Grove Gear E Series Right Angle User Manual
Ironman e series, Class of service
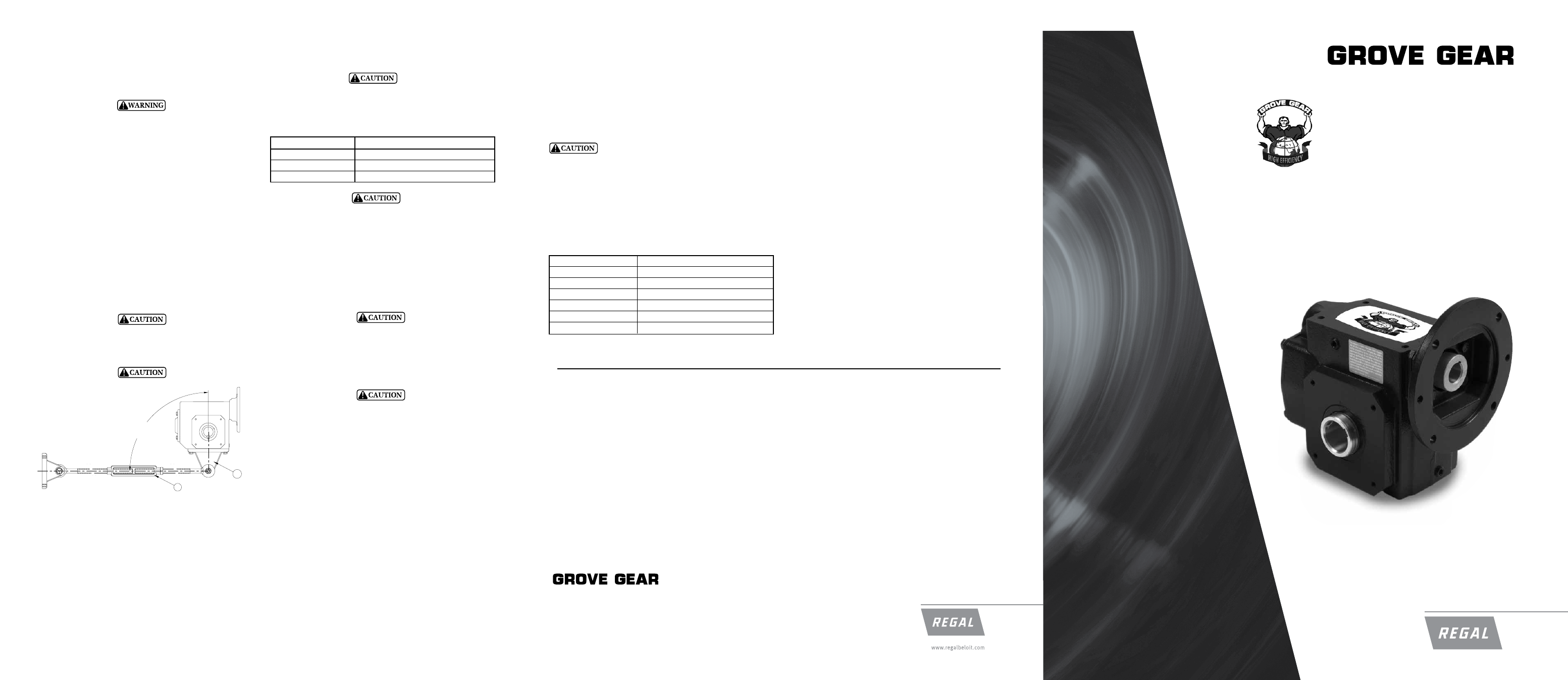
A Regal Brand
Electric Motor and Hydraulic Motor and Pump
Installation Instructions
For “C” Flange and Hydraulic Flange Units
1. Check the bore (input) to be sure it contains an adequate amount of anti-sieze compound, which is normally installed at the Factory.
This compound will inhibit fretting corrosion between the motor or pump shaft and the unit bore.
2. Install the key (if round bore) to the maximum depth of the keyway provided in the bore.
3. Align keyways or splines of motor or pump and bore of unit and install motor or pump into frame.
4. Grove Gear “C” flange reducers and Hydraulic Flange Reducers are designed to accept motors with shafts that do
not exceed the maximum specified by the N.E.M.A. or SAE standards. If the motor or pump shaft bottoms out before
the motor or pump flange seats against the reducer flange face, the motor or pump shaft length must be adjusted
to NEMA or SAE standards.
5. For stainless steel and washguard units only, install the o-ring or gasket between the motor and motor flange to prevent water and
debris from seeping in.
6. Secure the motor or pump to the unit. Capscrews and lockwashers are provided with “C” flange units.
7. Tightening torques for mounting bolts are provided in Table 4.
A parts list and print for your drive is available upon request. To obtain the proper parts list and print, you must accurately furnish the
assembly number, model number, ratio, style and shipping code as shown on the metal tag attached to the gear drive.
