Lubrication & installation – Grove Gear Helical-Worm Cast Iron (S Series) User Manual
Page 8
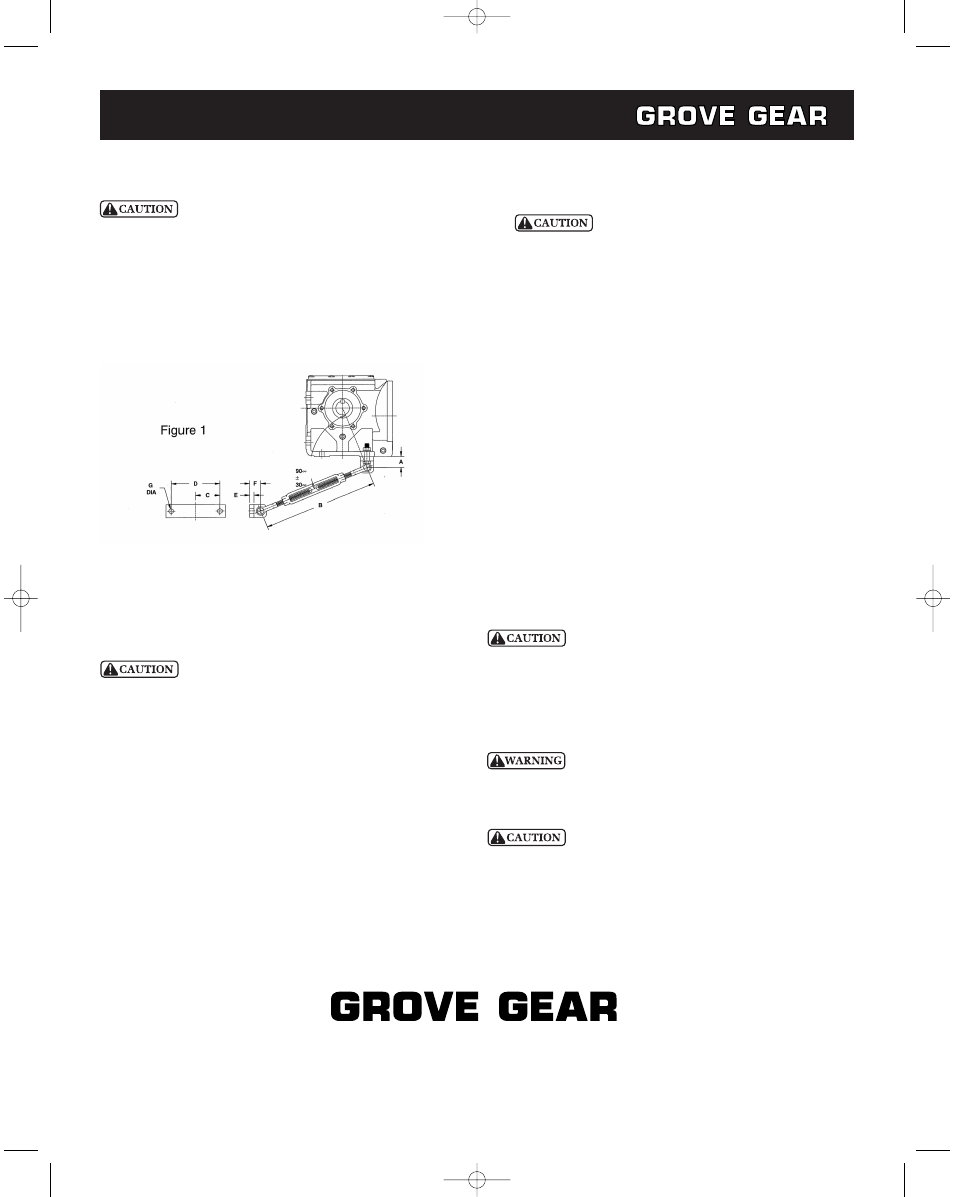
Lubrication & Installation
Flange Mounted Units
Units with the flange mount accessory are to
be mounted and supported by the mounting flange only. The
mounting pads on the housing are not to be used in
conjunction with the mounting flange to support the unit.
Shaft Mounted Units With Mounting Flange
There must be concentricity between the driven shaft and the
machine register that accepts the mounting flange pilot to
prevent misalignment between the hollow shaft of the drive
and the driven shaft.
Shaft Output Units With Mounting Flange
If coupling to shaft – flexible couplings are recommended to
minimize excessive bearing and shaft loading caused by
misalignment. Follow coupling manufacturer’s installation
directions.
The exterior holes on this drive are for
mounting the drive or drive accessories (mounting flange,
couplings, sprockets, etc.). They are not to be used for lifting
the drive or any driver/driven equipment. The lifting eye
included on this drive is to be used to vertically lift the drive
only and no other associated attachments or motors.
Electric Motor and Hydraulic Motor and Pump
Installation Instructions
For “C” Flange and Hydraulic Flange Units
1.
Be sure all of the paint and masking have been removed
from the face and pilot of the flange. Check the input bore to
be sure it contains an adequate amount of anti-seize
compound, which is normally installed at the factory. This
compound will inhibit fretting corrosion between the motor or
pump shaft and the unit bore.
2.
Install the key (if round bore) to the maximum depth of
the keyway provided in the bore.
3.
Align keyways or splines of motor or pump and bore of
unit and install motor or pump into frame.
4.
GROVE GEAR “C” flange reducers and
Hydraulic Flange Reducers are designed to accept motors with
shafts that do not exceed the maximum specified by the
N.E.M.A. or SAE standards. If the motor or pump shaft bottoms
out before the motor or pump flange seats against the
reducer flange face, the motor or pump shaft length must be
adjusted to N.E.M.A. or SAE standards.
5.
Secure the motor or pump to the unit. Capscrews and
lockwashers are provided with “C” flange units.
6.
Tightening torques for mounting bolts are provided in the
chart below.
CAPSCREW TIGHTENING TORQUE
Grade 5 Capscrews (dry, without lubricant)
Tightening Torque
Capscrew Size
(Ft. - Lbs.)
1/4 NC
8
5/16 NC
16
3/8 NC
29
1/2 NC
71
5/8 NC
143
3/4 NC
251
Mounting bolts, coupling fasteners, and other
power transmitting devices should be routinely checked
to ensure that all parts of the unit are firmly anchored to
provide proper operation. (Loose fasteners can cause
alignment problems and excessive wear). Check end play in
shafts. Noticeable movement might indicate service or parts
replacement.
Make certain that all tools and other items are
clear from rotating parts before starting machine. Stand clear,
and start machine slowly to be sure all components are
secure and operating properly.
Test run unit to verify operation. If the unit
being tested is a prototype, that unit must be of current
production configuration.
GROVE GEAR has Sales Offices and a network of Industrial
Power Transmission Distributors that can serve your needs
worldwide. Check the Yellow Pages for one near you or
contact the factory sales office.
5969G/1K/8-07/BH/BP
A Regal Beloit Company
1524 15TH AVENUE • UNION GROVE, WI 53182
PHONE: 262-878-1221 • FAX: 262-878-1968
E-MAIL: [email protected] • www.grovegear.com
HelicalWormMan,7-07 8/2/07 11:46 AM Page 8