specified.
Press
d
12) Display flashes 1
st
digit of previous “Percent High” setting.
Press
b & c 13) Use b and c buttons to enter a new value for “Percent High”.
Press
d
14) Display shows
STRD stored message momentarily and then
advances to
CTRL Control Type Submenu.
Example: On an Analog Output of 0~10 Vdc, a setting of %LO = 10 and %HI = 90,
cause the minimum on the control output to be 1 V and the maximum on the
control output to be 9 V. The same setting on a time proportional output, will
cause 10% duty cycle for the minimum control output and 90% duty cycle for
maximum control output. To disable %LO/HI, set LO to 00 and HI to 99. If %LO/HI
is at other values than the default (%LO = 00, %HI = 99),
SOAK is disabled.
*CONTROL TYPE OUTPUT: (Relay, SSR, or Pulse)
Press
d
15) Display flashes
ON.OF On/Off or PID Proportional, Integral,
Derivative.
Press
b
16) Scroll through the available selections: “ON/OFF” or “PID”.
Press
d
17) Display flashes
STRD stored message momentarily and
then advances to
AçTN only, if it was changed, otherwise press
a to advance to AçTN Action Type Submenu.
The ON/OFF control is a coarse way of controlling the process. The “Dead
Band” improves the cycling associated with the On/Off control. The PID control is
best for processes where the set point is continuously changing and/or a tight
control of the process variable is required. PID control requires tuning and
adjustment of the "Proportional", "Integral or Reset" and "Derivative or Rate"
terms by a trial-and-error method. The instrument provides an "Auto Tuning"
feature making the tuning process automatic, possibly optimum.
ACTION TYPE SUBMENU:
The error that results from the measurement of the Process Variable may be
positive or negative since it may be greater or smaller than the Setpoint. If a
positive error should cause the instrument output to increase (i.e. cooling), it would
be called Direct Acting. If a negative error should cause the output to increase
(i.e. heating), it would be called Reverse Acting.
Press
d
18) Display flashes
DRçT Direct or RVRS Reverse.
Press
b
19) Scroll through the available selections: “Direct” or “Reverse”.
Press
d
20) Display shows
STRD stored message momentarily and then
advances to
AUTo only, if it was changed, otherwise press a to
advance to
AUTo Auto PID Submenu (if PID Control Type was
selected).