Class of Service
Load conditions must be within cataloged ratings published in the current Grove Gear Catalog (available upon request). Published ratings
assume lubrication with ISO 460 viscosity grade polyglycol (PAG) oil. Contact Factory for ratings when an alternate lubricant is used.
Operating Positions
Normal Speed Reducer positions are shown in the Mounting Position
Figures (refer to Page 2). For special applications, mounting position
may be inclined. However, if position varies more than 15°, it may
be necessary to make some adaptions to maintain a sufficient oil
level. Contact Factory for recommendations. Input rotation of Speed
Reducers can be either clockwise or counterclockwise.
For safe operation and to continue the unit warranty, when in-
stalling, reinstalling, or replacing a Factory installed fastener for
servicing purpose, or to accommodate the mounting of guards,
shields or other light load imposing devices, or for mounting the
unit, it becomes the responsibility of the purchaser or user to
properly determine the quality, grade of fastener, thread engage-
ment, load carrying capacity, tightening torque, and the means
of torque retention.
Couplings
Flexible couplings to input and output shafts are recommended
because they minimize bearing and gear wear caused by slight
misalignment. Follow coupling manufacturer’s recommendations
for installation and shielding.
Sheaves and Sprockets
When mounting sheaves or sprockets, the center of the load
should be located as close to the reducer as possible. Excessive
overhung loading could result in early failures of bearing or shaft.
Refer to the general catalog or contact your local distributor for
overhung load ratings. Follow manufacturer’s recommendations
for installation and shielding.
Exterior threaded or through holes on this drive are for mounting
the drive or drive accessories (couplings, sprockets, etc.). They are
not to be used for lifting the drive or any driver/driven equipment.
Inspect shafts and components for paint, burrs, or other imperfec-
tions before installing components. Do not use excessive force or
pounding to install components onto unit shafts, as this may cause
damage to shafts, bearings, or gears.
Shaft Mount Units
The Torque Arm Bracket (4A) can be attached to any of the four
available mounting surface locations of the unit.
Install and position Torque Arm (4) at 90° ± 30° to the plane (a line
drawn) between the center of the output hollow bore and the bolt
that attaches the Torque Arm (4) to the Torque Arm Bracket (4A)
of the unit. The Torque Arm should be positioned to be in tension,
NOT compression, based on output rotation of the gear reducer.
Hollow Output Protective Cover
When installing a hollow output protective cover on washdown
unit, apply a gasket sealant to the face of the cover to prevent
liquid and debris from seeping into the cover.
Excessive setscrew torque may cause damage to the output sleeves
in hollow bore units. Please refer to Table 3 for recommended
tightening torque.
Capscrew Size
Recommended Torque (lb.-in.)
1/4 NC
87
5/16 NC
165
3/8 NC
290
Test run unit to verify operation. If the unit being tested is a
prototype, that unit must be of current production configuration.
Run-In Period
A new unit will not operate at maximum efficiency during the
run-in period. Increased current draw or heat rise may be seen
during this time.
Preventative Maintenance
Keep shafts and vent plug clean to prevent foreign particles from
entering seals or gear case. Inspect periodically for oil leaks.
Mounting bolts, coupling fasteners, and other power transmitting
devices should be routinely checked to ensure that all parts of the
unit are firmly anchored to provide proper operation (loose fas-
teners can cause alignment problems and excessive wear). Check
end play in shafts. Noticeable movement might indicate service
or parts replacement is necessary.
If the unit cannot be located in a clear and dry area with access to
an adequate cooling air supply, then precautions must be taken
to avoid ingestion of contaminants such as water, and to avoid a
reduction of cooling ability due to exterior contaminants.
Important Information
In the event of the resale of this E Series Speed Reducer (unit), in
whatever form, resellers/buyers will include the following language
in a conspicuous place and in a conspicuous manner in a written
agreement covering such sale:
The manufacturer makes no warranty or representations,
express or implied, by operation of law or otherwise, as to
the merchantability or fitness for a particular purpose of the
goods sold hereunder. Buyer acknowledges that it alone has
determined that the goods purchased hereunder will suitably
meet the requirements of their intended use. In no event will
manufacturer be liable for consequential, incidental, or other
damages.
Resellers/buyers agree to include this entire document,
including the warnings and cautions listed herein, in a
conspicuous place and in a conspicuous manner to instruct
users on the safe usage of the product.
4A
90°
±30°
4
TORQUE ARM FIGURE
Table 3 - Setscrew Tightening Torques
Table 4 - Grade 5 Capscrews
Capscrew Size*
Tightening Torque (ft.-lbs.)
1/4 NC
8
5/16 NC
16
3/8 NC
29
1/2 NC
71
5/8 NC
143
3/4 NC
251
* Grade 5 Capscrews (dry, without lubricant)
A Regal Brand
Ironman E Series
Installation, Lubrication and
Maintenance Instructions
Grove Gear
Union Grove, Wisconsin 53182
PH: 262-878-1221
FAX: 262-878-1968
grovegear.com
© 2014 Regal-Beloit Corporation 7741G/2.5K/04-14/NP/MERIDIAN